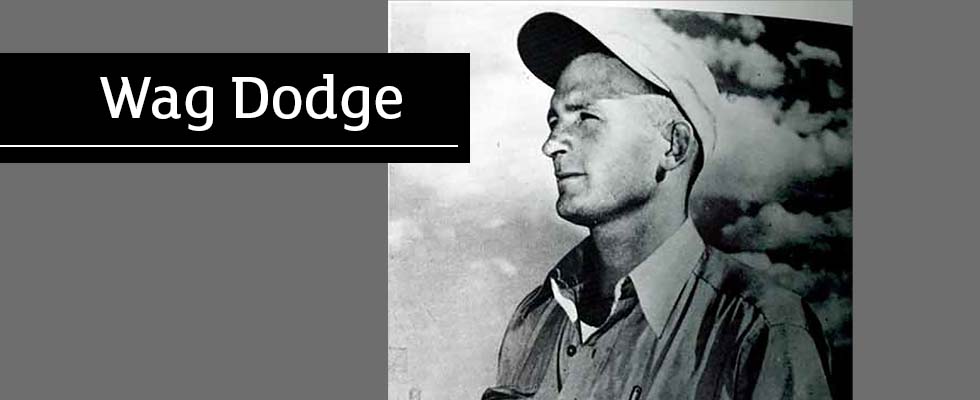
On Aug. 5, 1949, a wildfire was reported along the upper Missouri River in Montana’s Helena National Forest. A team of 15 smokejumpers parachuted in to fight the fire as it was engulfing an area called “Mann Gulch,” which had a steep-sided ravine on both sides of a small stream. As the smokejumpers came close to the fire, high winds suddenly ramped up, causing the fire to expand and cutting off the team’s route, forcing them back uphill. A “blow-up” of the fire covered 3,000 acres in 10 minutes, but just seconds ahead of the blow-up, the foreman, Wag Dodge, started an escape fire to provide a clear path for his crew to exit the fire safely. He threw himself into the ashes of the fire he started and survived, but most of his men were not trained properly on the benefit of an escape fire and instead ran in the opposite direction, their last moments obscured by smoke. The fire claimed the lives of 13 firefighters, including 12 of the 15 smokejumpers.
This story has been used as an analogy for many industrial trainings. Training effectiveness is measured by the impact on the trainee’s knowledge, skills and performance. But often, by the time you need to remember your training, it is already too late.
Gasket training can be considered something to speed through and an unexciting topic to cover. There are even times when gasket installation techniques have been handed down—from older worker to new trainee. Sometimes this information transfer is important and follows the technology, but there are many times when poor, inaccurate information is handed down. The results of this can be disastrous. Doing things incorrectly again and again will catch up to users and lead to serious issues.
A zero-tolerance policy to the installation of sealing devices is critical to maintain a safe workplace. Everyone wants to come home from work safely, and for this to occur, adherence to active training is critical. By training employees on best practices, the number of incidents that occur can be majorly reduced. It is an organization’s responsibility to do everything in its power to keep its employees safe, and training is a key preventative measure to be taken.
One issue still seen that highlights this idea is putting anti-seize on a gasket surface. Putting anti-seize on a gasket can (depending on service conditions) help the gasket come off the flange more easily. The trouble with this practice is that it is at the expense of gasket performance. Is it more important to want a gasket that can be removed easily or a gasket that leaks or blows out? The anti-seize reduces the grip of the gasket to the flange, creates volume loss when the anti-seize volatilizes and can chemically attack the constituents of a gasket.
Another area where poor training occurs is tightening bolting using only a wrench. There have been many studies that demonstrate massive load discrepancies when tightening using a basic wrench and a mechanic’s feel versus using a torque wrench, but the practice still occurs. It is like the people who did not follow Dodge’s lead when the fire came up the hill.
The Fluid Sealing Association (FSA) reviewed 100 gasket failures and, after doing a root cause analysis, realized that 68% of the failures were due to under-compression of the gasket. In that same study, 15% failed because the wrong product was used in the wrong application. With these facts in hand, it seems important that bolt tightening skills be included in any part of a good maintenance training program. However, as seen in the field, bolt loading training is not taken as seriously as it should be. For example, many plants do not have a plant-standard bolt lubricant that is used by all employees and contractors so that all torque calculations can be used with the same coefficient of friction (K factor). Many times, journeymen at a plant are using torque tables to get the torque for a bolted connection. In small print at the bottom of these tables, it states the K factor they were designed around—but they have not been updated based on the K factor of the bolt lubricant being used in the plant.
It is also important to review the condition of the bolting in a bolted connection. The lack of gasket compression results from poor transmission of bolt tightening to bolt load. This can be seen from not realizing the bolt condition as one of the most important factors in bolting. Torque is not tension. This is a mantra that comes to mind during any tightening process. Too often people will interchange the words—thinking they mean the same—but they do not.
Torque is the turning force or work applied to the bolt that in perfect conditions will result in a certain amount of stretch (tension) in the bolt. The relationship also must deal with other factors including bolt condition, coefficient of friction and torque wrench accuracy, to name a few.
Gasket material selection is important. A real-life example regarding incorrect gasket materials happened a few years ago. At 4:15 p.m., Sunday, Nov. 25, 2018 (Thanksgiving weekend), ethylene oxide (EO) was accidentally released into the air from an EO plant in Delaware. The Delaware Memorial Bridge was closed for five hours as a precautionary measure because of the hazardous nature of EO, which is flammable and toxic. No injuries to plant personnel, responders or nearby residents were reported, but shutting down one of the most traveled roads in America during one of the most traveled days of the year inconvenienced thousands. Investigations by the company and the state determined the release was caused by a failed flange gasket on the water reboiler piping, servicing the purification column. The gasket used was of a material not suitable for the operation. This is another example of how critical gasket selections are in hazardous service.
Lifelong learning and training are critical for maintenance workers, engineers and planners. Making sure this training provides the latest methods and techniques can lower the risk of an accident and keep plants running longer.