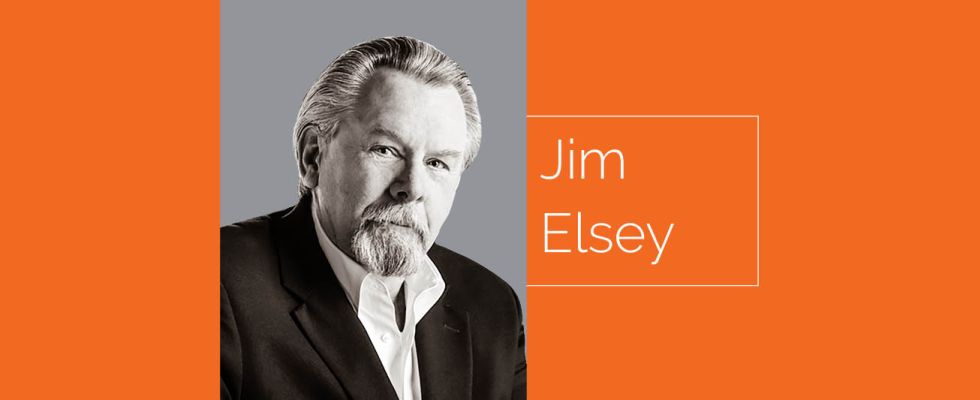
The title of this column is based on the old adage, “if a tree falls in the forest, does it make a sound?” The maxim’s question is really a test (philosophical thought experiment) to see if you know the difference between noise and sound. A brief explanation is that sound is what humans hear, and noise is unwanted sound and/or frequencies outside of our individual hearing range. So, if a human did not hear it, there was no sound, but there was noise.
As a side note, the frequency of the human hearing range is reported as being 20 hertz to 20,000 hertz (20 kilohertz [kHz]). In reality, it is more like 30 hertz to 17 kHz. As a comparison, the range for cats and dogs extends to 40 kHz.
Abstract
It is the belief of the author that before you establish site noise levels, require noise testing from the pump manufacturer or conduct noise testing (whether in the lab or the field), you should also acquaint yourself with the standards and be aware of both the cost and the limitations. I would be the first person in line for a quieter world, but according to Sir Michael Philip Jagger, you can’t always get what you want.
General
My interest in sound started as an audiophile’s quest for music fidelity in my 1960s stereo equipment (thank you, Miles Davis and Macintosh). Later, my fascination was burnished by my years spent operating a nuclear fast attack submarine. Pumps, compressors and turbines can transmit sound through the ship’s hull to the sea. The potential for equipment noise propagation to ambient is not a good thing if your mission is to remain undetected. For pumps, the generated sound energy is both a flow-induced noise (external) and flow noise (internal). To differentiate, the flow-induced noise is the energy transmitted to the surroundings, such as to pipes and supporting structures. To be complete in the evaluation, you would also need to add in the mechanical noise.
Pump Noise
For this column, we will focus on the total noise at numerous frequencies and a range of intensities generated by the combination of pump and driver that radiates to the surrounding area. We will assume the driver is an electric induction motor. When any pump is operated, it will generate noise at some level. As a matter of fact, a small percentage of the overall pump inefficiency manifests as noise.
Pumps with trimmed impellers will have different levels (higher). Pump noise estimates are normally based on pumping water at 68 F with the pump operating at or near the best efficiency point (BEP). Pump noise levels are a function of speed, fluid properties (especially specific gravity and viscosity), air entrainment, net positive suction head margin, position on the curve as a percent of BEP, piping (sizes, geometry and supports), operating clearances and pump foundations as a function of resonance, mass and rigidity.
To accurately predict what pump noise levels will be in the field (in situ) is not easy, as the ambient surroundings and site geometry are a major factor in the frequencies and intensity experienced and measured.
Most pump manufacturers will have data available for expected average pump noise levels. This will be for the pump alone and is not guaranteed because it will change once the pump is in the field coupled to a driver.
Motor Noise
In most every case, it is the driver that generates more noise than the pump, especially if the pump is operating near its BEP. This statement may not hold true for multiple stage pumps. You can expect higher noise levels if the motor is driven by an inverter or as the motor enclosure becomes more restrictive (open drip proof [ODP] versus totally enclosed [TEFC] versus explosion proof). Motor noise levels also increase with frame size, speed and horsepower. The motor manufacturer should have no issues supplying complete noise data on their equipment running alone (motor by itself). This is typically part of their standard engineering data submittal package.
Noise Testing
Most OEMs do not test pump sound levels at an in-house test facility. If they do, it is more of an anomaly than standard day-to-day operating procedure. Conducting noise tests at the manufacturer’s test facility is usually not commercially feasible, as it requires using a different motor, piping, ambient conditions, speeds, etc.
For further clarification, most OEMs cannot measure sound levels of the pump running alone because they cannot physically or acoustically isolate the motor from the pump, and they are usually not going to utilize the user’s actual driver for the test. If the tests are truly required and cannot be dismissed, note that American National Standards Institute (ANSI)/Hydraulic Institute Standard 9.2 offers means and methods to conduct these tests and adjustment correction factors.
I recommend that if a noise test is required, it should be conducted in the final setting with the actual driver and piping. You will need to have a contingency plan to mitigate unacceptable levels should they manifest (noise mitigation/correction structures are specifically designed and added), but this approach is usually less expensive (less drama) than conducting two tests and still having unacceptable levels.
Additionally, the pump OEM would not typically take steps to attenuate the background or reflecting noise in their facility, which is normally constructed of concrete and steel—a perfect worst case. I will acquiesce that some higher-end pump test facilities have temporary sound curtains or movable sound walls.
Further, the sound/noise as measured and/or attenuated at the user’s site is a function of their specific and unique ambient environment, which the pump OEM has no control over and consequently cannot guarantee. In summary, the levels measured in the OEM facility will be different than what will be recorded at the end user’s facility.
Industry Standards
ANSI/Hydraulic Institute 9.1-9.5 (specifically section 9.2):
“The purpose of the standard is to provide uniform test procedures for the measurement of airborne sound from pumping equipment.” This standard will thoroughly explain the test procedures and proper microphone placement for the tests for different pump geometries.
ANSI/Hydraulic Institute 14.3 (14.3.4.24 Sound):
This section offers guidance on adding two sound levels together and correction factors for multistage pumps and
impeller trimming.
ANSI/Hydraulic Institute 14.3 Appendix I (I.3.3.4):
This section offers guidance on noise mitigation for (internal combustion) engine-driven units.
Adding Noise Levels
Do not add motor and pump noise levels directly. The noise levels of a pump and motor are not directly additive, as they are logarithmic factors. When adding decibels, convert to logs first, then back to decibels. The log scale implies that when adding two noise sources that are different from each other, the louder noise will dominate.
Noise energy dissipates in the air by 6 dB as the distance doubles. Or, in other words, the 6 dB drop with doubling of distance is the drop in noise due to the energy being dissipated in the air. Distance is the main factor in noise attenuation.
Remember that a quiet pump is a happy pump.
As a result of the researching and writing this column, my wife has insisted I get a hearing test.
References
- ANSI/Hydraulic Institute Standards 14.3 and 9.2
- Cudina, M. and Prezelj, J., “Detection of Cavitation in Situ Operation of Kinetic Pumps: Effect of Cavitation on the Characteristic Discrete Frequency Component.” Abdulaziz Morgan Abdulaziz et al, Engineering Research Journal 164 (December 2019), M1-M14
- Dr. Lev Nelik, Pumps & Systems, September 2021, pumpsandsystems.com/your-guide-quelling-noise-vibration
- The Pump Handbook (4th Edition), Dr. Paul Cooper et al, section 10.3-10.24