Q. How does a liquid’s viscosity affect the performance of rotary sealless pumps? A. The viscosity of a pumped fluid affects the input power and magnetic coupling torque required in a rotary sealless pump. When selecting magnetic couplings, users should consider the maximum pressure differential, speed and viscosity. These factors determine the pump’s required input power and torque. To calculate the torque requirement of the magnetic coupling, the torque required to overcome viscous friction between the inner magnet and the containment shell must be added to the pump input torque. When handling high-viscosity liquids, users must consider suction lift, port size, friction losses and reduced pump speeds. Users selecting a sealless rotary pump should also evaluate the effect high-viscosity liquids have on the temperature rise of the magnetic coupling. These liquids may reduce the amount of cooling flow, causing increased temperature rise within the coupling. Starting torque for a pump that was previously primed with viscous pumpage can be a problem unless consideration has been given to coupling sizing. A soft-start device may avoid decoupling on startup. When pumping low-viscosity liquids, traditional concerns are poor lubricating qualities and slippage. Users should also consider the liquid temperature, temperature rise and vapor pressure when applying a rotary sealless pump. The temperature of the liquid in the coupling should be below the vaporization point of the pumped liquid. If viscosity increases with shear or temperature, additional torque could be required, and increased heat buildup in the drive section may occur. For more information, see the Hydraulic Institute (HI) Standard American National Standards Institute (ANSI)/HI 4.1-4.6 Sealless, Magnetically Driven Rotary Pumps for Nomenclature, Definitions, Application, Operation, and Test. Q. What type of bearing is recommended for use in slurry pumps, and how are these bearings sealed? A. While antifriction ball or roller bearings are used on most slurry pumps, hydrodynamic bearings may be used on some large slurry units. Bearings may be grease or oil lubricated, and bearing housings must be effectively sealed from leakage and outside contamination. Labyrinth seals, bearing isolators, lip seals and other proprietary seals are commonly used. Contact seals include all designs that have dynamic contact as a requirement for proper function. These are recommended for applications in which the seal must retain a static level or pressure differential. Labyrinth seals consist of a simple gap seal with labyrinth grooves and possibly a gravity drain. Labyrinth grooves help retain splash oil lubrication, but they rely on a simple gap for contaminant exclusion. Bearing isolators have a stationary and a rotating component that act in concert to retain lubricant and exclude contaminants.
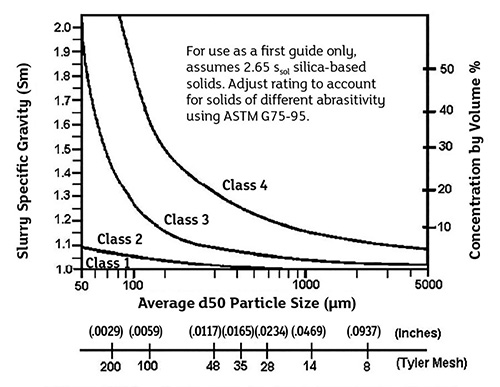
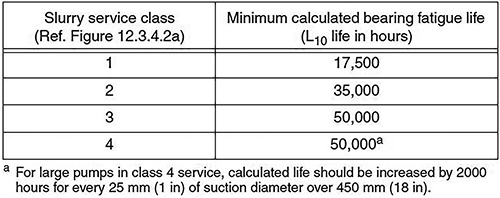