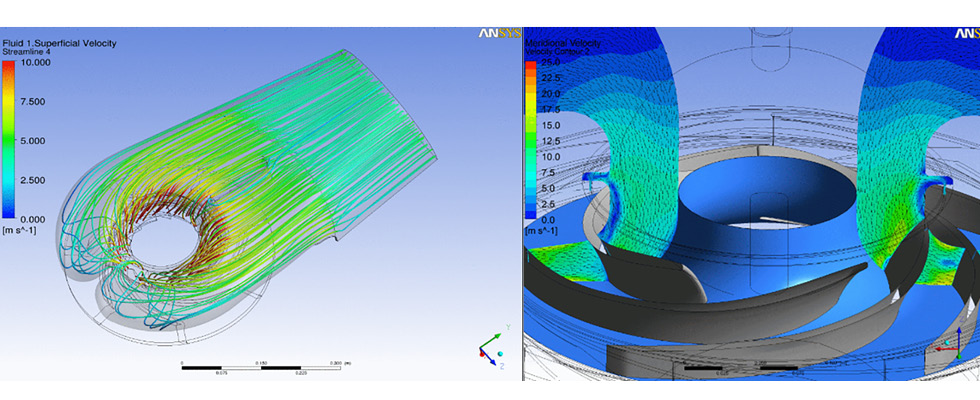
Many countries around the world are looking to advance their energy security and transition toward cleaner, more sustainable energy sources. In 2023, Italy took a step in this direction by launching its first combined cycle power plant equipped with an H-class gas turbine.
The new plant was the result of revamping an existing thermoelectric power station. The station was originally built in 1964 and was transformed into the first natural gas combined cycle plant in the country in 1992. A combined cycle plant uses both gas and a steam turbine, allowing it to produce more electricity while using the same amount of fuel as a simple cycle plant. Construction work on the plant took four years to complete, employing up to 1,000 workers during peak times, for a total investment of around 400 million euros.
The revamped plant now has a total electricity generation capacity of 780 megawatts (MW) and an energy efficiency of 63%, the highest output currently available from such technologies. Such efficiency gains have a direct impact on emissions reductions. The plant is expected to lower its carbon emissions (CO2 milligrams/kilowatt-hour [mg/kWh]) by up to 30% compared to the current average of the Italian thermoelectric fleet. Additionally, the plant will reduce its specific emissions of nitrogen oxides (NOx mg/kWh) by more than 70%. The new turbine is also technologically ready to mix up to 50% hydrogen with natural gas, aligning with potential advancements in hydrogen as a cleaner energy source.
To bring this project to fruition, both the end user and turbine supplier asked an Italian OEM to come on board from the project’s concept and design phase. The OEM was tasked with contributing to the definition of the main pumps’ technical requirements. This collaboration ensured the pumps would meet the stringent demands of the high-performance gas turbine, a key factor in the plant’s overall operational success.
The scope of supply for the project included six pumps in total: two horizontal high-pressure boiler feed water pumps (American Petroleum Institute [API] 610 BB4 type), two vertically suspended condensate extraction pumps (API 610 VS6 type) and three vertically suspended water circulation pumps (API 610 VS1 type). The boiler feed water pumps were the most technologically challenging, involving a great deal of customization.
The finite element method (FEM) and computational fluid dynamics (CFD) analyses were employed to check and optimize the pumps’ design. FEM analysis, which simulates structural response to stress, was applied to the pump and baseplate to enhance the skid’s dynamic behavior across the entire design speed range. This analysis also contributed to the design of the pump casings and tie bolts to withstand the most extreme operating conditions in terms of pressure and temperature. The impellers, diffusers and casings were developed using CFD analysis, which models fluid flow, combined with in-house prototype testing. The result of these efforts was an optimized first-stage impeller, engineered for low net positive suction head required (NPSHr) in both single and double suction configurations, with subsequent stages optimized for maximum efficiency.
Another area of customization involved the auxiliary equipment integrated into the pump skid. A key feature was the integration of a mechanical variable speed coupling, which enabled speed variation from 25% to 100% of the nominal speed, ensuring operational flexibility and reliability. The pump system also featured mechanical seals coupled with an API PLAN 23 system, which utilizes a closed-loop system with a pumping ring performing product circulation through a heat exchanger and back to the seal chamber. This provides enhanced cooling and lubrication for the mechanical seals.
A critical phase of the project involved validating the entire pump system through high-temperature testing. High-temperature testing is a specialized procedure to ensure the pumps meet the required mechanical performance standards and contractual requirements.
Following the successful completion of this project, similar high-pressure boiler feed water pumps were commissioned for two additional H-class turbine plant projects in the country. This example emphasizes the important role of equipment providers, such as pump manufacturers, in shaping an energy-secure and sustainable future.