In 2011, I wrote a five-part series on alternating current (AC) motors and motor efficiency. This column will go into more detail about the impact of efficiency. Efficiency defines how well a motor converts electrical energy into mechanical energy. If a motor were 100-percent efficient, only 746 watts would be required to produce 1 horsepower. If its efficiency were reduced to 50 percent, it would need 1,492 watts to produce the same output. Unfortunately, physics does not allow any machine to be 100-percent efficient, but larger motors can reach 96-percent efficiency. Even 1 horsepower motors can exceed 80 percent. Where do the excess watts go? The largest single loss (30 percent) is the stator resistance loss (stator I2R). If the stator wire size for a given motor horsepower is increased, resistance losses are reduced. The second largest loss (20 percent) is rotor resistance loss (rotor I2R). Larger rotor bars will lower resistance and, therefore, reduce these losses. One reason that premium-efficient motors are more expensive than lower efficiency models is the increase of copper in the stator and new rotor designs that allow larger rotor bars. The third largest loss (19 percent) is core loss. Core losses—composed of hysteresis and eddy currents—are a result of the continuously changing magnetic field in the steel laminations of the stator and rotor. Using higher quality steel can reduce hysteresis losses, while eddy current losses are decreased by using thinner and better insulated laminations. Lengthening the lamination stack will also reduce core losses by reducing the flux density within the stack. These improvements add to the cost of premium efficiency motors. The fourth largest loss (18 percent) is stray load loss. These losses usually increase with the motor load and can be reduced through proper motor design. Coming in last (13 percent) are friction and windage losses. Friction is caused by friction in the ball or roller bearings, and little can be done to increase bearing efficiency. Windage is a combination of the drag produced by the spinning rotor and the internal or external cooling fan. Fans are sized to meet a motor’s cooling requirements at the lowest possible energy requirement.
Nameplate Versus Actual Efficiency
A motor’s full-load efficiency can be higher or lower than its nameplate efficiency. The efficiency shown on the nameplate is the “nominal” efficiency. Nominal efficiency is defined as the average efficiency of a large population of motors of the same design. The nameplate on a 50-horsepower, 1,800-rpm motor shows the average efficiency for some number of motors that were tested. Any single motor may have an actual efficiency that is higher or lower than the one on its nameplate. However, a minimum efficiency must be met by any motor in the group. The nameplate for a 50-horsepower, 1,800-rpm motor shows a nominal efficiency of 94.5 percent. It could be higher, but its guaranteed minimum efficiency is 93.6 percent. This can be an issue if the engineering specifications require motor testing at the factory, and it performs under its nameplate rating.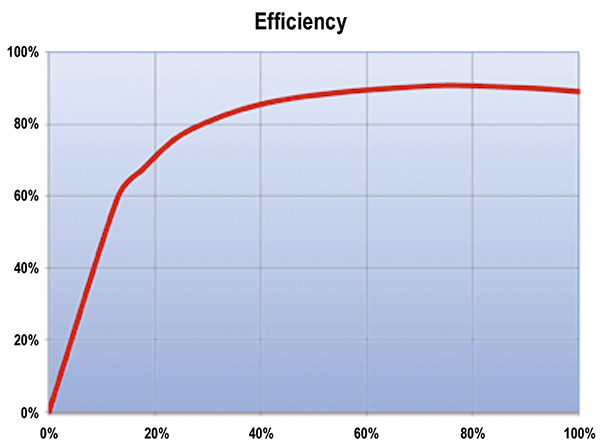