Energy efficiency is a hot topic in the process industry, and many authorities worldwide are preparing related regulations. First, the European Union (EU) created the Energy Related Products Regulations. Now, the U.S. Department of Energy (DOE) has introduced a regulation that specifies the Pump Energy Index (PEI) for clean water pumps, with the target of reducing energy consumption. After 2020, only pumps in the range of 1 to 200 horsepower (hp) that satisfy the PEI requirements are allowed on the market. In many industrial processes, pumping systems are responsible for 25 to 90 percent of energy usage. The energy consumption depends on the design of the pump and the installation, the specific application and the conditions and operation of the system. These components and factors must match in order to achieve the lowest possible energy and maintenance costs. Energy is often wasted because of inefficient or oversized equipment. To optimize the pumping system, users need to know the areas of energy intensity and how to boost the efficiency of the installed equipment. This optimization also helps cut down the carbon dioxide footprint. Image 1 demonstrates the role that energy consumption plays in the long-term costs of pumping systems. The right pump technology, properly sized for a specific application, can reduce energy consumption and the overall lifetime cost of the pump.
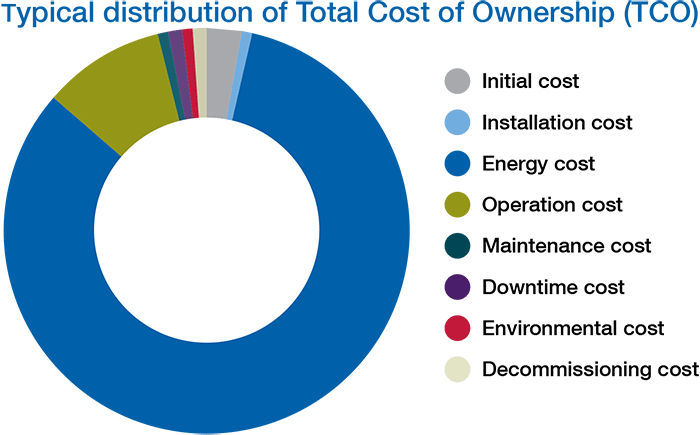