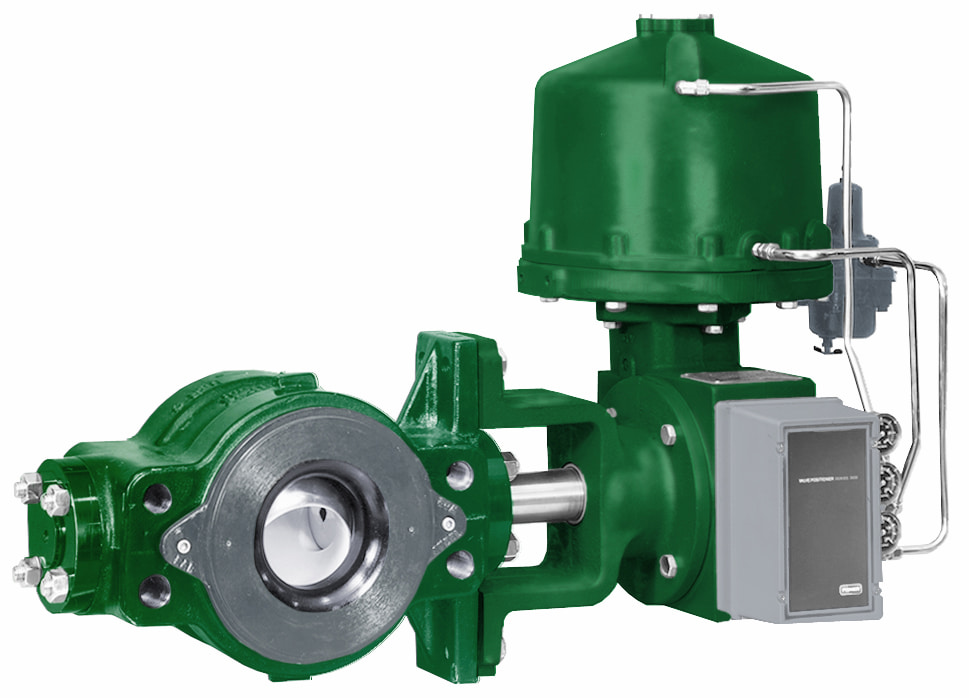
Final control elements (FCEs) play an important role as part of basic process control system (BPCS).
A process control loop for BPCS—consisting of a transmitter, controller and control valve—operates under dynamic conditions, with outputs constantly being adjusted for process control.
Clear understanding of failure mechanisms for electronic components and mechanical parts will help end users design their BPCS related field devices more optimally and accurately.
This will help eliminate initial premature failures and unnecessary plant trips during normal operation. It also will help end users determine what systems are fit for purpose, which will result in capital cost savings.
Mechanical valve assemblies used for the FCE of a BPCS are at the heart of process control. Optimal process plant performance depends upon the proper function of the FCE.
While FCEs are the main driver of process control, industry concerns are centered on plant availability, loop performance and field equipment ruggedness.
The valve assemblies can experience changed process conditions. Unlike electronic devices, the degradation of mechanical items occurs in definite form depending upon application, process fluid, physical properties of fluid, pressure drop, temperature, operational history, maintenance philosophy and environmental conditions.
Mechanical valve assemblies with pneumatic accessories inherently have limitations related to functionality. Their calibration, configuration and zero/span processes are manual—and often complex—requiring a high level of user expertise.
These issues also contribute to a longer installation and commissioning time.
In addition, several reliability issues may affect mechanical valves.For example, external factors—like air quality, temperature, humidity, etc.—may cause abnormal aging of the soft parts and pitting in the terminal box, while other environmental conditions could lead to corrosion of parts and linkages.
Vibration can trigger a calibration shift, and it can also cause loss of travel feedback and the dropping off of mechanical linkages. General wear can lead to instability and spurious valve behavior.
Mechanical valves can be prone to under-performance with potential issues, including high process variability and the valve not tracking the controller. Advance process control requires tighter controls, while there are more productivity and throughput requirements.
Plant maintenance philosophy and regulatory requirements mandate regular preventive maintenance to avoid any mechanical catastrophe, but with growing economic pressure and competitiveness, many process industries work with an extended turnaround period. This makes it important to predict the health of mechanical valves in advance, before any unforeseen issues arise.
However, because mechanical valves have no diagnostics, there is no easy way to predict valve health. Manual inspection is time-consuming and laborious, requiring frequent site trips. There are also no remote capabilities for data collection and analysis.
Using Digital Valve Controllers
With the advent of digitalization, a microprocessor-based digital valve controller can aid predictive maintenance by providing a valve degradation analysis, which is important for critical valves in control applications. This can reduce the amount of scheduled maintenance.
Installation does not affect the ability of a plant to migrate its FCE from a non-intelligent to a digital solution. All that is required is to switch the current conventional instrument to a smart, microprocessor-based intelligent instrument.
Microprocessor-based digital valve controllers have been used in the industry for some time. These smart positioners have fulfilled the traditional function of converting a current signal to a pressure signal to operate the valve.
They can also use digital communications protocols to provide simple access to the information critical to process operation, and to deliver the capability to integrate this information into a control system.
This means that the controller can aid predictive maintenance by providing a valve degradation analysis, which is important for critical valves in control and safety applications. This reduces the amount of scheduled maintenance.
By communicating through a variety of industry-specified protocols the controller links with the digital ecosystem of industrial internet of things (IIoT) to tie data, applications and organizations together.
The extensive diagnostics available to digital devices provide greater insight into the health of control valves, allowing potential failure conditions to be predicted before they occur.
A digital valve solution offers functionality from the outset, with auto-calibration, user-friendly configuration and a set-up wizard. It delivers accurate, precise control of the valve, with a range of instrument alerts available.
A Predictive Maintenance Approach
Communication options transmit critical device health data, which can be used to predict future valve performance. This allows valve maintenance to move from a preventative process to predictive.
This can improve reliability and allows for wider access to valve experts, both within the plant and located externally, who can use the data to drive valve performance enhancements and reduce loop variability.
Digital valve controllers can help identify potential problems including:
• poor seat condition
• internal galling
• downstream restriction
• crossover adjustment
• feedback interference/loose linkages
• actuator and tubing leaks
• travel sensor failure
• friction
• bad pressure sensor
• tuning
• I/P and relay problems
• lever misalignment
• supply pressure starvation
A predictive approach streamlines maintenance, making it easier to ensure the right spares are ordered at the right time, without storing them for long periods.
Shutdown, turnaround or outage planning is also improved, since the areas which need the most urgent focus can be determined by taking the digital valve signature (like an X-ray), while valves are still in line, saving considerable cost of stripping the valve from pipeline and taking to workshop for repair.
Valve signature is great help in pin-pointing probable areas of concerns (valve body related issues like seat area, bonnet portion, packing leak, or actuator related aspects, like pressurized path leak, over travel, damaged diaphragm, etc.). This helps to reduce the amount of time required, which is crucial to start up the plant and considerable cost savings by only handling portion of valve assembly, which require repair.
In addition, by continuously maintaining low process variability through controlling the valve near to required controller demand, plant efficiency is improved, and unplanned shutdowns are prevented.
By monitoring valves on a regular basis, those valves with deteriorating performance can be identified and put right, avoiding a potential failure which could cause plant shutdown, environmental damage, or personnel risk.
Online monitoring is able to define the problem and identify the possible cause of the issue, the remedy and any recommended action.
To provide an example, a digital solution was used to monitor final control elements in a power plant. The diagnostic detected a problem with a specific portion of valve assembly and issued a yellow light warning with list of likely causes in the event log.
Further monitoring indicated that the pneumatic part had degraded further, causing a red light to be issued. The data supported the original indication that a detected component was responsible.
After applying the recommended action, increasing supply pressure to remove the obstruction in the pneumatic path, normal operation returned. This avoided a costly shutdown.
Digitalization also allows data to be obtained remotely rather than sending personnel to hazardous or hard-to-reach areas. Likewise, technicians can also calibrate and configure control valves directly from the control room.
By combining digitalization with a predictive maintenance approach, repairs of control valves can be scheduled in advance to avoid unplanned shutdowns and reinforce process safety.
This results in savings in the operation and maintenance budget, while also ensuring the plant is run in a safe, optimal way.