Whether a pump is new, used and recently modified, or freshly refurbished with a critical service mission, end users routinely specify hydraulic performance acceptance tests to guarantee pump performance. Performance testing can be complex and should account for a multitude of variables. Test loop designs can vary both in system design and instrumentation selection. Image 1 shows an example of an open pit, vertical test loop used to test large, high-capacity vertical pumps; however, test loop designs vary greatly across the industry. Pump applications can represent a wide range of tolerance requirements for flow, head, efficiency, brake horsepower (BHP) and net positive suction head required (NPSHR). For these reasons, the pump industry adopted testing standards that are used to detail the methodology for testing centrifugal pumps and define whether a pump has met the performance specifications.
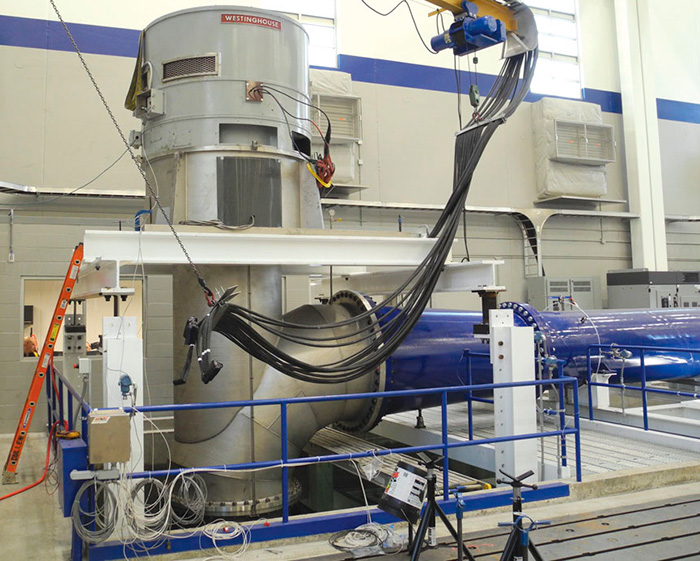
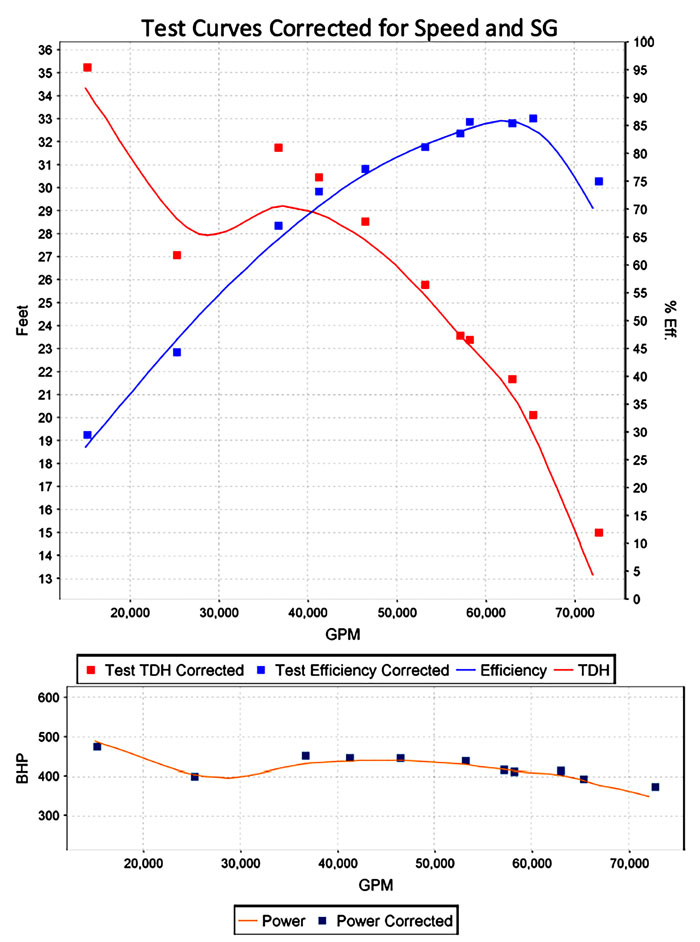
Before the Test
❑ Verify that any necessary elevation corrections will be made to the head readings. Unless the pressure gauges are located precisely at the suction and discharge centerlines, a head correction must be made to account for the difference between the pump centerline elevation and the measurement elevation.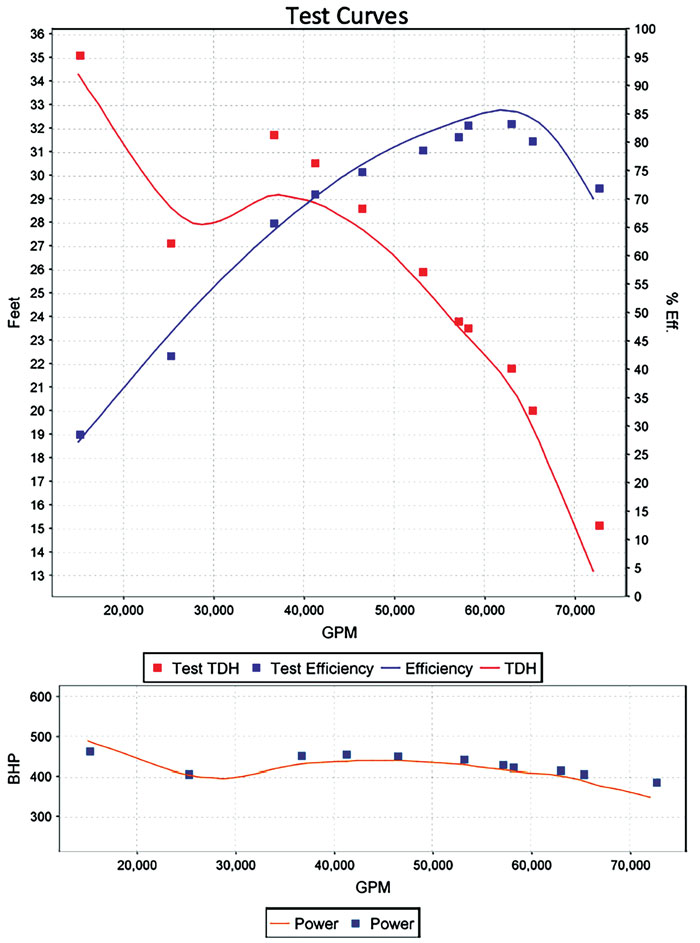
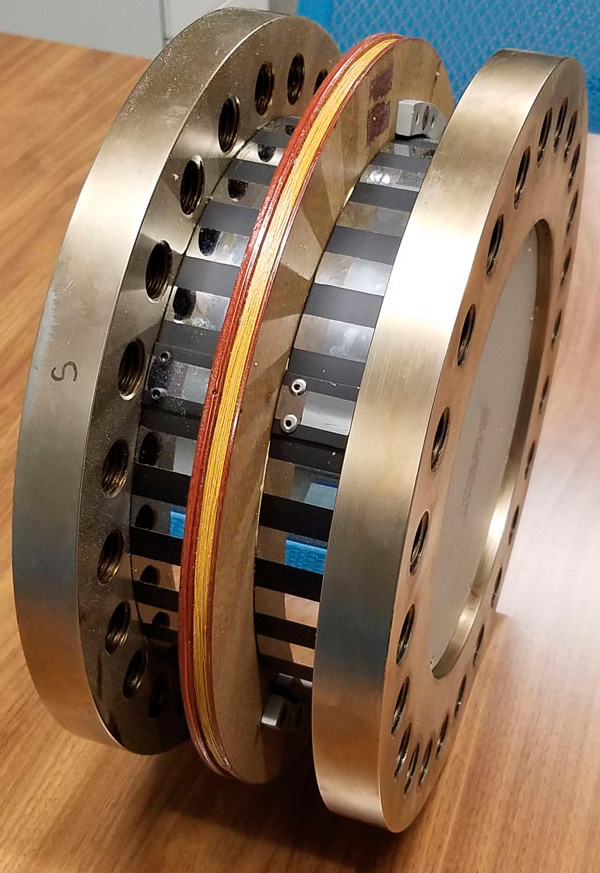
During the Test
❑ After start-up, make sure the gauge lines are vented or purged of all air. Air pockets or bubbles can cause significant measurement inaccuracies.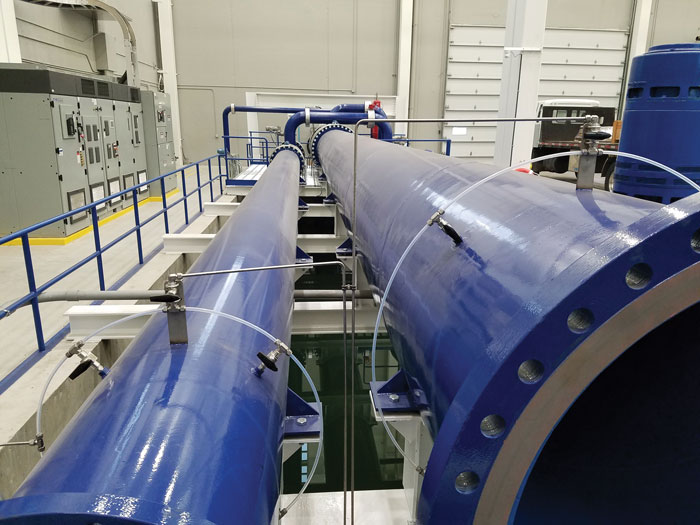