Laser alignment systems and other tools
04/11/2019
Is there a simple way to check the alignment of flexible couplings on a pump? Laser alignment systems are used to determine the extent of shaft misalignment by measuring the movement of a laser beam across the surface of a detector plate as the shafts are rotated. Many laser alignment systems are available, and the procedure for alignment is provided by the laser system’s producer. They are capable of aligning couplings with and without spacers and are most commonly used for precision alignments. Image 1 shows an example of a laser alignment system setup on a pump and motor shaft. By following the instructions of the laser system, the computer will output adjustment requirements to align the shafts.
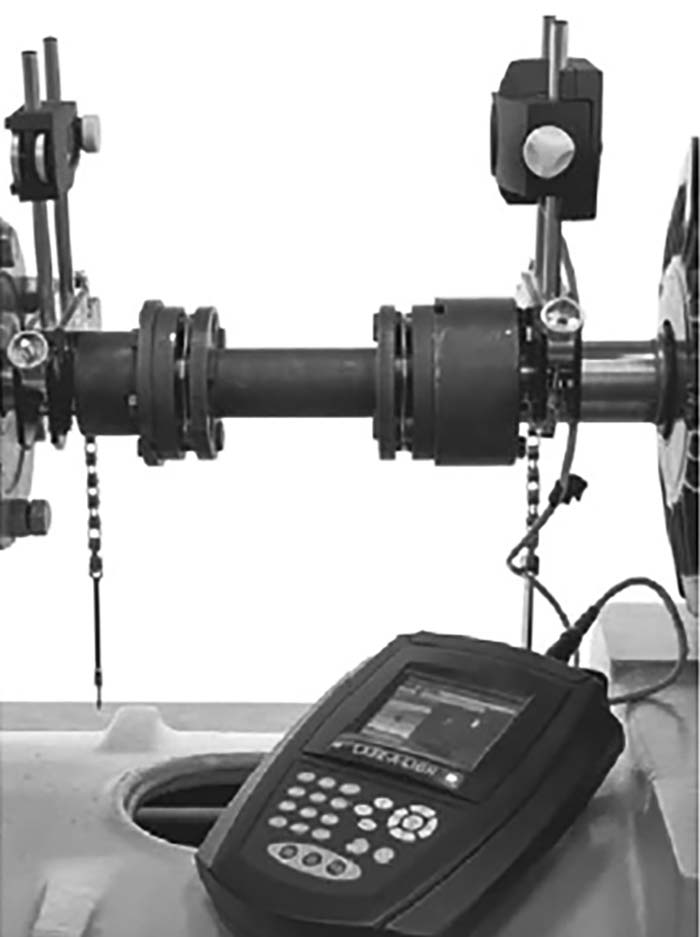
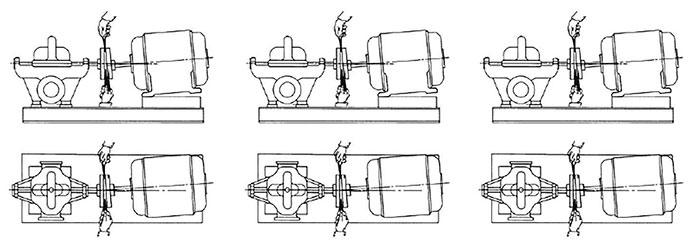