Gaskets have always been part of industrial production. However, gaskets have not always been forgiving, easy to use or simple to remove. What if the sealing products were designed to optimize the work put into them? What if the design had a level of intelligence built in? What if the design could make up for equipment damage? When used properly, enhanced surface profiles for gaskets can reduce leaks, spills and other releases that can damage the environment, put people at risk, result in fines and lead to costly downtime. Using surface profiling to reduce area and increase stress is found in everyday life, from the soles of running shoes to the treads on vehicle tires. Reducing the contact area while maintaining compressive force results in increased stress. In the case of gaskets, traction or friction between a gasket and the flange faces is critical to holding internal pressure. If the downward force created by the fasteners in a flange is diluted or spread over a larger area, the overall stress is reduced.
Compressibility
Adding raised features to the surface of a gasket to reduce contact area and increase stress also tends to impact compressibility. Compressibility represents the ability of the gasket to conform to the surfaces it is being used to seal. Flange surfaces usually show signs of wear, pitting, scratches or other defects. It is cost-prohibitive to make two mating flange faces smooth and flat enough to seal without a gasket. The more compressible a gasket is, the better chance the user has of attaining an effective seal.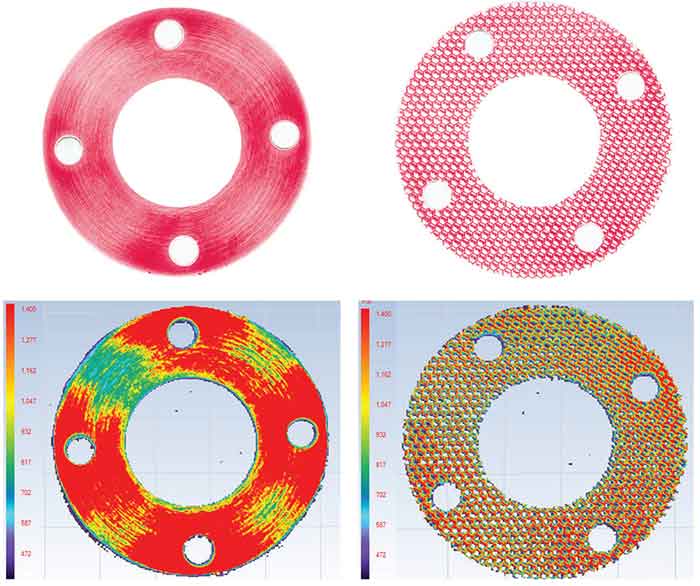