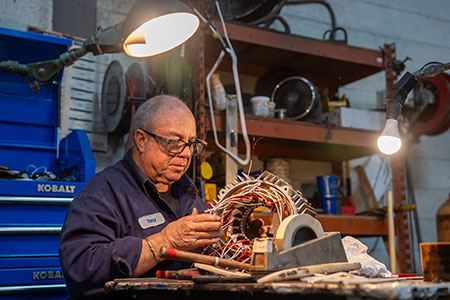
According to the International Energy Agency, globally, the combination of all kinds of motor electricity demand is estimated to be about 45%, with the United States, China and the European Union leading the way. Recognizing the significance of high-quality electric motors in production raises the question: How does rewinding an electric motor impact its efficiency and longevity?
Standardization Is Not Everything
Many articles discuss the importance of engineering and testing undertaken to ensure motors meet or exceed OEM standards. Reputable repair shops typically possess similar equipment and adhere to Electrical Apparatus Service Association (EASA) repair standards. So, what sets one repair apart from another? To answer this question, users need to delve into the manufacturing process and understand the materials used in manufacturing versus a rewind.
Material Matters: A Closer Look
Interactions with OEMs can often involve finding ways to reduce costs and enhance production. OEMs, while not always opting for the cheapest materials, frequently use products just above minimum insulation requirements. Understanding the insulation class, including ground wall insulation, phase insulation and varnish/resin, is crucial in comprehending the differences between manufacturing and rewinding. In most cases, rewind shops will remove all insulation and wire and reuse the frame and stator laminations of the motor. They essentially rebuild the motor with all new insulation, magnet wire, varnish/resin and lead wires.
The Unseen Challenge
In many industrial facilities, maintenance teams lack knowledge about the internal details of electric motors. Their primary focus is on efficiently repairing motors at a reasonable cost in a prompt manner. However, when the maintenance team is unaware of the materials used in rewinds, the resulting repair may fall short of OEM standards, drastically reducing motor life and risking premature failure.
Choosing Wisely: Materials Matter
When comparing rewinds, it is imperative to assess the materials used by each repair shop. Touring repair shops to understand their capabilities and materials is essential. For example, ground wall insulation in small motors may vary from Dacron Mylar Dacron (DMD) with a class F rating to Nomex Mylar Nomex (NMN) with a class H rating. Some repair shops may even use discrete Nomex for a class N insulation rating, offering enhanced protection and potentially a longer life for a motor, as excessive heat reduces the longevity of a motor.
Beyond Insulation: Consider All Components
The type of materials used extends beyond insulation to include magnet wire, phase insulation, varnish/resin, bearings, lead wire, terminal connectors and the quality of machine work involved in the repair. Each component contributes to the overall effectiveness and longevity of the electric motor.
Not All Repairs Are Equal
Not all repairs are the same. Even two identical motors sent to different repair shops can result in entirely different outcomes. The critical question is whether users know what repair materials are being used in their essential equipment. Price is important but quality products used in repairs are equally important. It is encouraged for industrial facilities’ maintenance teams to involve an insulation specialist in reviewing and influencing the materials used in their rewinds.