When dealing with a construction site that is underwater or where the water table is just above sea level, contractors must ensure that the excavation stays dry and safe for workers. This can be even more challenging in locations with conditions affected by water depth and complications like silt and sand. Additionally, these difficult conditions may vary during seasonal weather or with the tides. Contractors need to investigate historical data and monitor fluctuations in water levels and speeds of flow to decrease the risks for workers and ensure the success of the project. The contractor must decide what pumping equipment to use based on the hydraulic conditions. Jobsite conditions—such as flow required to mitigate water seepage, depth of a coffer dam and solids content—influence this decision. The contractor usually chooses between self-priming centrifugal pumps or submersible pumps.
Self-Priming Centrifugal Pumps
One weakness of end-suction centrifugal pumps is their poor performance when the liquid is below the pump centerline. Liquid must be delivered to the pump so the process can begin. Air on the suction side of the pump (the piping and pump casing) needs to be completely evacuated. If any air remains in a centrifugal pump, the pump becomes air bound and incapable of functioning..jpg)
Submersible Pumps
Submersible pumps offer many operational and application advantages. These pumps are submerged directly into the water for immediate use and unit cooling. This eliminates priming challenges and extended prime times. No worker intervention is required. The pump is fed without the need for a suction line. Submerged pumps are quiet. Cavitation is rare and occurs primarily when the sump is too small for the installed submersible pump’s size. They are also lighter weight and portable. The versatility and low maintenance of submersible pumps make them an ideal option for dewatering service. No regular maintenance is necessary. Submersible pumps usually need to be fully submerged. The water around a submersible pump actually cools the motor.Case Study: Reconstructing Galveston
The sea level along the Gulf Coast is rising faster than most places on the globe. Galveston, Texas, has experienced a 3-foot rise since the disastrous flood of 1900 that killed thousands of people. One of the toughest jobs in rebuilding the infrastructure of a city that is just a few feet above sea level is keeping water out of the construction site—particularly water that is laden with sand. Pumping a water/sand slurry is tough on pumps, especially aluminum dewatering pumps. Boyer Construction experienced this condition while working in Galveston. Galveston Island, located in Southeast Texas, runs west to east and is slightly tilted to the northeast end, where the city of Galveston is located. The north side of the island opens up to a protected harbor, and the southern side faces the Gulf of Mexico. Before the 1900 hurricane— which still holds the record of the most deadly natural disaster in American history with 6,000 deaths—the highest point in Galveston was 9 feet above sea level. After the 1900 hurricane, a 17-foot high, 3-mile long seawall was built to protect the city and its people from other storms. The entire city was raised to the edge of the seawall. Then the island was sloped down 8 feet above sea level on the north side, so that water rising over the seawall would drain into the bay. This engineering feat, which took more than 10 years, was accomplished by pumping a sand and seawater slurry under existing buildings to raise the island. The seawater ran off, leaving the sand and building up the island. Since then, Galveston has experienced other hurricanes, but none have had the same impact as the great 1900 storm. In September 2008, Hurricane Ike devastated Galveston Island along with the Bolivar Peninsula and Gilchrist, Texas, with sustained winds of 110 miles per hour, and a 22-foot storm surge. Property damage was estimated at $29.5 billion, and 135 people died in the U.S. because of the storm. The downtown area of Galveston had 6 feet of standing water in the aftermath. As is always the case after a hurricane impacts a populated area, the rebuilding and damage-repair effort took years of hard work and millions of dollars. One of the companies that worked to rebuild Galveston was Boyer Construction.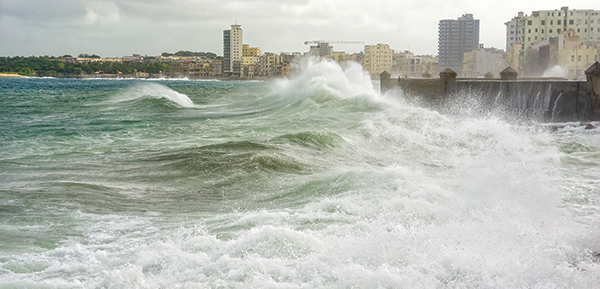