The benefits of dry screw, liquid ring and rotary vane vacuum pumps.
Busch Vacuum Pumps and Systems
08/01/2018
Editor’s Note: As we celebrate Pumps & Systems’ 25th anniversary this year, we have published articles from 1993 and asked experts from the same companies as the original author(s) to give our readers an idea how that technology has changed since that time. For this month, here is an excerpt from the August 1993 article, followed by an update on choosing vacuum technology for chemical and pharmaceutical processes.
Vacuum Sources
Many factors help determine the best type for your application By Henry H. Hesser In the recent past, a process engineer had few things to consider when choosing a vacuum source for a process requiring less than atmospheric pressure. Cost, reliability, vacuum level and experience in similar processes were about all that mattered. These considerations have not disappeared, but like everything else in life, many more complications have arisen. A list of concerns today might include:- effluent considerations (Clean Air Act and Clean Water Act)
- potential for recycling or recovery of solvents and materials removed with the vacuum stream
- energy requirements and methods of reduction
- expandability and flexibility of adding or subtracting capacity
- accuracy of vacuum control
- steam or air ejectors
- roots-type rotary lobe boosters
- rotary vane vacuum pumps
- screw-type vacuum pumps
- claw-type vacuum pumps
- liquid-ring vacuum pumps
- rotary piston pumps
Here is the original article published in August 1993.
Selecting the right vacuum technology for chemical and pharmaceutical processing applications is often difficult. First, a vacuum system must deliver the required pumping speed at operating pressure and ensure the required pump downtime. Second, it cannot be sensitive to process gases and must meet all requirements when it comes to CIP (clean-in-place) cleaning and gas recovery. Reliability and economic efficiency also play a significant role when deciding which vacuum technology to use.
Dry Screw Vacuum Pumps
Dry screw vacuum technology is widely used in the chemical and pharmaceutical industries. The first dry screw vacuum pump for use in the chemical and pharmaceutical markets was launched in the 1990s. These pumps have an advantage since they do not require operating fluid to compress the process gas. In a screw vacuum pump, two screw-shaped rotors rotate in opposite directions. The pumped medium is trapped between the cylinder and screw chambers, compressed and transported to the gas outlet. During the compression process the screw rotors do not contact each other or the cylinder. Precise manufacturing and minimal clearance between the moving parts enable this operating principle and, in addition, guarantees a low ultimate pressure of less than 0.1 Torr. Modern screw vacuum pumps have a variable pitch screw, which results in even compression of the process gas across the entire length of the screw. This has the advantage of ensuring the same temperature throughout the entire compression chamber, which can easily be monitored and controlled. Screw vacuum pumps use a cooling jacket, ensuring even temperature distribution and greater thermal efficiency and stability throughout the pump body.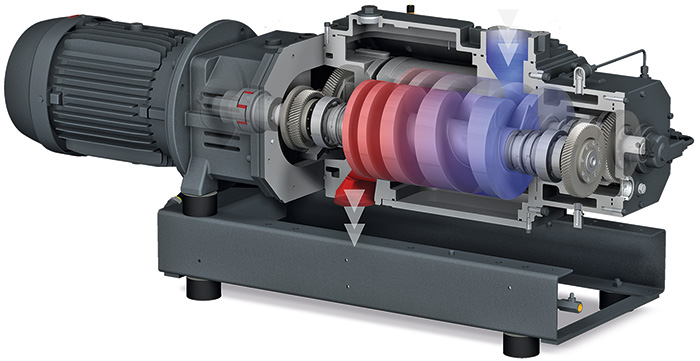
- dry compression, no contamination or reaction possible between process gas and operating fluid
- high vacuum level
- energy efficient
- can be designed for nearly all process gases thanks to material selection and temperature regulation
- sensitive to particles entering the system
- requires special considerations when used with process gases that tend to be reactive at high temperatures
Liquid Ring Vacuum Pumps
Liquid ring vacuum pumps are rotating positive displacement pumps with an impeller that is eccentrically placed in a cylindrical housing. A liquid sealant flows through the vacuum pump, and the rotation of the impeller creates a liquid ring on the inside of the housing that seals the spaces between the individual impeller blades. The gas is conveyed in the spaces between the shaft, the individual blades and the liquid ring. Due to the eccentric placement of the impeller, the volume of these spaces initially increases, drawing vapor in through the inlet. As the impeller continues to rotate, the volume of these spaces is reduced, the vapor is compressed and then discharged through the exhaust port. The liquid ring vacuum pump can be operated as a simple continuous sealant flow system, or a partial or total recirculation sealant system.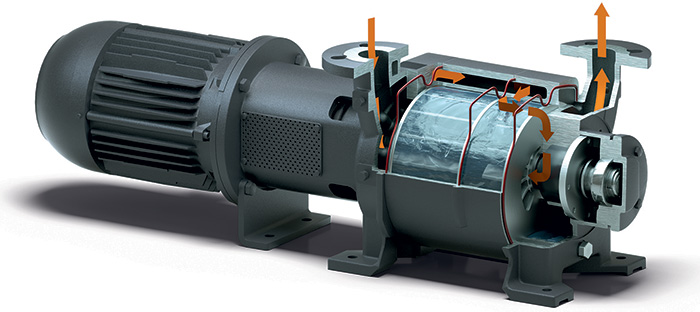
- not sensitive at all to vapor or liquid entering the system
- materials of construction can be tailored to the process gas
- possible contamination of the operating fluid with condensate from the process gas, affecting performance and making it necessary to subsequently treat the operating fluid before its disposal
- high energy consumption
- ultimate pressure depends on the vapor pressure of the operating fluid
Once-Through Oil-Lubricated Rotary Vane Vacuum Pumps
These are among the mechanical vacuum pumps used in the chemical and pharmaceutical industry. A two-stage once-through oil-lubricated rotary vane vacuum pump was developed in the 1960s and was designed for chemical and pharmaceutical processing. The rotary vane vacuum pumps have three distinguishing features when compared to other vacuum pumps that operate with the rotary vane principle: Two compression stages are stacked and connected to each other, facilitating initial compression of the process gas in the first stage and secondary compression in the subsequent stage, achieving a lower ultimate pressure.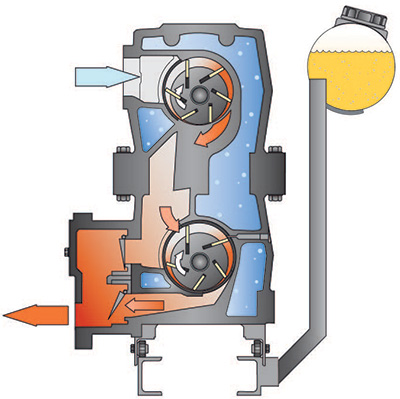
- high vacuum level
- extremely robust and reliable
- easy servicing
- suited for conveying acid vapors and monomers or products that lead to polymerization when other vacuum technologies are used
- operating fluids must be treated or correctly disposed of