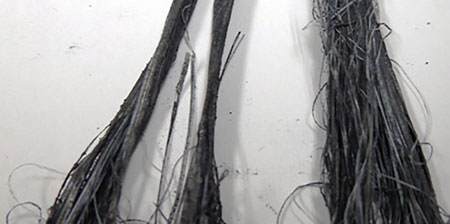
From a mechanical packing manufacturer’s point of view, there has always been an application where the braided mechanical packing has failed. Whether the application was in a pump, mixer, valve or another specialty piece of equipment. It is always a quick decision to look toward the braided packing as the primary cause of the failure or problem. People seem to arrive at this decision for a few reasons, because they could view packing as low or antiquated technology—maybe it is simply the last step in the process of getting their equipment back up and into service. When speaking to people about their equipment, there are never any issues with the equipment. It is possible that the braided packing was misidentified for the application. Whether the issue is from a single or a combination of contributing factors, each problem can impact performance and shorten a packing’s life expectancy.
Many new mechanical packing solutions will start from a single user request of a challenging application or further development and advancements in new raw materials. Mechanical packing manufacturers can spend many months, even years, evaluating materials and combinations of materials, striving for improved sealing performance.
Creating a new mechanical packing solution is driven by the desire to eliminate painful applications and extend sealing performance, which means thoroughly considering all the options. Is the sealing medium liquid or gas? Is the medium a liquid range from something abrasive to relatively clean? Is the medium on the caustic or acidic side of the pH scale? What if the medium was a gas? A gaseous medium could be inert, explosive or even a health hazard. Could there be concerns with emissions or vapors? Does the medium have a constant steady temperature or are there temperature fluctuations? Packings can be used in applications in high heat and bitter cold.
The Fluid Sealing Association’s (FSA) fourth-edition compression packing manual refers to the use of the “STAMPS” acronym. It is an easy and concise acronym to remember, one that can guide a user toward the pertinent details of an application logically and methodically every time.
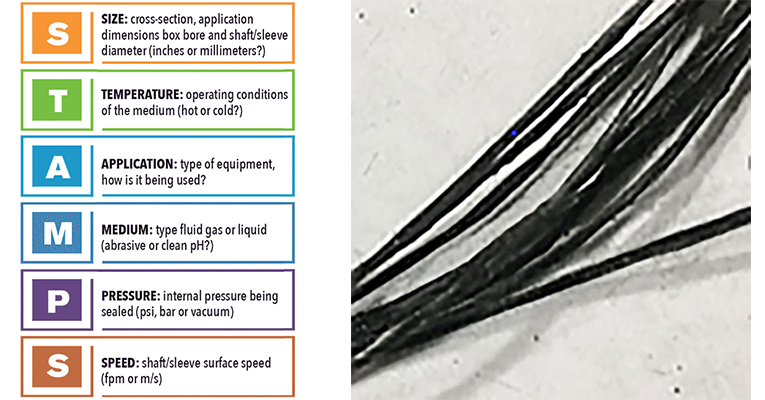
Be aware of any special requirements that need to be met and be sure to have the context and background on the specifics of the problem. Having these details, no matter how small or insignificant, can provide direction toward a solution for the design of a new packing set. There are commonly distinct features that make up a good quality packing. The first is strength. A good packing will need to be made of strong materials to resist the physical demands of pressures, temperatures and surface speeds. The next characteristic of a good packing is chemical resistance. The wider the pH range, the greater number of chemicals and the levels of concentrations a packing will be able to handle. The last characteristic of a good packing is resiliency. This allows for the packing material to deform under load and recover. A good quality packing needs to have some elasticity to its construction to energize and maintain a constant seal.
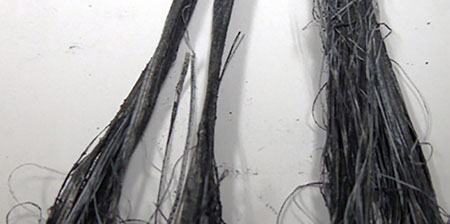
Once the application details have been identified, the focus would be to determine the best material options for the application. Should the packing be a carbon or a graphite yarn (Image 1)? Maybe it should be a synthetic blend of fibers, para-aramids, polytetrafluoroethylene (PTFE) or expanded PTFE (ePTFE) type of yarn (Images 2 and 3)? Looking at the potential benefits and weaknesses of each material type takes a strong knowledge of the material fibers and their characteristics.
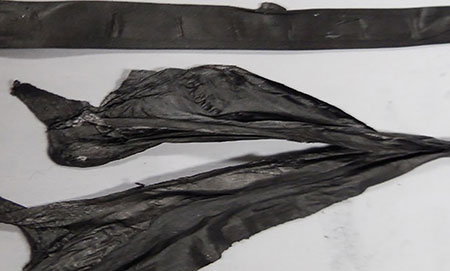
Just as important as the type of fibers in a packing is coating type. Coatings and lubricants are also components in the process to consider for a mechanical packing set. How is the lubricant going to be used? Will the lubricant be a sacrificial component of the packing or a blocking agent? Are there any restrictions on contamination of the lubricant or packing in the process medium?
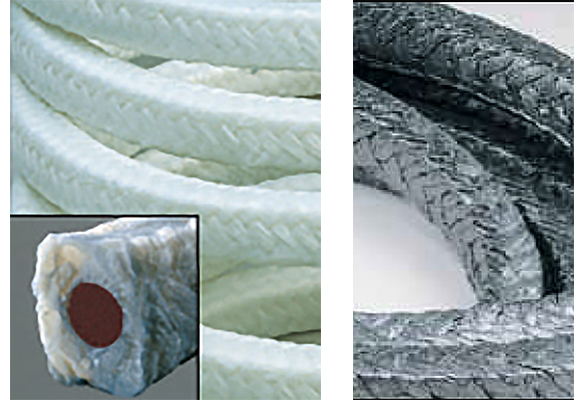
It is important to be able to identify the differences in braided packing construction such as interbraid (lattice) versus square braid packing (Images 4 to 6). It is also important to know why a braided packing is being specified for its features and benefits in an application—maybe it is because of the material, the combination of materials or even the type of construction. Some examples of packing styles that are used in equipment that have specific needs include braided packing with a rubber core (Image 4), used primarily to seal for shaft/sleeve run-out conditions and multi-fiber packing (Image 6) to seal aggressive heavy mediums with graphite-coated PTFE yarn and additional strength of Kevlar
corner reinforcement.
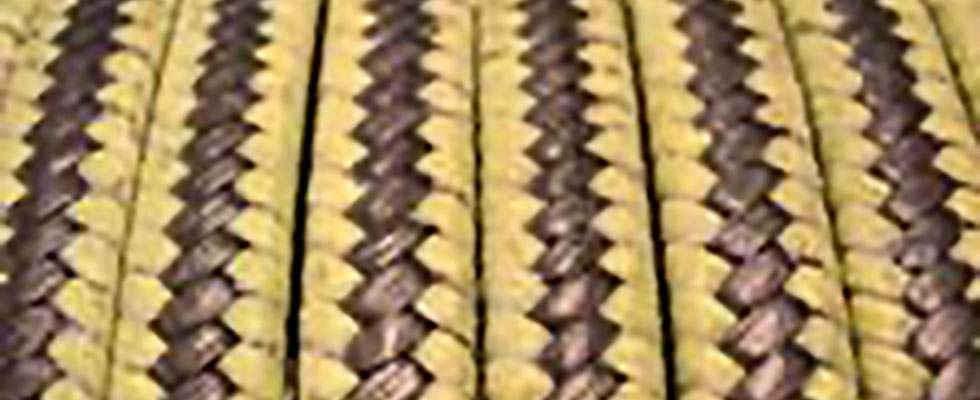
From advancements in material fibers and coatings in conjunction with using combinations of material types and improvements in the construction of braided packings, users have a greater selection of braided mechanical packings than ever before.