Protecting these two components can lead to longer equipment life.
06/18/2015
Last of Two Parts Motors represent a significant energy expense for any industrial plant. To minimize cost, users can ensure their motors run as efficiently and reliably as possible. Operators should focus on caring for bearings and windings, the two components that most commonly lead to motor failure. Last month's Motors & Drives column (Pumps & Systems, May 2015) detailed some common causes of premature bearing failure, such as lubrication and vibration, and steps that motor users and manufacturers can take to prevent these problems. Part 2 of this series will focus on winding failures.
Winding Failures
After bearing failures, winding failures are the next highest failure mode in motors. Windings fail because of temperature, coating or caking on the frame, overloading, and other problems. An industry rule of thumb states that for every additional 10 degrees C of winding temperature, the winding life drops by a factor of 2. Conversely, every 10-degree reduction in winding temperature doubles the winding life. A common practice is to specify "Class F insulation with Class B rise." Figure 1 shows the differences in temperature for the three most common insulation systems used in motors.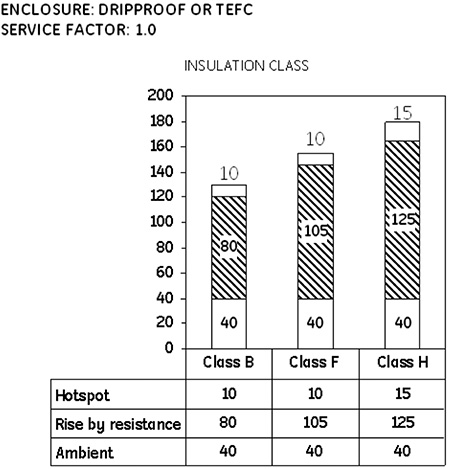
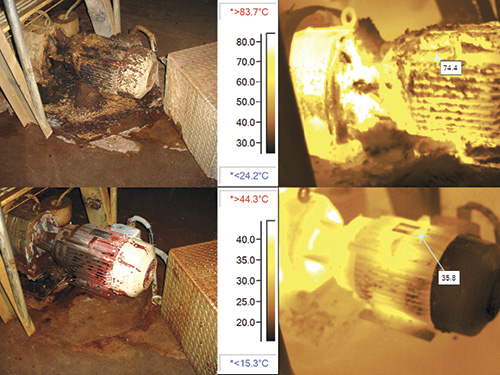