Pump manufacturers have a long, successful history of working with metals and are familiar with the beneficial properties they deliver in a variety of pumping applications. Similarly, the pump industry has been using thermoplastics in pump designs for several decades because of their low cost, light weight, superior chemical resistance, manufacturability and other valuable—and profitable—advantages. While unmodified thermoplastic resins have many inherent benefits, they also pose many limitations for pump applications if used in an unmodified form. Chief among these limitations are strength, impact, wear resistance and flame-retardant properties that can often fall short of those same properties in metals. Despite these setbacks, manufacturers have a broad range of options for enhancing the properties of unmodified resins. Compounders can add combinations of reinforcing fibers, fillers and additives to a carefully selected base resin to create a high-performance compound with a host of distinct properties instilled into a single material. Many manufacturers are frequently surprised at the diversity of properties that can be readily built into a compound—including flame retardancy, impact resistance, strength, wear and friction resistance, conductivity, temperature resistance, chemical resistance, corrosion resistance and colorability—to deliver the exact performance criteria that they have specified.
Developing the Right Formulation
The job of the compounder is to first understand the pump application and its challenges and then consider the wide variety of base resins, reinforcing fibers, fillers and additives in its portfolio to develop the optimum formulation. Experienced compounders can begin with lower cost base resins such as polypropylene for less demanding applications, higher-temperature resins such as polyphenylene sulfide (PPS) and polyetheretherketone (PEEK) for more demanding thermal and wear requirements, or fluoropolymers such as polyvinylidene fluoride (PVDF) and ethylene tetrafluoroethylene (ETFE) for extreme chemical resistance. From this base resin, the compounder works to create the composite using a combination of reinforcing fibers, fillers and additives such as long glass fiber to increase mechanical properties or the internal lubricant polytetrafluoroethylene (PTFE) for reduced wear and friction. Other options include aramid fibers, graphite or ceramic powders for improved wear resistance, halogenated or non-halogenated flame-retardant additives, conductive carbon fiber, and pigments and dyes for custom color options. Depending on the challenges presented by the application, some of these formulations may be created from scratch with no base resin in mind, while others may begin with previously developed resin/additive combinations. During the development stage, manufacturers often continually request additional properties. For example, they may begin by requesting that strength be added to the compound. Later, they may ask for a flame retardant and finish off by requesting that the compound be made the company's corporate color. An experienced compounder is often able to accommodate these requests, but compounding technology requires balance and compromise of ingredients and properties. Sometimes, when one performance criteria is added, issues may arise with others. For example, imparting conductive properties may result in reduction of overall strength or impact resistance for which the formulation must compensate. A skilled compounder understands how different constituents of the formulation interact, as well as their advantages and limitations.Maximizing Compound Strength
Compounders use a variety of reinforcing fibers, including short glass fiber, carbon fiber and very long glass fiber, to achieve maximum strength and other specific properties. The manner in which these fibers are introduced into the melt stream and the sizing chemistry used on the fiber are key considerations when striving to maximize material strength. As an example, a manufacturer was looking to convert components of a fluid-handling pump that moves waste products at up to 155 gallons per minute (gpm) from metal to a thermoplastic. Polypropylene was considered because its weight savings were projected at 20 to 50 percent and the manufacturing process was relatively quick and easy. Because of the inherent properties of polypropylene, the manufacturer achieved excellent chemical resistance but was unable to obtain the required level of tensile strength. After carefully analyzing the application, the compounder selected a 40 percent long glass fiber reinforced polypropylene, with a 17,500 pounds per square inch (121 megapascal) tensile strength and 5.0 foot-pounds per inch (267 joule/meter) notched izod impact strength that met all structural and impact requirements of the application. The long glass fiber reinforcement, with its unique balance of strength and impact properties, allowed the manufacturer to benefit from the use of a thermoplastic compound, a scenario that otherwise would have been impossible because of the inherent strength deficit of the polypropylene alone.Incorporating Superior Wear Resistance
Another property of enormous consequence to pump manufacturers is wear and abrasion resistance. Despite the large number of moving parts, pumps must provide a long useful life with minimal downtime while maintaining effective operation in corrosive, high-temperature and other inhospitable environments. To incorporate wear resistance, the compounder can select an additive technology, such as PTFE, perfluoropolyether (PFPE), silicone, carbon and aramid fibers, graphite and molybdenum disulfide. As illustrated in Figure 1, wear resistance (per American Society for Testing and Materials D3702) can be improved in inherently wear-resistant materials such as nylon 6/6 and acetal (POM) by incorporating PTFE alone or in combination with PFPE.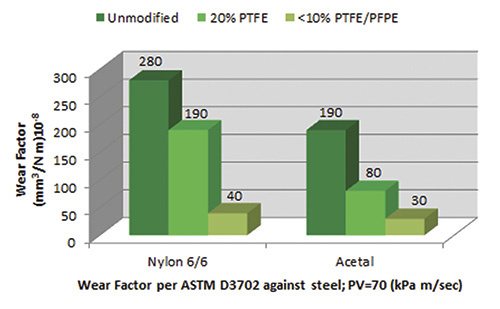
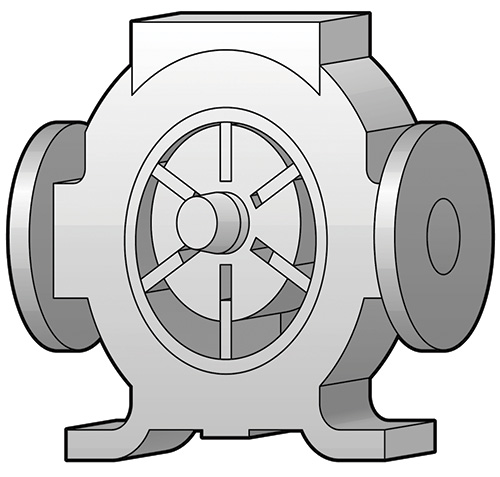
Compounding: A Key to ATEX Success
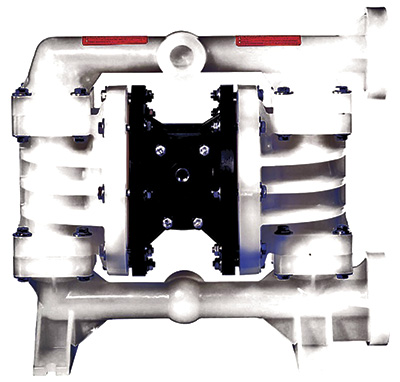