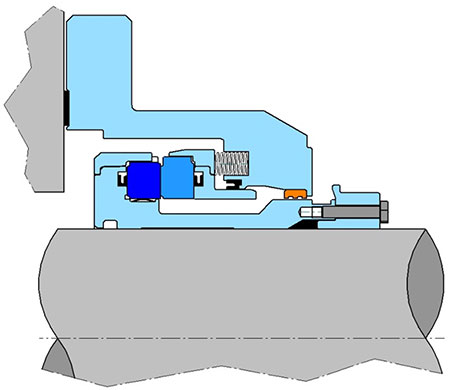
In 1965, a then 31-year-old, well-motivated learner accepted a job offer from a big company in the oil refining and chemical manufacturing industry. In his first year of employment, the mechanical engineer was given three projects. Their common scope was to define equipment and process efficiencies and, to the extent possible, these were to be expressed as profit margins. Working on three projects simultaneously was the most efficient way to keep busy and fine-tune this engineer’s learning skills.
Although completed within their scheduled 14-month time frame, none of the three projects were deemed ready for commercialization in the 1960s. Their proposed implementation simply did not meet the corporation’s then prevailing profitability hurdles or thresholds. However, 57 years later, smaller players are actively marketing the three technologies that were the subjects of the screening studies in 1965:
- oils made from jojoba beans
- roofing materials made from bagasse
- closed-cycle power generation packages for large resort hotels and other potential users in the Caribbean as well as similar locations not connected to highly industrialized locations with large power grids.
It can be shown that the smaller players became profitable because they periodically reassessed and readjusted to situations and adopted the technological tools that evolved in the years and decades after 1965. Given this context, additional data points of interest are brought to the reader’s attention next. The message: Reassess facts and move forward. Refuse to become stale and arrogant. Adjust thinking and include living space and the environment in future plans.
Jojoba beans
Jojoba beans are waxy diesters that contain 50% oil by weight. The beans grow on shrubs that thrive in dry soils and can be harvested in deserts. Jojoba oil is the liquid produced in the seed of this plant; it is native to southern Arizona, southern California and northwestern Mexico. The technology may respond favorably to commercial scale-ups that produce biodiesel. Who might be the likely beneficiaries of such scale-ups and conclude that design shops and manufacturing facilities might have to be built? Structured apprenticeship programs would be given a boost, and pollution would be reduced. Although engine output would decrease by as much as 15%, neither the owner nor consuming public would lose if such commonsense approaches were to replace the present pursuits.
Bagasse
Bagasse is a plant residue; typical residues include the outer layers of sugar cane and grape vines. The authoritative Wikipedia defines bagasse as the dry pulpy fibrous material that remains after crushing sugarcane or sorghum stalks to extract their juice. The outer layers are used as a biofuel to produce energy in the form of oil, heat and electricity. In some countries, bagasse is widely used in the manufacture of pulp for cardboard, paper and other building materials. We have reason to believe that full-scale commercialization would be both beneficial and profitable. Eliminating waste can be a real profit proposition.
Gas turbine and piston engine
Gas turbine and piston engine utility packages are among the many solutions that can be considered for energy conversion in general. Of course, they find application primarily in power generation services. If suitable volumes of gaseous fuel are available, users consider these before evaluating the various liquid fuel options. However, other approaches exist and have become even more important in 2022 than they were in 1965. They certainly deserve to be investigated and implemented whenever they can result in reducing stress on the environment. Environmental stresses are at an extreme, and their true cost far exceeds lowball estimates.
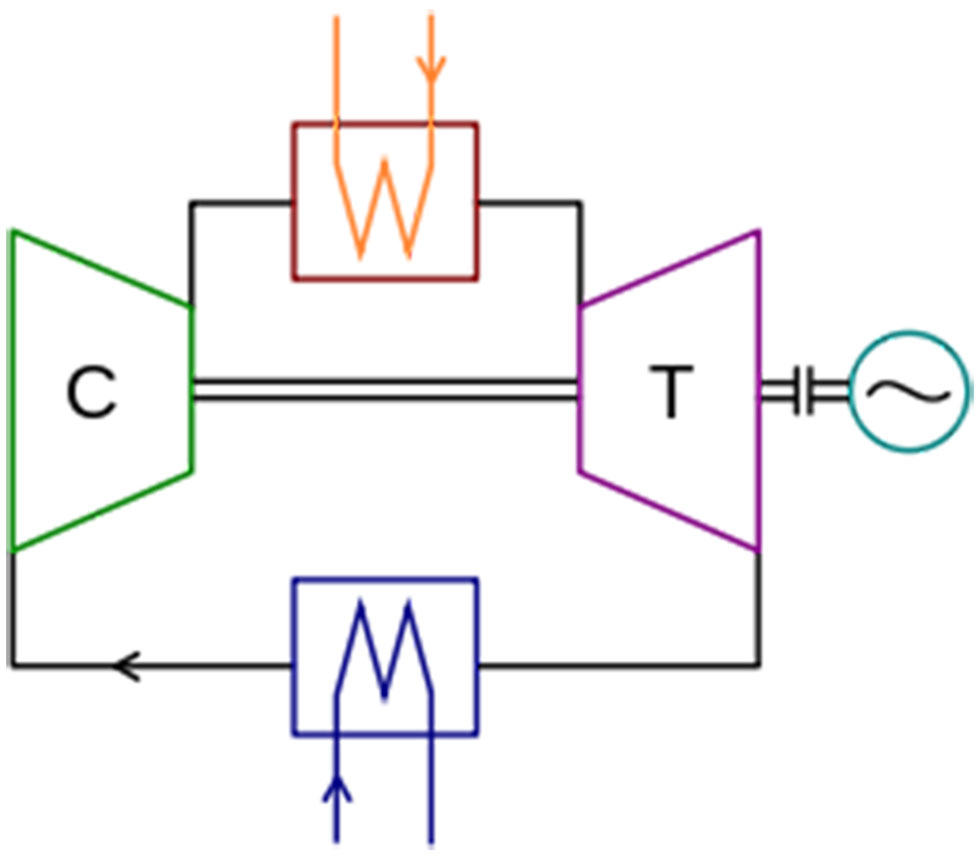
As a general rule, closed-cycle gas turbines are fluid machines that use a gas such as air, nitrogen, helium, argon, etc., for the working fluid in a closed thermodynamic system (Image 1). Heat is supplied from an external source, see the red heat exchanger (HX) element and note that cooling takes place in the blue HX element. Such recirculating turbine arrangements follow the Brayton cycle. Today’s modern reciprocating piston engines should be in contention as well. They are among the oldest generator drivers but were later pushed towards the background when gas turbines gained prominence as the low-maintenance driver.
Gas turbines are indeed capable of satisfying the needs of power generation applications across different industries. These largely range from food and beverage applications that start around 200 kilowatts (kW) to large-scale industrial and municipal projects. The overall efficiencies of sets consisting of piston engine driver, gear and generator typically range from 40% to 50%. This compares favorably with that of small gas turbines or any other conventional power generation technology. Both piston engines and gas turbines can work in combination with other types of equipment, renewable energy sources or battery storage, thus increasing the efficiency and flexibility of the overall system. Finally, gas-fueled piston engines are used successfully to modernize or repower current power generation infrastructures. In other words, the old assumption that gas turbines are one’s best choice is not always correct. Successful large-scale municipal plants proved it a long time ago.
Advantages of Closed Cycle Arrangements1
A closed-cycle gas turbine has the advantage over its open-cycle counterpart in that it can utilize dirty fuels such as residual fuel oil, coal or lignite. Further, there is practically no loss in thermal efficiency at part load, and waste heat can be rejected at temperatures up to 700 F (370 C) for use in downstream industrial processes. The system has the disadvantage in that the peak turbine inlet temperature is limited to 1,500 F (815 C) by stress and corrosion in the heat exchanger located between the combustion products and the turbine working fluid. A review of 40 years of research and development effort on closed-cycle gas turbines combined with over 30 years of commercial experience with a dozen systems in Europe indicates that, if used just to produce electric power, they yield a system a little higher in capital costs and a little lower in thermal efficiency than a conventional steam system. However, if a dirty fuel is to be used for cogeneration applications where the ratio of the heat energy required to the electrical energy produced is less than four, particularly if the heat is required at temperatures greater than 212 F (100 C), both the efficiency and utilization of the energy in the fuel and the capital costs are more attractive for a closed-cycle gas turbine than for a steam system.
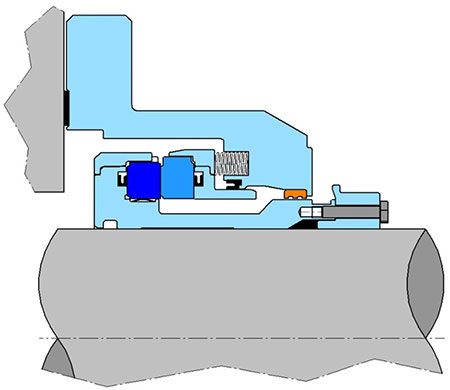
IMAGE 2: Cross-section view of modern steam turbine gland shows its nonrotating flexing components sealed and centered by U-cup style high-temperature elastomers (Image courtesy of AESSEAL)
Closed systems allow prompt access to electrical and thermal energy. This is especially important for energy-deficient regions and for locations that cannot connect to centralized energy sources. Closed systems give improved reliability of the electric power source for locations with unstable grid infrastructure and facilities demanding high energy supply reliability. Phasing out segmented carbon rings is advantageous. Equipping fluid machines with the modern sealing glands shown in Image 2 would cut back on fugitive emissions that pollute air and water.
Time to Consider Environmental Facts & Rethink Old Assumptions
Today, the planet we call home is in serious distress, and old ways of thinking are obstructing needed progress. Collectively, we should never abdicate our ethical obligation to be well-informed professionals. So, make it a priority to lead, follow or get out of the way. There can be no nobler endeavor than making cleaner air our common future. Discover the facts on emissions and pollution. Start by making honest appraisals, and then drive the push for lasting change.
References
Fraas, A. P., “Summary of Research and Development Effort on Closed Cycle Gas Turbines,” Oak Ridge National Laboratories Report TM-6237, 1981.