During the feasibility stage for any new mine, one of the fundamental questions is: How can the ground be kept dry enough for mining to be carried out efficiently and safely? The majority of mines around the world involve working below the natural water table where, if no action were taken, the areas would be completely submerged. Mines above the water table experienced the ongoing challenge of groundwater ingress from rainfall. Unless this water is removed and kept out, mining is impossible. The importance of a mine’s dewatering system cannot be overstated. If it fails or is unable to remove enough water, the consequences can be severe—such as costly and potentially lengthy delays; compromise to critical structures; and in the worst-case scenario, risk to miners’ lives. A large number of complex considerations must be kept in mind when designing a dewatering system, including:
- The depth of the water table
- The porosity and permeability of the ground
- The amount of surface water present
- The presence of geologic features, such as underground rivers or water pockets
- The level of precipitation and its seasonal variations
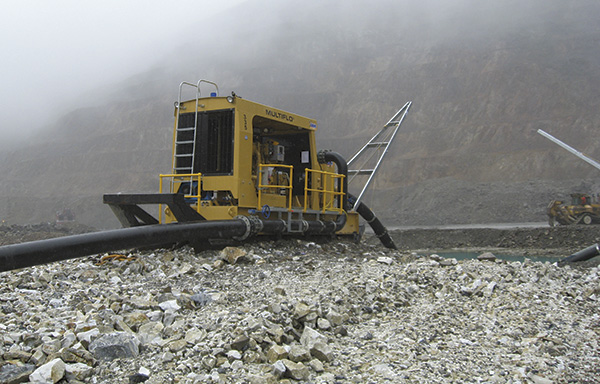
Planning
In the absence of the geological surveying methods and processes available today, dewatering provisions at most mines in the past were determined by a trial-and-error process. Pumps would typically be sized and installed on approximated values and operated manually based on the water levels in the pit. If the water extraction rate was not adequate, the system would be manually adjusted by removing or adding pumps. Modern feasibility studies for mining projects involve a lengthy and detailed modelling process. It is so thorough that pump positioning and the flow and head requirements required are commonly mapped out in advance for the duration of the project. For a large operation, this can be a period of several years. Once the inflows have been calculated, a dewatering system is specified with a capability that exceeds the maximum requirements that could foreseeably be presented by the project, such as an extended period of unusually heavy rainfall. Unexpected changes to underground water systems may also be encountered, which could necessitate higher flow capabilities from the system.Location
Normally, the main dewatering pump system will be positioned at the lowest point in the pit or shaft, and the water will be pumped to the surface. This may be supplemented by a feeder system of smaller pumps at other low-level points that do not drain sufficiently to the pit bottom. These pumps usually transfer the water from these additional areas to the central point before the main dewatering pump lifts it to the surface. Occasionally, for larger, open-pit projects, deep shafts are drilled around the pit and water is pumped out of these to lower the water table across a wider area. As the mining develops by either lowering or widening the mined area, new stages of the dewatering system may be required. Typically, an additional pump will be added for every 70 meters descended. This multistage system can usually be replaced by a more efficient and more powerful single-stage arrangement when the mine reaches its maximum depth.The Right Tools for the Job
The correct specification of the complete dewatering system goes beyond the selected pump types. The other design features—such as sump design, pipeline sizing and valves—are equally critical. By far, the most commonly used dewatering pumps are horizontal centrifugal or submersible pumps because they offer a good balance of easy deployment and high performance levels. Centrifugal pumps can be single-stage units arranged in a multistage configuration, which are capable of generating pressures up to 70 bar. Multistage centrifugal pumps can also be used, although this type may provide limited solids-handling ability. Beyond the capabilities of these pumps, positive displacement pumps that can generate significantly higher pressures but at lower flow rates would be deployed. The equipment selected for any given situation depends on the performance required and the practical questions of space and accessibility. In some instances, the operators’ working preferences may be considered in the equipment specifications. The pumps are either diesel or electrically driven, and the power source choice is largely based on the preference of the operator and existing practices onsite. Furthermore, for underground operation, particularly in mines, the presence of hazardous gases must be considered, which will require the use of suitably rated equipment that is certified by the relevant authority. This affects the complete pump systems and not just electrical drives and controls.Smart Control
Pump drive and control technology advancements have helped dewatering systems become more adaptive to weather conditions. Optimum flow requirements can be achieved by employing variable frequency drives and sophisticated programmable logic controllers that can increase or decrease individual pump speeds and start up or shut down the pumps’ operation to adjust for the inflow requirement. This increase in complexity has created a demand for remote and automated functionality so that operators do not have to physically be at the pump to make system adjustments. This automated control may include inputs via flow rate, pressure or level sensors and can significantly increase operational efficiency.Efficiency Versus Ruggedness
Historically, clear liquid-handling pumps have generally had higher hydraulic efficiency because they do not need to make allowances for handling solids. Slurry pumps, on the other hand, are designed to handle fluid that often contains large particles, so the internal designs vary significantly. Typically larger and heavier, slurry pumps have increased clearances between the impeller vanes and the volute to ensure free passage of larger particles and to reduce wear. This requirement usually means a slurry pump will deliver lower energy efficiency when pumping clear water. However, recent developments in slurry pump designs because of advanced modelling methods have allowed them to deliver efficiencies that rival some clear-water pumps. Dewatering applications fall somewhere between the two because they require performance levels similar to clear-water pumps in terms of flow, head and efficiency but need to be able to handle some solids particles—typically not exceeding around 10 percent.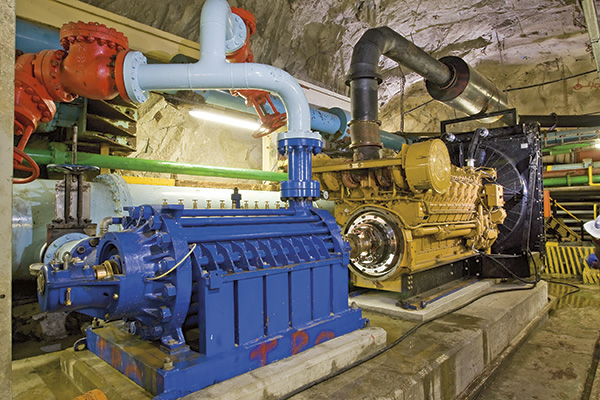