Water and wastewater treatment is not a glamorous or popular topic. However, it is a critical part of our everyday lives that is often taken for granted. For example, the last thing on anyone’s mind during a major sporting event, such as the Super Bowl, is water and wastewater. During halftime, though, thousands of treatment facilities handle the demand when millions of people use their facilities at the same time. Municipal treatment facilities are sophisticated operations that use chemical and biological processes to contain and convert dangerous waste into an environmentally safe and often reusable material. Since most of these facilities are operated and funded by a municipal governing body, cost control, efficiency and reliability are top priorities. The review of common applications, rotating equipment and sealing options found in a typical treatment facility is important.
Rotating Equipment
Like most process facilities, wastewater treatment plants have a variety of rotating equipment to handle the volume and different fluids being processed. These include centrifugal pumps (vertical and horizontal), submersible pumps, progressive cavity pumps and large axial flow pumps. Sealing options that provide reliable and economical solutions to contain the fluids being pumped are available for each type. These include designs for the wide range of pump sizes used in treatment facilities.Sealing Options—Compression Packing or Mechanical Seal
The most common sealing option is compression packing. In addition to providing adequate leakage control, it is economical and provides additional bearing support to the shaft. However, it experiences wear and requires regular adjustments and a clean water flush. Further, it can wear the shaft sleeve that it seals upon.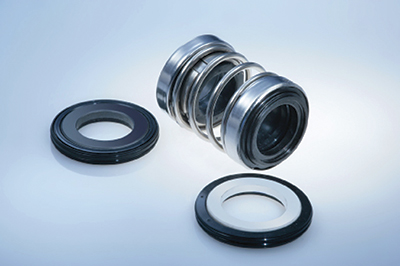
Feedwater—Handling Solids and Abrasives
Wastewater treatment facilities process solids-containing liquid from a wide range of sources. Typically, ambient temperatures prevail and large volumes of liquid and every kind of solid imaginable are processed. The amount of solids at any given time will be a guide to the optimum mechanical seal arrangement. However, the design will almost always include hard faces (silicon carbide) to handle the abrasives that are present. Since water is the base fluid, stainless steel is the most common and acceptable metallic component of the seal for most applications. However, some applications with excessively high or low pH or those in which other corrosives are present might require a higher base metallurgy. The abrasives are the most common and challenging part of wastewater applications.Seal Arrangement
The amount of solids present, typically defined as a weight percentage of the fluid being handled, will drive the decision to use a single or dual seal arrangement. The typical single seal with two hard faces can handle as much as 10 percent solids when installed in a big bore seal chamber without flushing or in conjunction with API Plan 02. In a pump that is equipped with a standard bore seal chamber, the typical single seal is limited to a few percent solids unless water is injected into the seal chamber per API Plan 32. A throat bushing in the bottom of the seal chamber should be used with API Plan 32 to minimize water consumption while providing a clean environment for the seal. Treated water is commonly used as a flush medium because it is readily available and does not require removal later. For solid concentrations above 10 percent, single seals typically can be used, but an external flush will be imperative. If an external water flush is not desirable or available, dual pressurized seals should be considered for high solid concentrations. The most common flush plan for dual seals is API Plan 54. API Plans 53 A and B are rarely used. Single mechanical seals are usually preferred over dual seals because of the lower initial cost and simplicity of operation and maintenance.Seal Design Considerations
A few specific aspects must be considered when sealing a pump in a wastewater treatment facility. First, routine, axial adjustments to the impeller are needed to maintain the pump’s efficiency when handling solids. When such an adjustment is made, the seal must be able to accommodate this axial movement. Depending on the type of mechanical seal—component or cartridge—additional steps/care may have to be taken. The second aspect involves cleaning the seal chamber before shutdown. The seal chamber can trap solids that could cause problems during the next startup if not removed adequately.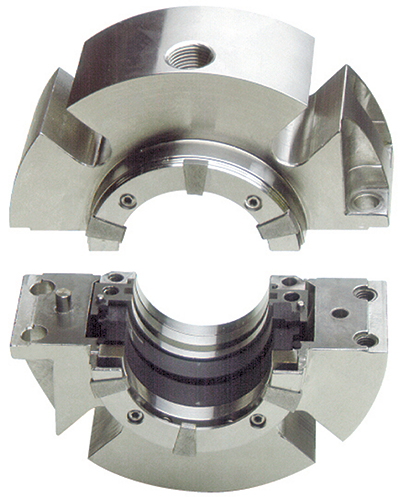
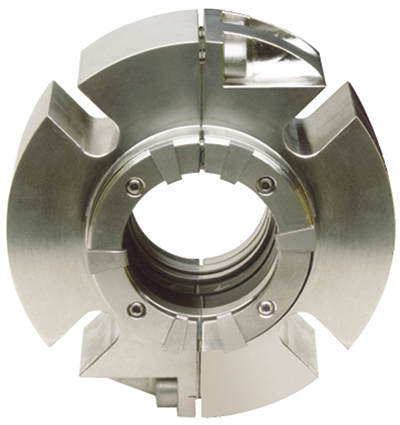