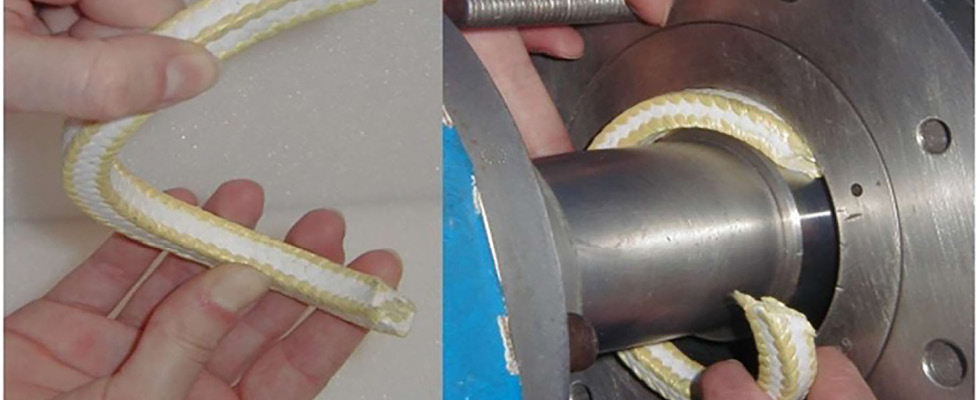
In the intricate tapestry of industrial machinery, one often overlooked yet indispensable component stands out: the mechanical seal. From ancient civilizations to modern-day industries, mechanical seals have played a pivotal role in ensuring the smooth operation of pumps, compressors, turbines and other critical equipment. As we delve into the history of mechanical seals, we uncover a fascinating story of innovation, adaptation and technological advancement, with a focus on the reduction of carbon emissions over the years.
The origins of mechanical sealing can be traced back to ancient civilizations, where ingenious methods were devised to contain fluids and prevent leaks in early machinery and irrigation systems. In Mesopotamia, clay was molded and shaped to form seals for pottery vessels and irrigation channels, laying the foundation for sealing principles. Similarly, ancient Egyptians utilized animal fats and plant fibers for waterproofing and sealing purposes to preserve valuable resources, showcasing an early understanding of the initial groundwork for what would later be known as packing.
During the Industrial Revolution, a pivotal moment in the history of mechanical seals occurred with the emergence of gland packing as a major advancement in sealing technology. Gland packing, a method originating from ancient sealing techniques, changed industrial machinery by addressing the pressing need for more effective sealing solutions.
Gland packing consists of rope or fibers, typically made from natural fiber materials like flax, hemp or cotton, wrapped around a rotating shaft and compressed between the shaft and housing by an adjustable gland follower. This compression creates a barrier that prevents the leakage of fluids, such as water or steam, in pumps, engines and other mechanical equipment. The tight packing of fibers effectively seals the interface between the rotating shaft and the stationary housing, thereby reducing the risk of leaks and ensuring the smooth operation of industrial machinery.
The significance of gland packing during the Industrial Revolution cannot be overstated. It provided a reliable and cost-effective solution to the widespread problem of fluid leakage in steam engines, water pumps and other machinery essential to driving industrial processes. By minimizing leaks, gland packing improved the efficiency and performance of equipment, leading to increased productivity and economic growth during this transformative period in history. Gland packing’s simplicity and effectiveness was improved though further innovations in sealing solutions, such as stuffing boxes and lantern rings, which further enhanced sealing performance in industrial equipment. Moreover, gland packing laid the groundwork for the development of today’s modern mechanical seals by demonstrating the fundamental principles of sealing technology.
The 20th century witnessed rapid advancements in sealing technologies, driven by the demands of advanced industrialization and wartime needs. World War II spurred innovations in sealing solutions for military equipment and machinery, leading to the development of synthetic materials such as rubber and plastics. These materials offered improved durability and resistance to harsh operating conditions, revolutionizing mechanical seal applications in diverse industries.
The 20th century witnessed the birth of end-face mechanical seals, marking a significant milestone in sealing technology, where the rotating equipment shaft was no longer used as a dynamic sealing element. These mechanical seals were introduced with a modular approach, separating the wearing components of the sealing device from the equipment assembly, and instead attaching sealing rings and their supporting components to the equipment’s shaft and housing. This innovation did require more care during installation, as the components had to be installed piece by piece into the equipment, but it nearly eliminated equipment sealing wear and reduced power requirements and maintenance while enhancing efficiency and reducing downtime in industrial operations.
Building upon the foundation of component seals, the latter half of the 20th century saw the rise of cartridge seals. These seals integrated all sealing elements into a single, preassembled unit, simplifying mechanical seal installation procedures and minimizing the risk of installation error seal failure. Cartridge seals quickly gained popularity across industries for their simplicity and reliability, furthering the demand and advancement of cartridge mechanical seal technologies. The development of compressor gas seals in the late 20th century revolutionized sealing solutions in high-pressure, high-speed applications. Utilizing seal face topography, these specialized mechanical seals effectively sealed the interface between rotating and stationary components in gas compressors and turbines, minimizing gas leakage while enhancing equipment efficiency.
Metal bellows mechanical seals were another notable innovation introduced in the mid-20th and early-21st centuries. Featuring flexible metal bellows as the spring unit and dynamic sealing element, these seals offered superior resilience and durability compared to traditional mechanical seals with elastomeric secondary seals with coiled springs. Metal bellows seals used both elastomeric secondary sealing elements and nonelastomeric secondary sealing elements, like flexible graphite. This contributed to improved operational reliability across various industries with applications in demanding environments involving high temperatures and corrosive fluids.
As awareness of environmental and safety concerns grew, regulatory agencies began imposing stricter standards for industrial equipment. To comply with these more stringent emission regulations, operators and manufacturers continually developed new sealing solutions that minimized process emissions. One notable solution to address the emission regulation challenges was the adoption of dual cartridge mechanical seals. These mechanical seal arrangements offer enhanced sealing performance by incorporating two mechanical seals in a single housing, separated by a barrier fluid. This configuration minimizes the risk of process leakage reaching the atmosphere, ensuring compliance with regulatory emissions requirements while maintaining operational efficiency. Dual cartridge mechanical seals provide additional safety through redundancy, allowing for process containment in the event of a seal failure, further enhancing safety and reliability in industrial processes.
In the modern era, mechanical seal manufacturers face new challenges posed by evolving industrial trends and technologies. High-pressure and high-temperature applications demand seals capable of withstanding extreme operating conditions without compromising performance or equipment efficiency. Innovations in seal designs, uses of specialized coatings and advanced materials and advancements in seal support systems have addressed many of these challenges, enabling seals to operate reliably in the most demanding environments. Further safety progress has been made with the integration of internet of things (IoT) and sensor technologies, enabling real-time monitoring and predictive maintenance of mechanical seals while revolutionizing asset management practices and enhancing operational efficiency.
Looking ahead, the future of mechanical seal technology is likely to have a continued emphasis on sustainability, efficiency and reliability. Advancements in materials science, nanotechnology and additive manufacturing are expected to further enhance seal capabilities, performance, reliability and longevity. Additionally, the integration of artificial intelligence and machine learning algorithms could revolutionize seal design optimization and enable predictive modeling and virtual testing of seal performance in real time. As industries embrace emerging technologies, mechanical seals will continue to play a crucial role in ensuring the smooth and reliable operation of machinery and equipment, while contributing to the inevitable industrial development and growth.
The evolution of mechanical seals is a testament to human ingenuity and innovation, building on centuries of technological advancement and industrial progress. From ancient sealing techniques to modern marvels of engineering, mechanical seals have been instrumental in shaping the industrial landscape.
We invite your suggestions for article topics as well as questions on sealing issues so we can better respond to the needs of the industry. Please direct your suggestions and questions to sealingsensequestions@fluidsealing.com.