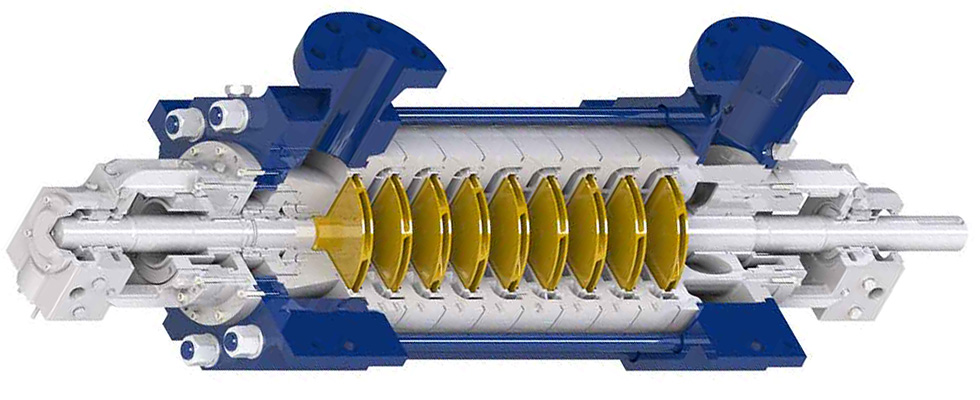
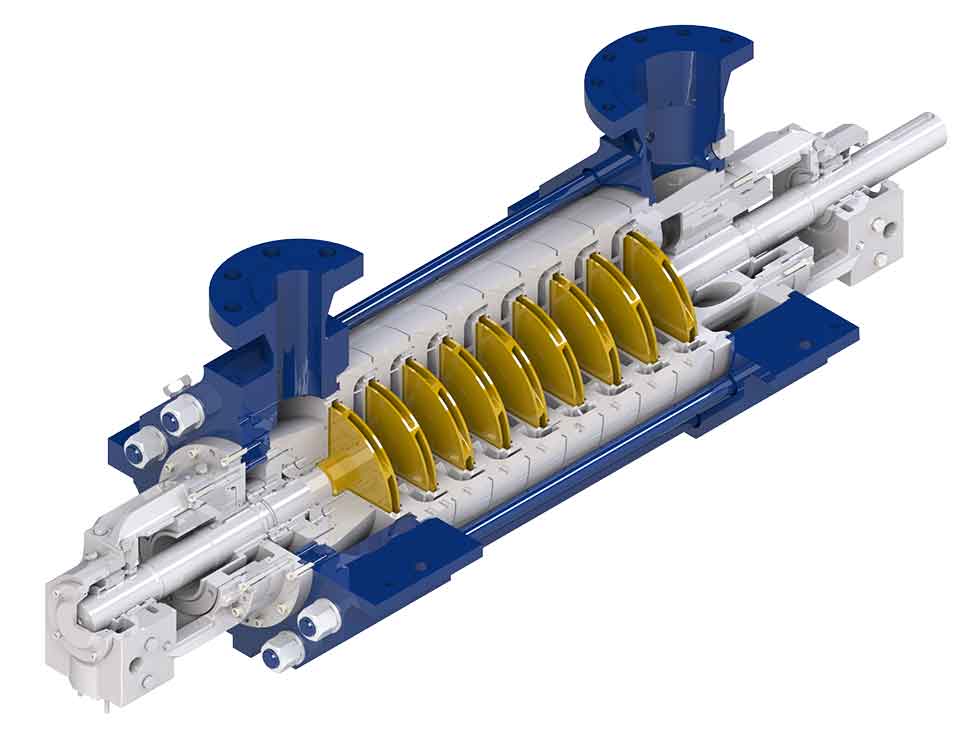
The pump shaft is the central component of the rotating element and is responsible for transmitting energy to the rotating components. The shaft carries the impellers, sleeves and couplings for the rotating element assembly. The stiffness of the combined assembly is responsible for ensuring that the pump stationary components do not come into contact with the rotating components.
Unfortunately, this is not always achieved and many pump rotors cannot be described as classically stiff. This can have dire consequences for machine reliability, particularly if, during the rotor build process, the technicians are not aware of the subtleties of the machine design.
Some machines deliberately have shafts that are flexible and these machines rely on the Lomakin stiffening effect that occurs due to the differential pressure across wear rings and bushes.
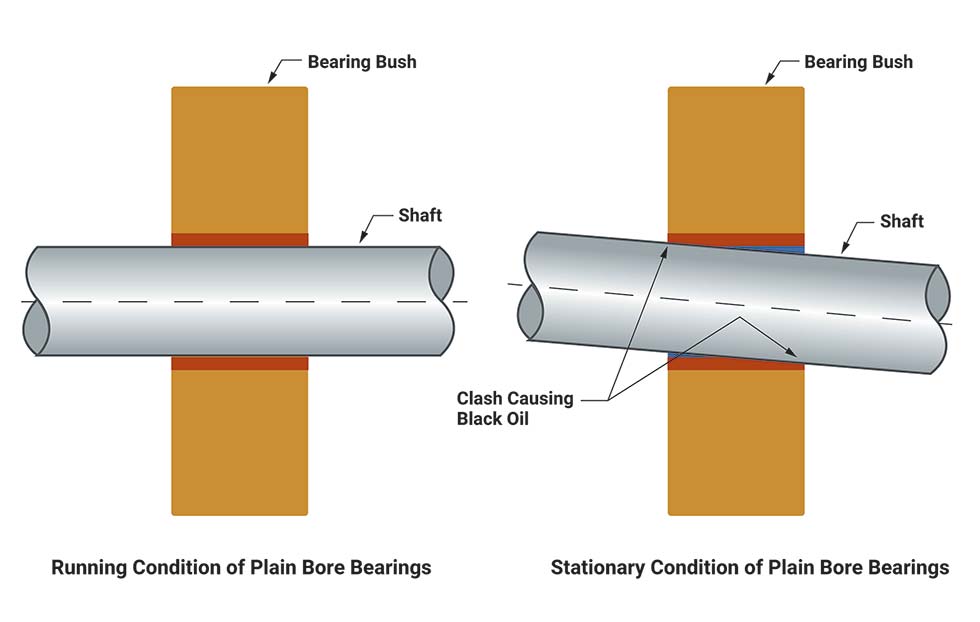
This force centralizes the rotor within the machine’s running clearance. This allows machine costs to be kept low as the shaft can be lighter and the running position of the element is supported by the machine in operation. This is particularly true of BB4-style machines.
One drawback to this design is the tendency for this type of machine’s stationary and rotating components to touch on startup and rundown.
This situation has even been known to contribute to “black oil” caused by journal bearing contact.

Pump manufacturers employ complex geometries including pre-worn bearings and offset bores to ensure this type of contact does not occur. The problems come over time when the subtleties of the design adaptions are forgotten or neglected, even by the companies that originally introduced them.
Shaft stiffness can also cause reliability issues when upgrading a machine to more modern sealing technologies.
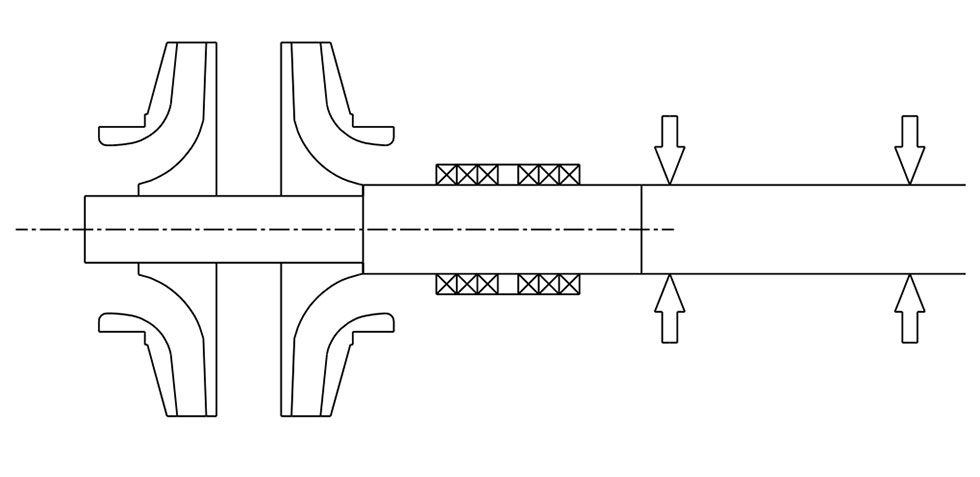
Many machines were originally designed with shaft systems suitable for soft packing. This packing has great supportive properties to shaft stiffness. These properties were used at the time of the machine design to allow the pump manufacturers to employ a small shaft diameter. The shafts are now commonly called “wet noodle” shafts.
When the soft packing is replaced by a mechanical seal, which has little supporting properties, the shaft support system can be compromised.
This can lead to poor bearing and seal life, and high vibration. Also, the wear parts are prone to contact.
The situation also exists with overhung pumps. While codes and specifications have had some success in eliminating this type of machine, many examples of this type of equipment still exist.
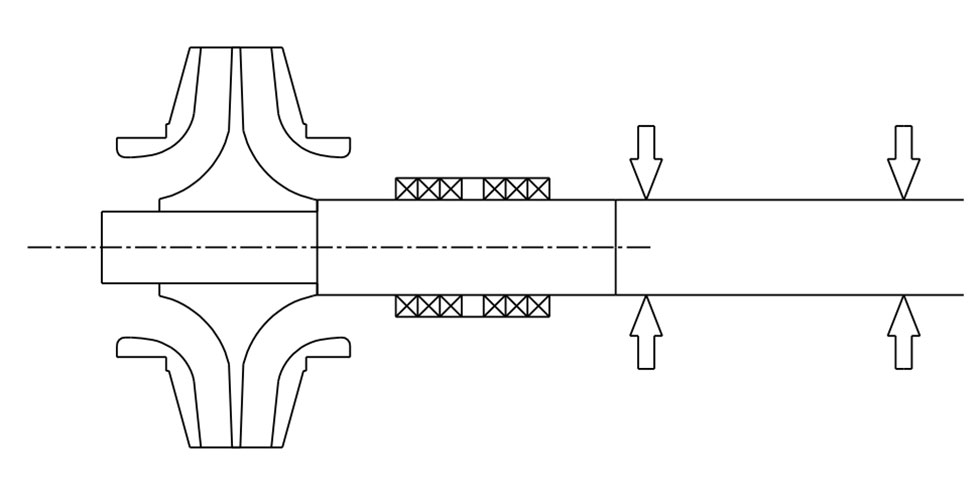
Environmental requirements that drive the upgrade of this type of machine from soft packing to mechanical seal also have the unintended consequence of driving reliability downwards.
Soft packing provides a great deal of shaft support, mechanical seals can provide little. Make sure the shaft system is considered before any seal upgrade.
Understanding the nature of the shaft system is important for any pump rebuild and any pump upgrade. Reliability headaches can be avoided if this is considered before any machine change.