
Flow meters play a pivotal role in water management by offering precise and real-time measurements of water flow. This enables operators to assess and optimize system performance. This article explores the operation of flow meters and the different types available while providing guidance on selecting the most appropriate flow meter for specific water management needs.
What Is a Flow Meter?
A flow meter is an instrument designed to quantify the volume or mass of a fluid passing through a pipeline over a specific time frame. By tracking flow rates, flow meters offer vital information on the movement within pipelines, drainage systems and other infrastructure. This information assists operators in verifying system equilibrium, ensuring adequate supply at each endpoint, identifying excessive flow rates that could harm pipelines and more.
Specifically, a water flow meter is tailored to measure the flow of water, distinguishing it from devices meant for other liquids (such as oil or gasoline) or gases. Water flow meters are used to:
- Monitor consumption by individual homes or communities within municipal water supply systems
- Track sewage flow to aid municipalities in ensuring their wastewater management systems can accommodate demand
- Assist operators in factories to gauge the volume of water utilized for cooling purposes in an industrial setting
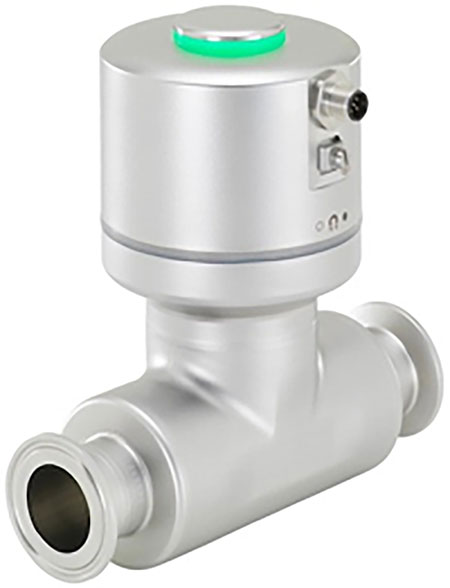
of Tameson)
Types of Water Flow Meters
All flow meters have a fundamental task—to measure flow by monitoring the amount of liquid or gas that moves through a conduit within a specified period. Despite this common objective, there are several distinct types of flow meters, each employing a different technique to measure flow.
Surface acoustic wave (SAW) flow meters
SAW flow meters (Image 1) are nonintrusive devices designed to measure the flow rate of fluids. These devices operate on the principle of generating surface acoustic waves along a piezoelectric material substrate. As the fluid moves across the sensor’s path, it affects the velocity and amplitude of these waves. The flow meter analyzes these changes in wave propagation, which are directly influenced by the fluid’s velocity, to determine the flow rate. These meters are favored for their nonintrusive nature, high precision and minimal maintenance needs.
SAW flow meters are commonly used in municipal water supply systems to monitor water distribution and ensure a consistent supply. They are also employed in industrial cooling systems to measure flow rates in cooling water circuits and in environmental monitoring to track water flow in natural water bodies for research and conservation purposes.
Electromagnetic flow meters
Electromagnetic flow meters, also known as magnetic meters or mag meters, utilize electrodes to measure the flow of water. These electrodes are placed on opposite sides of the conduit through which the liquid flows, creating a magnetic field. The flow rate is determined by detecting the voltage generated as water moves through this magnetic field, enabling electromagnetic flow meters to accurately track flow rates.
Electromagnetic flow meters are typically low maintenance because they lack mechanical parts that could fail. Additionally, since there are no obstructions in the water’s path, electromagnetic meters do not impede the flow of water. This means the measurement process does not negatively impact the flow rate. Electromagnetic flow meters find their applications in wastewater management, where they handle dirty, sludgy and corrosive fluids without clogging. They are essential in the distribution of potable water, ensuring accurate measurements, and are also used in chemical processing plants to measure flow rates of conductive liquids.
Differential pressure flow meters
Differential pressure flow meters work by directing water through a narrowed section, such as an orifice plate or a nozzle, and then measuring the pressure before and after this constriction. A significant difference in pressure indicates a high rate of water flow.
The main drawback of this flow meter type is its tendency to decrease pressure and potentially reduce the speed of water flow, leading to a permanent loss of pressure. This characteristic makes differential pressure flow meters less suitable for applications where maintaining maximum pressure throughout the system is critical.
Differential pressure flow meters are typically used in boiler feed water systems to monitor flow rates in high-pressure environments. They are also utilized in heating, ventilation and air conditioning (HVAC) systems to measure flow and in the oil and gas industry to track flow rates in pipelines where a pressure drop is acceptable.
Mechanical (turbine) or propeller flow meters
Mechanical flow meters operate by channeling liquid through a component that moves in response to the water’s force. The most prevalent form of mechanical flow meter incorporates a propeller for this task. The speed at which the propeller or another mechanical element rotates allows the flow meter to accurately gauge flow rates.
This category of flow meters relies on mechanical components, which may experience wear and tear over time, necessitating a higher level of maintenance. To maintain accuracy, it is essential for operators to regularly replace bearings and ensure the propeller is correctly aligned.
Mechanical flow meters are suitable for cooling systems in factories and data centers, ensuring the correct volume of cooling water. They are also used in water treatment plants to measure flow rates in various stages of water treatment and in irrigation systems to monitor water distribution in agricultural fields.
Ultrasonic flow meters
Ultrasonic flow meters determine the velocity of a liquid using ultrasonic waves. By emitting these waves into the liquid and analyzing the returning signal, these meters can quickly calculate flow rates.
One of the advantages of ultrasonic meters is their minimal mechanical parts, making them a low-maintenance option for measuring flow. However, the accuracy of ultrasonic meters can be affected by the presence of contaminants like dirt or air bubbles in the liquid, as these can alter the speed at which sound waves travel through different materials. Ultrasonic flow meters are ideal for agricultural irrigation, measuring flow in large pipes with minimal maintenance. They are also used in building management systems to monitor water usage in commercial buildings and in leak detection to identify leaks in water distribution networks.
Vortex flow meters
Vortex flow meters utilize the von Kármán effect to measure water flow. They work by detecting the differential pressure generated by an obstacle placed in the liquid’s path. This obstruction causes a swirling effect or vortex, which is then used to determine the flow rate.
Although vortex flow meters lack mechanical parts, which translates to lower maintenance requirements, they may not provide highly accurate readings, particularly at lower flow rates. Vortex flow meters are commonly used in steam applications, measuring steam flow in power plants and industrial processes. They are also employed in water treatment to monitor flow rates in treatment processes and in the chemical industry to measure the flow of liquids and gases in chemical processing.
Coriolis flow meters
Coriolis flow meters are highly valued in water management for their ability to directly measure both the mass flow rate and the density of flowing water, offering a comprehensive view of water movement and characteristics in various applications. Coriolis meters operate on the principle of the Coriolis effect, where fluid passing through a vibrating tube causes the tube to twist in proportion to the mass flow rate, a phenomenon accurately detected by sensors. This makes them ideal for applications where water’s mass or density is a critical parameter, such as in mixing or dosing processes, and for ensuring the precise management of resources in treatment facilities.
Coriolis flow meters offer the advantage of measuring mass flow and density directly, providing high accuracy across a wide range of flow conditions, but they can be expensive and complex to install, especially in large pipe sizes. Coriolis flow meters are highly valued in mixing and dosing processes, ensuring precise measurement of mass flow and density. They are used in pharmaceutical manufacturing for the accurate measurement of ingredients in drug production and in the food and beverage industry to monitor flow rates in production lines.
Positive displacement flow meters
Positive displacement flow meters are crucial in water management for their ability to accurately measure the volumetric flow rate of water by mechanically trapping and counting discrete volumes of fluid.
These meters excel in applications requiring precise volumetric measurements, such as water billing and distribution, due to their exceptional accuracy across a wide range of flow rates, including very low flows. Positive displacement flow meters excel in measuring low flow rates with high accuracy and are simpler and more cost-effective, yet they have moving parts that may require maintenance and are less suitable for measuring high flow rates or handling particulate-laden water.
Positive displacement flow meters are crucial for water billing and distribution, providing accurate measurements for billing purposes. They are used in residential water meters to monitor household water usage and in fuel measurement systems to measure flow rates of fuel in dispensing systems.
How to Select a Water Flow Meter
Choosing the most suitable water flow meter for specific needs involves navigating through various options, each offering different levels of accuracy and maintenance requirements. To make
an informed decision, consider the following factors:
- Understand the process: Begin by thoroughly understanding the process that requires flow measurement. This includes knowing the flow rates, pressure and temperature conditions the flow meter will encounter.
- Consider the media being measured: Identify the characteristics of the water (or other media) being measured. Factors such as viscosity, presence of particulates and whether the water is clean or wastewater can significantly influence meter selection.
- Determine accuracy, range and certification requirements: Assess the required accuracy level for the application. Also, consider the flow rate range over which the meter must accurately measure. Some applications may also require flow meters to have specific certifications or to meet industry standards.
- Inspect the meter location and installation needs: Evaluate the physical space where the flow meter will be installed for any constraints. Consider the environment around the meter, such as the presence of vibrations or electromagnetic interference, which could affect meter performance.
- Decide what type of output is needed: Determine the type of output needed from the flow meter, such as analog, digital or a pulse signal. This will depend on how the flow data will be used, whether for monitoring, process control or integration into a larger management system.