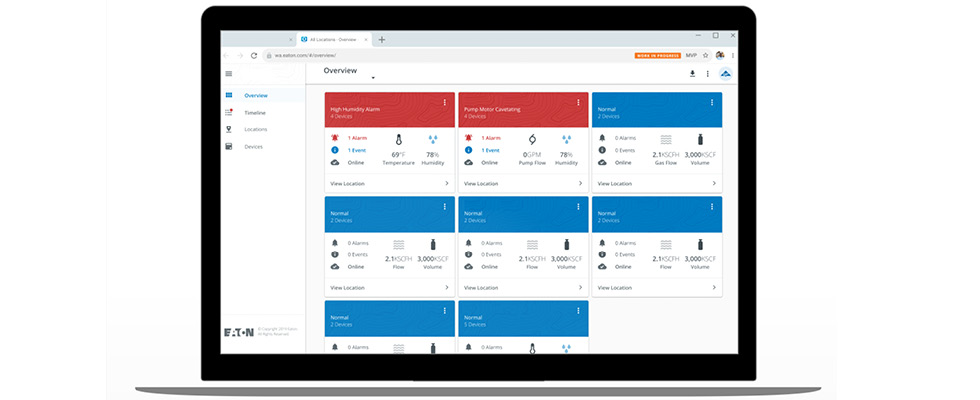
Tracking equipment health manually lacks the immediacy required to grasp the current condition of vital assets, identify potential issues leading to downtime or comprehend failures if they occur. Embracing remote monitoring for electrical power equipment and operational assets in water treatment facilities opens avenues for safeguarding personnel, productivity and equipment. When seamlessly integrated into critical assets, remote monitoring furnishes round-the-clock insights into equipment health
status, promptly notifying plant personnel of any abnormalities.
Furthermore, these solutions leverage collected data to monitor trends in equipment condition, which is crucial for predicting potential availability and reliability impacts. Specific event alerts and alarms ensure the safe deployment of personnel equipped with the necessary tools and parts for addressing particular issues or failures. The notifications empower operations and maintenance teams to swiftly respond to evolving conditions that could precipitate downtime or equipment damage. Additionally, trend data aids in proactive maintenance planning, enhancing reliability and prolonging equipment life span.
Motor & Control Monitoring
Approximately 70% of electricity used by industry is used to drive electric motors. Motors often power the most critical loads in water utilities, such as operating pumps in pipelines and water treatment facilities. Understanding the health of motors and the electrical systems that power them is vital to reliability and productivity in continuous process industries as well as water treatment facilities.
With motors and electrical rooms spread across dozens of remote pumping stations spanning thousands of square acres and potentially harsh environments, manual monitoring is time- and cost-prohibitive. This leaves operations teams blind to line, load and motor conditions, as well as current device status, which could risk unplanned downtime. To avoid these risks, it is best to have continuous, current readings on a system, from the quality of the incoming power source feeding the motor to individual pump or load conditions.
A cloud-based remote monitoring system provides current readings on any aspect of an operation, from vibration or excessive heat in the motor to key metrics in the electrical system including device status, temperature inside the enclosures, status of fans and blowers, breaker condition, current and voltage, overload protection and voltage anomalies.
This data can reveal issues that might otherwise go unnoticed, such as phase loss and harmonics, triggering notifications to relevant personnel. This allows maintenance teams to proactively correct issues that could otherwise lead to equipment damage, downtime or power factor charges from the utility. Planned repairs ensure maintenance personnel will not need a hot work permit and can work as safely as possible.
Continuous Thermal Monitoring of Electrical Equipment
There are hundreds to thousands of electrical connections in every electrical room, and each one is important to electrical reliability and equipment health. Manual thermography audits are labor- and time-intensive and involve deploying staff or contractors across the site, including remote or hazardous areas. Despite these costs and risks, manual audits only provide a snapshot of connection health, which is not sufficient to support trends analysis or preventive maintenance.
Solutions included within switchgear and other assemblies provide alarms and relays for predetermined setpoints to the control room but cannot communicate those anomalies directly to relevant maintenance personnel.
Some recent sensor technology solutions now capture continuous readings from equipment but deliver a huge volume of raw data without context or analysis. As a result, the work of identifying a bad connection or spotting a trend falls to the plant staff. This diminishes the usefulness of the data to prevent anomalies from becoming downtime events.
A remote monitoring solution augments internal continuous thermal monitoring within electrical assemblies by capturing sensor data from within each bucket for trend analysis. In addition, the application sends notifications directly to the necessary site personnel if readings are outside the normal expected range.
Substation & Asset Utilization Monitoring
Substations are intersection points in a power system where multiple facility loads are served from upstream power sources through several feeder units. A downtime event from these areas is likely to cause outages in wide areas of the facility, often for lengthy periods. Sites with multiple electrical rooms housing substations across a large facility face a common challenge: due to time and cost constraints, these substations are rarely visited.
Equipment may operate for 20 to 30 years in remote substations with a maintenance cadence of every five to 10 years, so the current health of electrical room equipment such as distribution switchgear and transformers is unknown. This “set it and forget it” approach means every failure is unexpected and has the potential to cause unplanned downtime that disrupts water collection and treatment processes, laboratory safety testing and clean water delivery.
Remotely monitoring electrical equipment gives plant personnel current readings from sensors, monitors and other digital devices placed in electrical equipment to monitor specific components, states and conditions, including environmental conditions. The system transmits data to a cloud-based solution so personnel who have access to the application can see current data trends on all monitored aspects of substations and their associated rooms. This allows them to receive alarms based on predetermined thresholds and events.
Facility Power Management & Asset Utilization
Power failures are particularly problematic for utilities that must provide clean drinking water to users and are subject to environmental regulation. Data on power usage and equipment performance is essential for the operation of production lines, as well as for capacity planning. What processes or equipment consume the most power in the facility? How is capacity currently allocated and how does that impact operational equipment usage or changes? Why are two similar assets consuming power at substantially different rates? Are issues like harmonics driving up power factor penalties?
Because manual monitoring is expensive and time-consuming, many facilities have little to no information on these important questions. Being blind to power usage, capacity and equipment health trends leads to a reactive approach to maintenance that causes increased operating costs, unplanned outages and lost productivity.
Remote monitoring of assets provides ongoing insights into critical aspects of facility power management and asset utilization. By capturing power usage from each piece of equipment, the system provides essential information on equipment health as well as opportunities to decrease power usage and utility costs by resolving issues like harmonics. Monitoring also makes clear the balance of capacity to usage, which is essential information for facility planners.
Benefits of Remote Monitoring
Worker safety
- Reduced staff interaction with electrical equipment to take readings
- Ability to capture a continuous flow of data from equipment in remote and hazardous environments
- Sensor data identifies location, equipment monitored and condition or state so maintenance can deploy with appropriate tools, parts and personal protective equipment (PPE)
Equipment health and longevity
- Continuous metrics give an updated understanding of the current state of any monitored asset
- Escalating alarms and notifications ensure prompt response when a sensor reading falls outside of predetermined thresholds and events
Productivity and profitability
- Reduction in frequency and duration of downtime events
- Data is immediately available to relevant personnel so they can act without delay
- Reliable current and historical data informs preventative maintenance scheduling
- Greater efficiency in response by eliminating troubleshooting in the field
Cloud-based application
- Role-based alarms, notifications and access to equipment data
- Alarms are sent instantaneously to correct personnel via SMS and email for timely action
- Equipment health data is available 24/7 on any device
- Captured data is reflected in dashboards and trend lines for actionable insights
- Equipment data is available for reporting and for use in other software systems
- Greater accuracy of sensor data improves quality of monitoring
Planning and reporting
- Insights into facility power management, asset utilization and capacity to usage to support
facility planning - Consistent data to support compliance reporting and the organization’s environmental, social and governance (ESG) goals