During the past few years, end users in the power generation industry have considered specifying pumps according to American Petroleum Institute (API) standards. The standards, according to the API website, “are designed to assist industry professionals improve the efficiency and cost-effectiveness of their operations, comply with legislative and regulatory requirements, safeguard health, and protect the environment.” Typically, the standards require a more robust equipment design. The API Standard 676 is a purchase specification used for rotary positive displacement pumps. Like all API standards, 676 was developed to establish a minimum standard for process pumps in mission-critical applications. In power generation, these applications include fuel injection, fuel transfer or booster services. The standard helps ensure the integrity of the pump’s envelope during an emergency, such as a fire. The most recent version of API Standard 676 (Third Edition, November 2009) specifically states that “... in auxiliary services (for example, lube oil systems), manufacturer’s standard with demonstrated experience is acceptable.” In most cases, API 676 is applied only when handling fuel. The standard must be relevant to service needs. Alone, it cannot be applied to the overall operation. The purchaser must specify certain details and required features. More than 70 bulleted paragraphs require either a decision by or more information from the purchaser. A completed data sheet should also be supplied to the vendor. The purchaser should complete the following sections: operating conditions; detailed fluid data; site and utility data; API Standard 682 data sheets for mechanical seals; driver detail; quality assurance inspection; piping and appurtenance details; instrumentation requirements; preparation and paint; and baseplate detail.
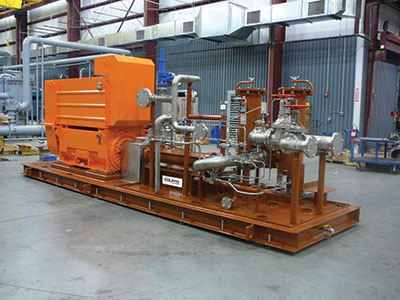