Single-Volute & Double-Volute Casings & Reverse Runaway Speed
01/22/2014
Q. What are some differences between single-volute and double-volute casings for rotodynamic centrifugal pumps? A. The discharge casing serves the following purposes:
- Collects output from the rotating impeller
- Decreases the velocity momentum of liquid leaving the impeller before it reaches the next stage impeller or pump discharge
- Transforms increased kinetic energy of liquid at the impeller outlet into pressure
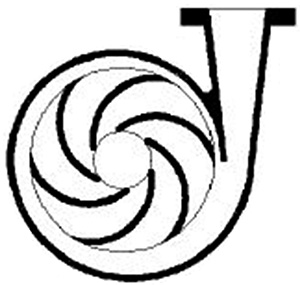
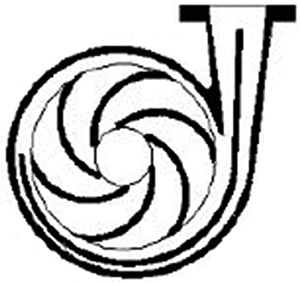
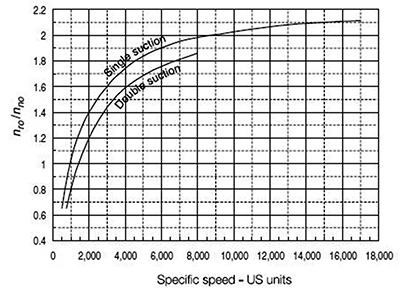
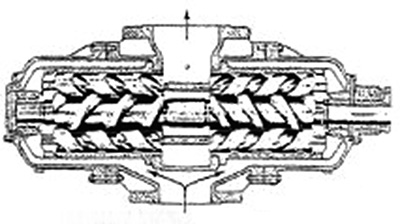
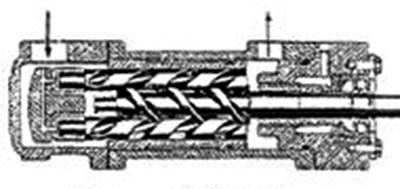