The pumping operation experienced an 80-percent reduction in energy use.
06/20/2014
Founded in 1637, Fiskeby Board AB, a paper mill in Norrköping, Sweden, has been manufacturing paper and board for 375 years. The mill had equipment installed that operated adequately and experienced few pump failures. However, expenses were high, and the mill operators believed that costs could be reduced with an alternative pump control solution. An industrial drive was installed in an attempt to decrease energy consumption and save money.
Pump Control Before the Drive
Before the drive was installed, flow control was achieved by running the pump at full speed against a valve that was nearly closed during most of the pump’s operation. This inefficiency wasted energy, similar to driving a car and pushing both the accelerator and the brake at the same time.After the Drive’s Installation
The system’s centrifugal pump moves up to 5,000 liters per minute and is operated by a 50-horsepower motor that runs at 1,720 rpm, at 60 hertz. This motor has a power factor rating of 84 percent. With the new drive, the centrifugal pump runs at variable speed depending on the level of the tank that it is feeding. This means it runs slower for much of the time, providing energy savings. The drive was built using an all-compatible drives architecture designed to provide compatibility, flexibility and ease of use.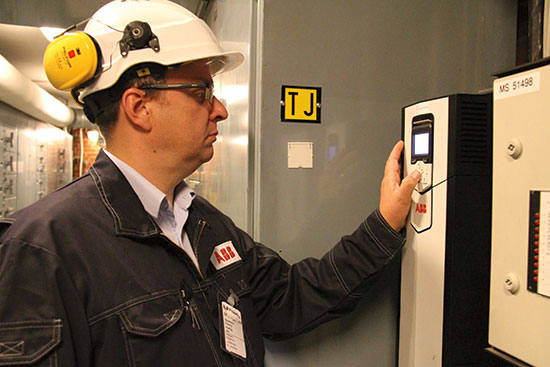