Gasket information and the tests used to generate it can help users make the best possible equipment selections.
08/21/2015
Every industry has its own terminology. For example, depending on the frame of reference, the acronym "API" can mean American Petroleum Institute, active pharmaceutical ingredient or application programming interfaces. To know what is meant, one needs to know the context. In the case of industrial sealing products, the context is often a catalog published by the manufacturer, which to the uninitiated, may raise as many questions as it answers. Yet, accurately deciphering the information is vital to making informed decisions in the selection of the optimal seal for a particular application (see Table 1).
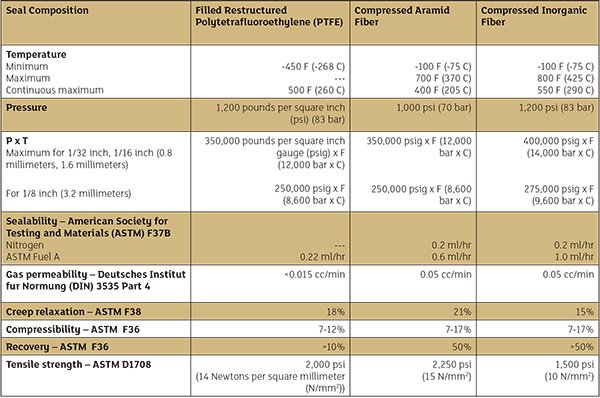
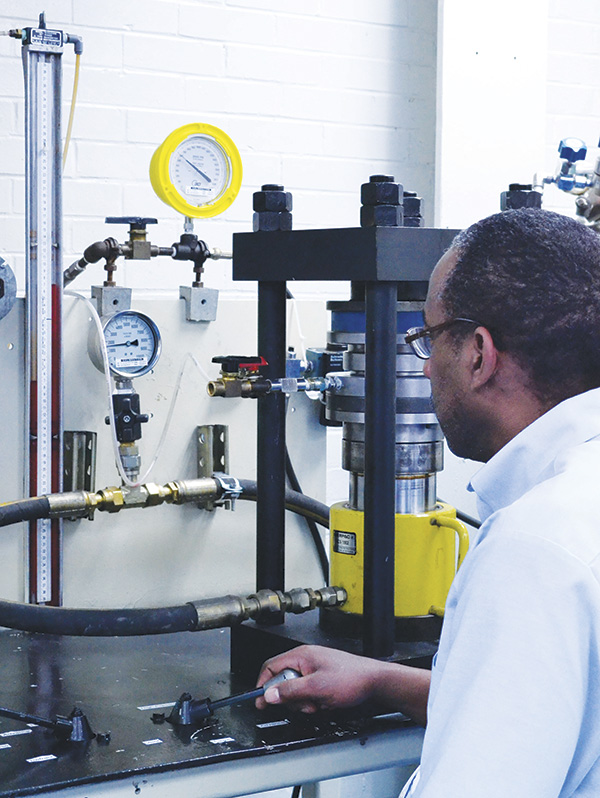