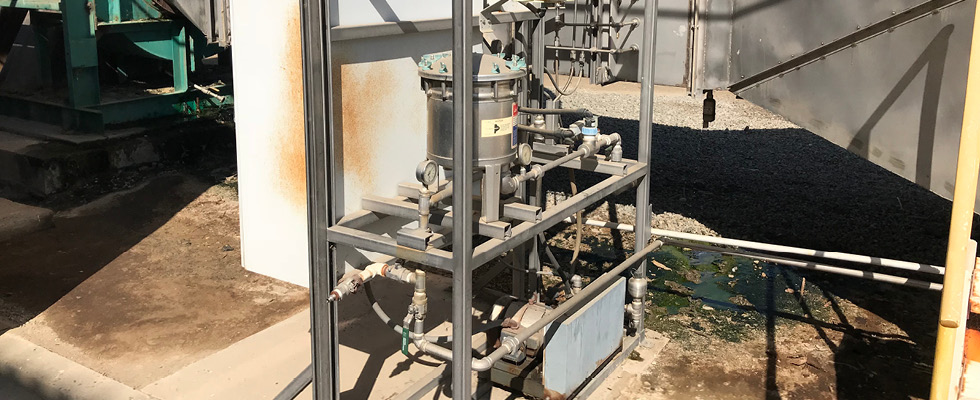
Evaporative cooling of the inlet air flow to gas turbines has been used successfully for several decades to boost output, especially in the warm summer months. However, this technique has not been widely used to cool the inlet air flow to air compressors.
In a hot and dry climate, evaporatively cooling the inlet air flow can increase the mass flow through a compressor by 6% or more. In a humid environment such as the United States Gulf Coast, the air mass flow can be increased by 3%. Cooling the air also reduces the power consumed by the compressor.
Hearing about its potential benefits, J.R. Simplot Company decided to implement fogging in one of its fertilizer plants as part of ongoing efforts to improve energy efficiency and improve output.
Reducing Energy Intensity
A food and agriculture company headquartered in Boise, Idaho, that focuses on food processing and food brands, phosphate mining, fertilizer manufacturing, farming, ranching and cattle production, as well as other enterprises related to agriculture was looking to reduce the energy intensity of its products by 25%.
One of the company’s major U.S. production facilities is in the heart of California’s San Joaquin Valley. The plant produces nitric acid and various downstream nitrate and phosphate liquid fertilizers. According to the engineer and production manager, roughly 55% of its energy consumption is from butane, 35% is from the grid, 7% is from natural gas and the remaining 3% is from gasoline and diesel. Its nitric acid plant consumes about 80% of the total electric load (about 600 kilowatts [kW]) and is the most critical part of overall operations, along with a nearby ammonium nitrate plant. Both are run continuously except during scheduled shutdowns. In addition, a calcium ammonium nitrate (CAN-17) plant operates intermittently on the premises.
To achieve the 25% reduction goal, it attacked energy inefficiency on multiple fronts. It carried out various upgrades, installed variable frequency drives (VFDs), upgraded pumps and controls, updated its air compressor and added fogging to the air compressor’s inlet air to boost output. Efforts like these earned the fertilizer plant Energy Star certification from the U.S. Environmental Protection Agency (EPA).
The EPA recognized the plant as among the most energy-efficient nitrogenous fertilizer manufacturing facilities in the country. This measure is a statistical model that scores a facility’s production and energy use to benchmark its energy performance against the industry.
Air Compressor Fogging Boosts Efficiency
Inlet air fogging of the air compressor represents one facet of the plant’s drive to achieve a greater level of energy efficiency for the facility as a whole. Fogging consists of spraying tiny water droplets into the inlet air flow to cool the air by evaporation. This increases gas turbine power due to the fact that cooler air is denser. Therefore, the mass flow of the working fluid increases and the compressor becomes more efficient at lower air temperatures.
Modern fog systems allow a plant operator to control compressor output by adding or removing fog nozzle stages. It has been shown to produce good results in dry as well as humid climates.
How does it work? When a fog droplet is evaporating, the hot air molecules surrounding the fog droplet supply the heat of vaporization. Thus, the air is cooled as the droplet evaporates. Mass is transferred but energy is conserved, which means there is no change in the enthalpy—or total heat—of the air/vapor mixture. The heat used to vaporize the water droplet is latent in the air/vapor mixture while the sensible heat of the air is reduced. The output increase for a typical industrial gas turbine with 8 C of cooling is about 6%.
In a desert environment, power boosts of more than 20% have been recorded during the hottest parts of the year. At the plant, the engineer and production manager estimated the gains from using the fogging system on the air compressor vary from 5% to 10% depending on conditions.
What drove the adoption of this technology at the facility? The drivers were both energy efficiency and the demand for more fertilized production on warm days. The facility had a strong need for higher nitric acid production during the long California summer. The fogging system is used to cool down the inlet air of the process air compressor in the nitric acid plant.
The multistage process air compressor at the plant is driven by a steam turbine on one side and a hot gas expander on the other end. The steam turbine utilizes 550 pounds per square inch gauge (psig) process steam and the expander is fed by hot tail gas. Pressurized process air is supplied to the reactor to react with ammonia in the nitric acid production process. The more air mass delivered, the more ammonia is produced and the higher the nitric acid production will be. The compressor performance (factoring the mass flow of the air delivered at the discharge pressure) varies following the ambient temperature.
During summer months in the valley, the dry air temperature can rise up to 115 F at times, leading to lower daily production, yet product demand is high in those periods. Using the fogging system when the ambient temperature is above 78 F allows the inlet air to be cooled down significantly. This results in higher air mass delivered to the process and thus, higher production during summer months due to increased air flow and lower energy intensity.
Operational Matters
The fogging system has been easy to operate. When ambient humidity soars, the air temperature does not drop as much as during dry conditions. However, the system remains in use as it still brings about an improvement by cooling the air down despite the higher humidity.
As for maintenance, the engineer and production manager reports there is relatively little needed on the fogging system. The main maintenance actions needed include winterization each year, as temperatures in the San Joaquin Valley plummet in the winter, and they drain the system during the winter months to protect it from freezing and also to preserve filter life.