A facility in this island nation installed new technologies to meet continuous high water demand without changing the building’s footprint.
08/01/2016
Faced with continuous high water demand and increasing energy costs, the Cyprus Water Development Department decided to upgrade its desalination plant in Larnaca, Cyprus, an island nation off the coasts of Syria and Turkey. While the plant’s production capacity met the department’s requirements, its owners were challenged to optimize the efficiency of the plant without changing the footprint of the existing building. To meet this goal, the Larnaca plant was updated with improved high-pressure (HP) pumps and advanced work exchanger-type energy-recovery devices (ERDs), as well as other state-of-the-art technologies. The new design exceeded the project’s efficiency targets and reduced maintenance.
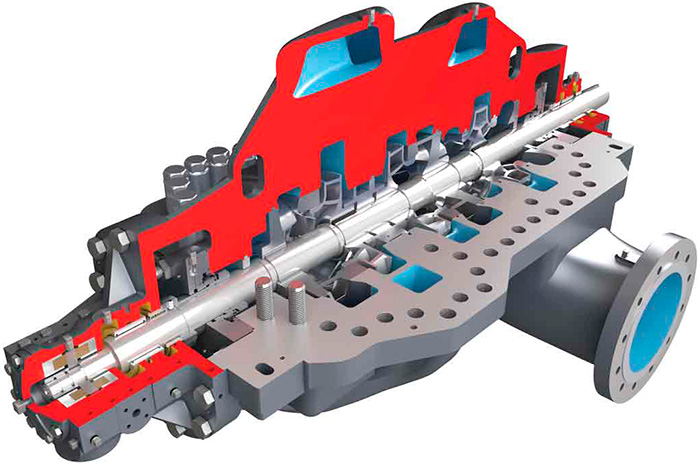
Building on Success
The Larnaca desalination plant was constructed in 2000 and commissioned in 2001. The facility was originally equipped with turbine/motor/pump units, including energy-recovery turbines (ERT), the most efficient ERD available at the time. To further increase capacity and performance, the plant was upgraded to a maximum capacity of 64,000 cubic meters per hour (m3/h), or 16 million gallons per day (mgd). “The system ran successfully and very reliably for 10 years, with an availability exceeding 99 percent,” said Richard Long, director of product management, engineered product operations, for the pump supplier. “A decade later, though, water demand and energy costs were both rising fast.” When the original 10-year contract expired, the Cyprus Water Development Department issued a tender for a new desalination plant to be built within the existing facility layout. M.N. Larnaca Desalination, a consortium of Mekorot Development & Enterprise Ltd. and Netcom Co., won the bid.Economical Design
To achieve the most economical design, plant personnel decided to use fewer but larger seawater reverse osmosis trains. Instead of the original six trains, the new design was reduced to two significantly larger trains with higher-efficiency pumps and isobaric work exchangers, rather than the previously used ERTs. This equipment is more efficient, and the capital cost of fewer large, high-pressure membrane feed pumps is lower than that of more smaller units. In addition, each of the new trains was outfitted with energy-efficient variable frequency drives (VFDs). “We installed variable frequency drives on the intake, HP feed and energy recovery system (ERS) circulation pumps to ensure maximum efficiency under changing conditions,” Long said.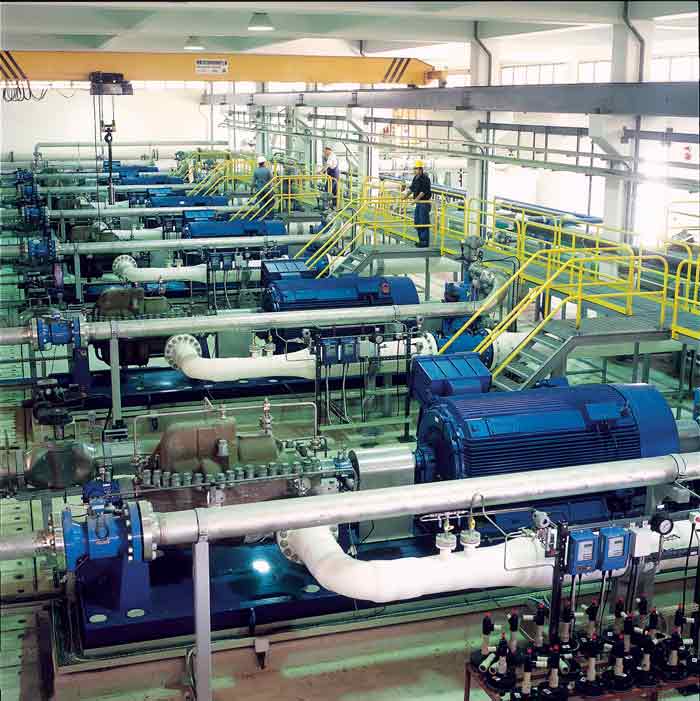
HP Pump Efficiency
To meet the new HP pump capacity and head requirements, the end user selected an axially split, three-stage centrifugal pump. With a redesigned continuous crossover that extends more than 180 degrees, the selected pump is designed to reduce crossover losses by 40 percent. “The pump achieved a best efficiency point of 87.5 percent when installed,” Long said. Ringless impellers, Stellite-overlaid stationary rings and impeller hub, and channel rings with 360-degree guide vanes also contribute to greater pump efficiency, improved reliability and less maintenance.ERS Efficiency
While improvements to the ERS were critical from the start, they soon became an even bigger concern. After the contract was signed, energy costs in Cyprus surged from €0.15 per kilowatt-hour (kWh) to more than €0.20/kWh. To optimize capital versus operational costs, the existing brine evacuation of the previously installed ERTs was reused. As a result, both the head and power consumption of the low-pressure feed pumps could be reduced. The user conducted an analysis to determine the optimal number of work exchanger ERDs that should be used. The goal was to optimize the differential head and simultaneously build in additional spare capacity. The analysis showed six ERDs per train to be ideal for this installation. To fit the larger trains within the constraints of the existing space, the user determined that the optimal design involved installing the electrical-driven linear actuators and patented linear valves in the vertical position. The new train design also included:- super duplex hydro-formed vessels, delivering
- extremely high accuracy with 100 percent
- radiographic inspection to ensure the highest
- possible integrity
- double-seal pistons, reducing leakage to 0 percent
- a low-maintenance check valve designed for lowest differential head
- an electrical actuator to ensure maximum control and simplicity with minimal maintenance