A damaged condenser vacuum pump and high temperatures put operations at risk.
02/06/2015
Unexpected maintenance or repairs can represent a major expense to end users. The costs of parts, labor and production downtime compound to create serious problems for any facility. Many users find it helpful to implement proactive maintenance policies that allow them to plan for and minimize these expenses. Advanced predictive analytic solutions can enable users to monitor component performance and detect problems early, helping them design and carry out effective proactive maintenance.
Unhealthy Vacuum Pump Detected
In November, a software monitoring solution detected an increase in condenser backpressure at a combined-cycle power plant. The backpressure moved from 1.16 inches of mercury (inHg) (0.039 bar) to 2.27 inHg (0.076 bar) and continued to rise to as high as 3.15 inHg (0.107 bar) in early December. Once detected, the remote monitoring and diagnostic (RM&D) team sent an email notification to the end user, who investigated the issue the following day. The end user learned that the high condenser backpressure was caused by an unhealthy condenser vacuum pump. The pump was swapped out, and the condition improved.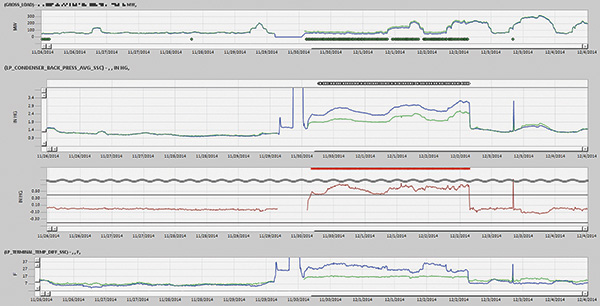
High Bearing Temperatures on Pump at Coal Plant
In early September 2014, a software solution detected an increase in the motor outboard bearing temperature for a condensate booster pump (CBP). Temperatures rose as high as 170 F (77 C), while expected values were 150 F (66 C). Concurrently, the pump outboard bearing temperature for the sister CBP rose as high as 150 F (66 C). The RM&D team sent an email notification to the user and began tracking this issue on weekly calls.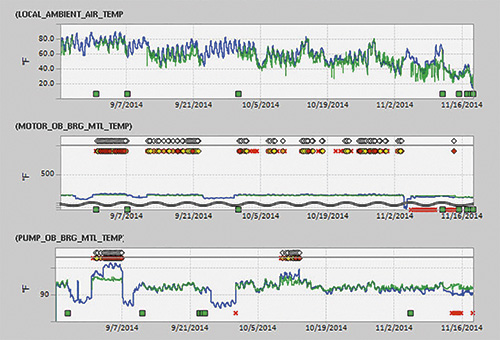
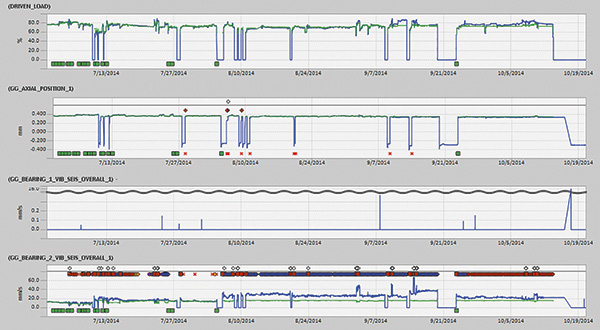