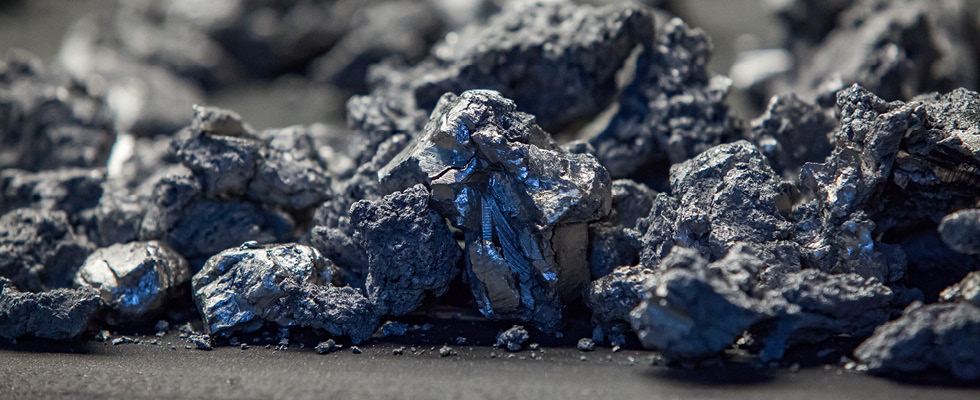
As regulatory standards tighten worldwide, there is an increasing demand for pumps and equipment capable of enduring harsh fluids. Pump manufacturers have consistently strived to meet these needs, enhancing pump construction to address evolving requirements while integrating stronger materials to bolster corrosion resistance and overall durability.
Some manufacturers adopt an approach of leveraging materials like stainless steel and titanium to engineer pumps that offer greater strength and corrosion resilience. This strategy ensures the company stays aligned with the changing necessities of several industries, especially those facing challenges in managing harsh fluids. These fluids range from chemically laden water to low-pH corrosive acidic solutions and seawater.
Stainless Steel: The Workhorse of Corrosion Resistance
Stainless steel is renowned for its resistance to oxidation, while its sanitary properties render it ideal for applications in food processing and hygiene-sensitive environments, ensuring compliance with rigorous regulations. Corrosion-resistant pumps integrate these materials across all components exposed to fluids, including the impeller, casing, motor frame, outer cover, strainer stand, bend, flange and sealing parts. Additionally, the mechanical properties of stainless steel, such as high tensile strength and excellent ductility, allow pumps to operate reliably under high pressure and in fluctuating temperature conditions. This versatility makes stainless steel pumps a preferred choice for industries ranging from pharmaceuticals to petrochemicals.
Titanium: Defense Against Corrosion
Titanium’s corrosion resistance and strength-to-weight ratio make it indispensable in specialized applications where conventional materials may fall short. Titanium pumps are particularly suited for environments with high levels of chlorides, such as seawater desalination plants, marine applications and chemical processing facilities dealing with aggressive solvents.
Titanium’s biocompatibility also opens avenues for the medical and food industries, where preventing contamination is crucial. Its ability to maintain structural integrity in extreme temperatures and corrosive environments ensures long-term reliability and reduced maintenance costs.
Cast Iron: A Durable & Cost-Effective Choice
Cast iron is another cornerstone material, prized for its robustness and impact resistance. Cast iron sump pumps are capable of withstanding high temperatures with minimal risk of internal shock. This material offers cost efficiency and expedited manufacturing processes, further adding to its appeal.
Cast iron is a time-tested material characterized by its long life and durability. Its high tensile strength makes it ideal for components exposed to significant stress, and its corrosion resistance properties make it a cost-effective solution for varied applications. These include municipal wastewater treatment plants, industrial sludge management and agricultural irrigation systems.
As wastewater regulations become increasingly stringent, the role of advanced materials in pump manufacturing cannot be overstated. Stainless steel, titanium and cast iron each bring unique properties that enhance the performance and longevity of pumps in challenging environments.
By leveraging these materials, manufacturers can ensure their pumps not only meet but surpass the rigorous demands of modern wastewater management. This commitment to innovation and quality will continue to drive the industry forward, safeguarding water resources and protecting public health.