A gas pipeline owned by Petrobras Energy Group runs through the rainforest in the Brazilian Amazon region. Located between Urucú and Manaus, there are two compressor stations required to boost the gas pressure in the pipeline for providing gas flow. The stations can only be accessed via a complex route along rivers in the Amazon rainforest or by helicopter. Reliability and low maintenance equipment is critical at the compressor stations due to the challenges related to accessing them. The natural gas for this 663-kilometer (km) pipeline is extracted from a gas field in Urucú and piped to the city of Manaus. This gas is provided to refineries and power plants. Because generators driven by gas powered turbines are used at the power plants to manage energy peaks, gas demand varies. This requires the compressors at the Coari and Juaruna compressor stations to start and stop reliably to effectively manage the demand. One of the critical components for ensuring the reliable start of the compressors is the delivery of seal gas when the compressor starts, stops and is in standby. For normal operation, filtered product gas is supplied to the seals. This is accomplished by taking gas from the compressor discharge and flowing it through a filter, using it to clean and flush the seal cavity, which is at suction pressure. This ensures that the seal is provided clean gas to deliver reliable operation. When the compressor runs slow or comes to a standstill, there is low or no differential pressure between the compressor discharge and suction, resulting in low or no seal gas flow. To manage this, an alternate means of providing clean seal gas is required.
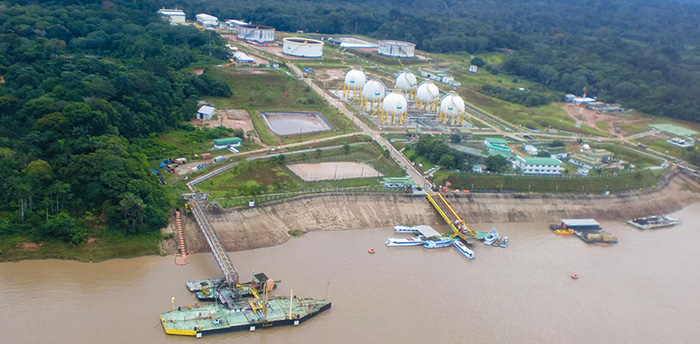
Converting the Seal Supply
The nitrogen used for seal gas during the start, stop and standby situations was an unacceptable permanent solution. The operator investigated possibilities to reduce costs and eliminate manpower associated with supplying the seal gas during these situations; a better long-term solution was required. In 2012 the decision was made to assess seal gas boosters, which used the product gas during low differential pressure and eliminated the nitrogen demand. When low or no seal gas flow occurs, a seal gas booster starts drawing gas from the compressor through the filter and delivering clean seal gas to the seals. This prevents contaminated product gas from entering the seal, which will affect the seal operation and potentially cause a seal failure during a compressor restart.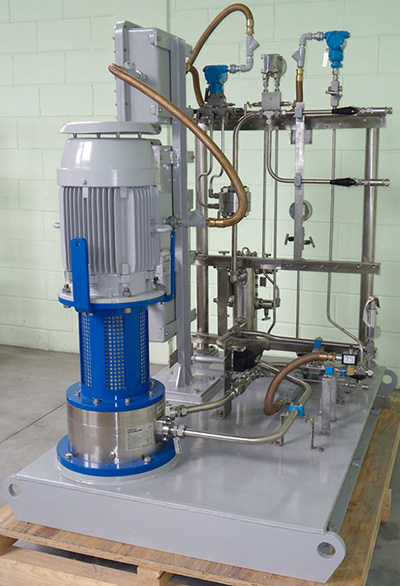
Trouble Free for Years
The operator found a seal gas booster, which requires virtually no maintenance, making it ideal for remotely operated compressors. These rotating seal gas boosters use a magnetic coupling to drive the rotating component, eliminating the need for a seal. The hermetically sealed unit eliminates leakage to prevent any climate-damaging methane from escaping into the atmosphere, making it an ideal choice for the rainforest. The operating principle was also simple, requiring no high demand of air utilities to operate. Only minimal air and power was required for implementation. With the high efficiency design of the magnetic coupling, which produces 98 percent less eddy current than a conventional magnetic coupling, the power consumption loss associated with torque transfer through the pressure barrier is dramatically reduced. These features made it the ideal seal gas booster to use for this application.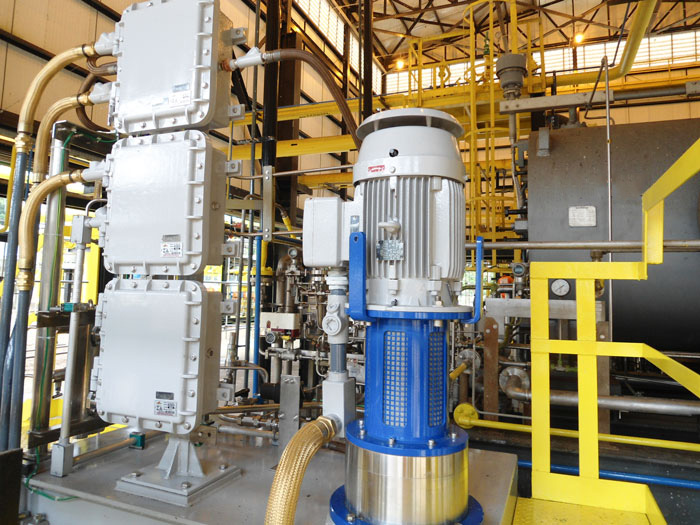