Operators are the eyes, ears and manipulators of switches and valves in their plants. They often receive training from a two-year associate degree program or on-the-job training. Their training may or may not cover how their equipment works or the significance of pump performance curves. Effectively training plant operators is crucial for maximizing plant uptime and minimizing maintenance and repair problems. Operators are expected to both identify and troubleshoot problems. They are trained to start, operate and shut down the plant. However, without understanding how the equipment should operate and the basics of a pump curve, troubleshooting will be difficult. Many operators feel that they have little control over the process and are subject to its whims. For example, they know when a pump experiences cavitation, but they may not feel that they have any control of the cavitation. They may identify the problem but feel they have no power to do anything about it. They may not realize that they have some limited control.
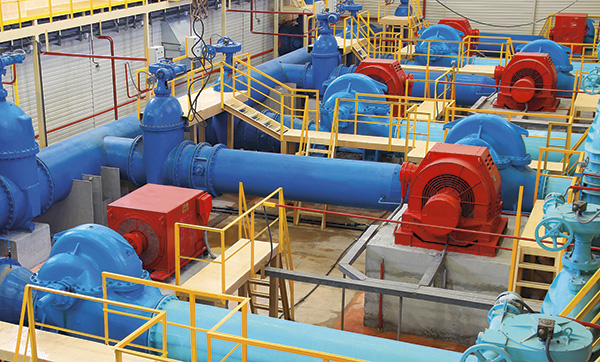
Look, Listen & Feel
Most operators use their senses to identify problems. However, they also must consider what has caused the evidence that they are sensing. For example, if a black mark appears on a tank near a hose, operators should ask why the mark is there. If they don’t determine the cause, damage may result. The hose could be rubbing the tank, and eventually, a hole will form in the hose, preventing the use of any equipment to which the hose is connected. Many problems can be detected before failure occurs by using these simple techniques. In many instances, however, when these clues are detected, failure is imminent. The look, listen and feel (LLF) method helps to gather data so that a permanent solution to the problem can be determined and implemented. The LLF method also helps operators become familiar with how their equipment behaves when it is operating well or when a problem exists.Pump Curves
Operators must be taught the basics of pump performance curves. They must know the relationships between pressure, flow, horsepower and net positive suction head (NPSH). These relationships should be taught for both centrifugal and positive displacement pumps. Little to no troubleshooting will occur if operators do not understand these performance relationships. Many operators know that the discharge pressure on a centrifugal pump will rise if the discharge valve is closing. They also may incorrectly assume that the pump is drawing more horsepower. This is because they may not understand the relationship between horsepower and flow. Simple concepts, such as pumping more product than the pump is rated for, mean more NPSH will be required to prevent cavitation. Because some operators may not understand these relationships, they think that they have no control over cavitation in their pumps. For example, most operators do not know that they can reduce the likelihood of cavitation by increasing a pump’s suction pressure by raising the tank level or pressurizing the suction source. They do not consider reducing the output from the pump to reduce the NPSHR. If a pump has a bypass to allow the pump to operate at different flows and head, operators can close or reduce the spillback flow to reduce the NPSHR of the pump and possibly reduce or eliminate cavitation. Cooling the incoming liquid is another way to reduce the possibility of cavitation, but this is usually a more difficult parameter to correct.Root Cause Failure Analysis
Simple root cause analysis helps identify the main source of a problem and is an action that the operator can implement when a problem is discovered. Many operators think their job is to identify a problem and then turn to someone else for a solution. While this may be true, the operator is the person looking at the problem and can gather data on the spot in order to identify a permanent solution.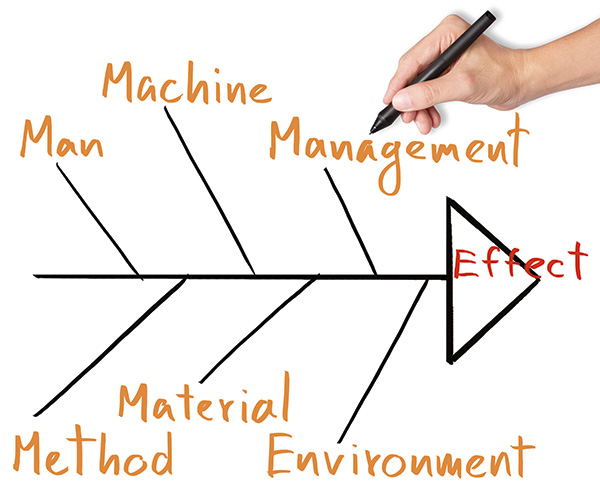