Temperatures, altitude and humidity can cause problems that may surprise unprepared users.
09/21/2015
While many companies provide solutions for power plants, customizing their technologies for difficult environments may be challenging. Some extreme ambient conditions that trouble users and providers include the following:
- extreme heat, with ambient air temperatures up to 55 C
- extreme cold, with ambient air temperatures as low as -60 C
- extreme annual variations, with peak to peak variations in temperature of more than 70 C
- extreme humidity, with ratios of more than 25 g/kgdry air
- extreme altitude, reaching heights of greater than 4,000 meters above sea level
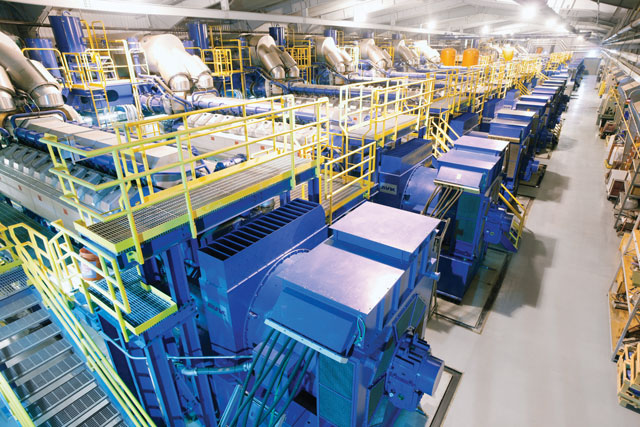
ISO 3046 Standard
The International Organization for Standardization (ISO) 3046-1 standard gives guidelines for how engine manufacturers can communicate engine performance data to power plant operators and helps the operator compare different engines and conditions. A diesel-fueled, turbocharged, medium-speed, four-stroke engine with charge-air cooling has three main correction factors: suction air temperature, charge air coolant temperature and total barometric pressure. Equations 1, 2 and 3 show the basic calculations: Px = α x Pr Equation 1 Where: Px = power at site conditions Pr = power at standard reference conditions α = power adjustment factor, which can be calculated using Equation 2 α = k – 0.7(1 – k) ((1/ηm) – 1) Equation 2 Where: ηm = mechanical efficiency k = ratio of indicated power, calculated using Equation 3 k = ( px / pr )m ( Tr / Tx )n ( Tcr / Tcx )s Equation 3 Where: px = site total barometric pressure in kilopascals (kPa) pr = standard reference to total barometric pressure, 100 kPa m = total barometric pressure ratio factor, 0.7 Tr = standard reference to suction air temperature, 298 K (25 C) Tx = site suction air temperature (K) n = suction air temperature ratio factor, 1.2 Tcr = standard reference charge air coolant temperature, 298 K (25 C) Tcx = site charge air coolant temperature (K) s = charge air coolant temperature ratio factor, 1 These factors have been selected for their direct impact on the working conditions for diesel engines. The total barometric pressure is directly related to the site altitude. The higher the site, the lower the pressure and air density. As a result, the turbocharger supplies less air to the engine, even if it, in part, compensates the difference in air density by rotating faster. The suction air inlet temperature affects both the turbocharger speed and the total engine heat load, as warmer air has a lower density. The turbocharger speed will increase but will actually supply less air to the engine. In addition, an increase in temperature results in increased component temperatures, known as thermal load. Finally, the charge air coolant temperature directly relates to the air temperature entering the cylinders and affects engine component temperatures and combustion pressure. According to the ISO 3046-1 standard, “In the case of turbocharged engines where the limits of turbocharger speed, turbocharger turbine inlet temperature and maximum combustion pressure have not been reached at the declared power under standard reference conditions, the manufacturer may declare substitute reference conditions to or from which power adjustment shall be made.” Based on this, one manufacturer employs the following substitute reference conditions: Px = α x Pra Equation 4 Where: Pra = power substitute reference α = power adjustment factor, calculated in Equation 2 k = ( Px / Pra )m ( Tra / Tx )n ( Tcra / Tcx )s Equation 5 Where: Pra = substitute reference total barometric pressure, 100 kPa Tra = substitute reference suction air inlet temperature, 308 K (35 C) Tcra = substitute reference charge air coolant temperature, 318 K (45 C) These limits are a result of rigorous testing and years of experience in the power production industry. They represent the most optimal work point for engines under normal conditions. This optimization takes into account the turbocharger inlet temperature, turbocharger speed, combustion pressure, component temperatures, emission levels and efficiency. The limits may require project-specific adjustments to match special conditions and may also be subject to revision due to process optimization and engine development.Maintaining Reliability
By optimizing the engine, the cooling system and the plant design and by adjusting the substitute reference conditions, users can make the engine operate at close to optimal working conditions throughout the seasonal changes of a whole year, even in extreme conditions.Extreme Heat
The ISO 3046-1 standard defines the basic control and performance of the engine in increasing temperatures. But other challenges, such as a method for adequately cooling the engine’s lube oil, are not addressed in the standard. The obvious solution is to improve the cooling system so that it can maintain the required lube oil temperature, even in extremely hot ambient conditions. One ideal solution is a wet cooling system, such as cooling towers or raw water cooling. In extremely hot conditions, however, it is usually also extremely dry, making wet solutions expensive and unsustainable. This shows the benefit of dry solutions, namely that there is no water consumption. The fundamental advantage of producing power with almost no water consumption has been a key driver in engine development during recent years. As a result, there are solutions today that enable dry cooling methods with little or no impact on the power output even in extremely hot conditions. As power plants grow in size, they also start to exhibit their own microclimate caused by the circulation of hot air from external heat sources, the cooling system or the engine itself. If this hot air is reintroduced to the engine or cooling system, it may cause performance degradation. Manufacturers use computational fluid dynamic (CFD) simulations for evaluating risks, developing solutions and verifying results, while fighting this phenomenon. In some cases, extremely high air temperature and low density resulting from elevation may cause the standard turbocharger to reach its mechanical limit, even if the traditional design and control philosophies are being followed. In such cases, it is necessary to implement new solutions that can be based on hardware, software or both.Extreme Cold
When a power plant must operate at temperatures below 0 C, it is vital that antifreeze is added to the cooling water. Otherwise, expansion of the freezing cooling water could cause parts of the cooling system to crack and break. Even if no mechanical failure occurs, ice will block the coolant flow, jeopardizing cooling performance. Propylene glycol is a commonly used antifreeze agent. With 20 percent glycol and 80 percent water, the freezing point is lowered to -8 C. However, antifreeze also affects properties other than the freezing point. It lowers the specific heat value (cp), lowers the thermal conductivity (λ), increases the dynamic viscosity (μ), and increases the density (ρ). The change in the specific heat value of the cooling water has the greatest effect. A lower specific heat value means that a constant change in temperature (ΔT), in a constant mass flow (ṁ), will result in a lower energy transfer (Q̇) (see Equation 6) Q̇ = ΔT x ṁ x cp Equation 6 Plants must compensate for the lower heat transfer by increasing the temperature difference, meaning that the charge air coolant inlet temperature is lowered. At the same time, the substitute reference charge air coolant temperature must be lowered, so that the maximum heat load occurs at conditions corresponding to what the system performance would be without glycol. This adjustment realigns the performance window so that it coincides with the optimal heat load performance.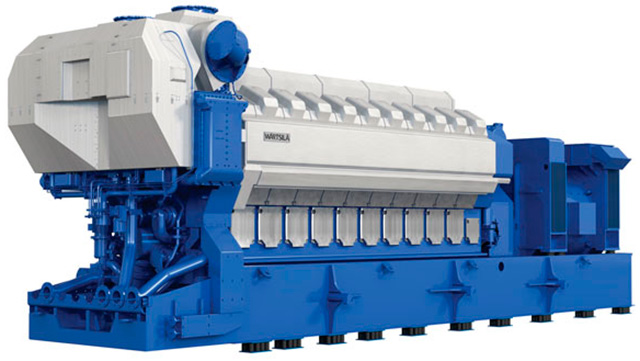
Extreme Temperature Variations
Some parts of the world, such as inland Russia, experience extreme temperature variations, from the cold of winter to the heat of summer. Although this does not explicitly create any new challenges, it does combine the different challenges from both hot and cold conditions. One notable effect of this combination is that the cooling deficiency caused by glycol may create challenges in keeping the engine sufficiently cooled during hot periods. Users must evaluate the combined solution, identify possible synergies and eliminate any overlapping functionalities.Extreme Humidity
According to the ISO 3046-1 standard, turbocharged engines do not need any correction for humidity. But humidity can significantly affect engine performance, since high humidity may lead to condensation of water vapor in the charge air cooler. Some effects of condensation include:- corrosion of engine parts, such as the charge air cooler, valves, receiver and cylinder liners
- acid formation through the combination of liquid water and sulphur, which will cause aggressive corrosion
- loss of mass as a result of the extraction of the liquefied water through drains
- risk of water stroke if the drains are not working properly
- increased heat flux but with less cooling