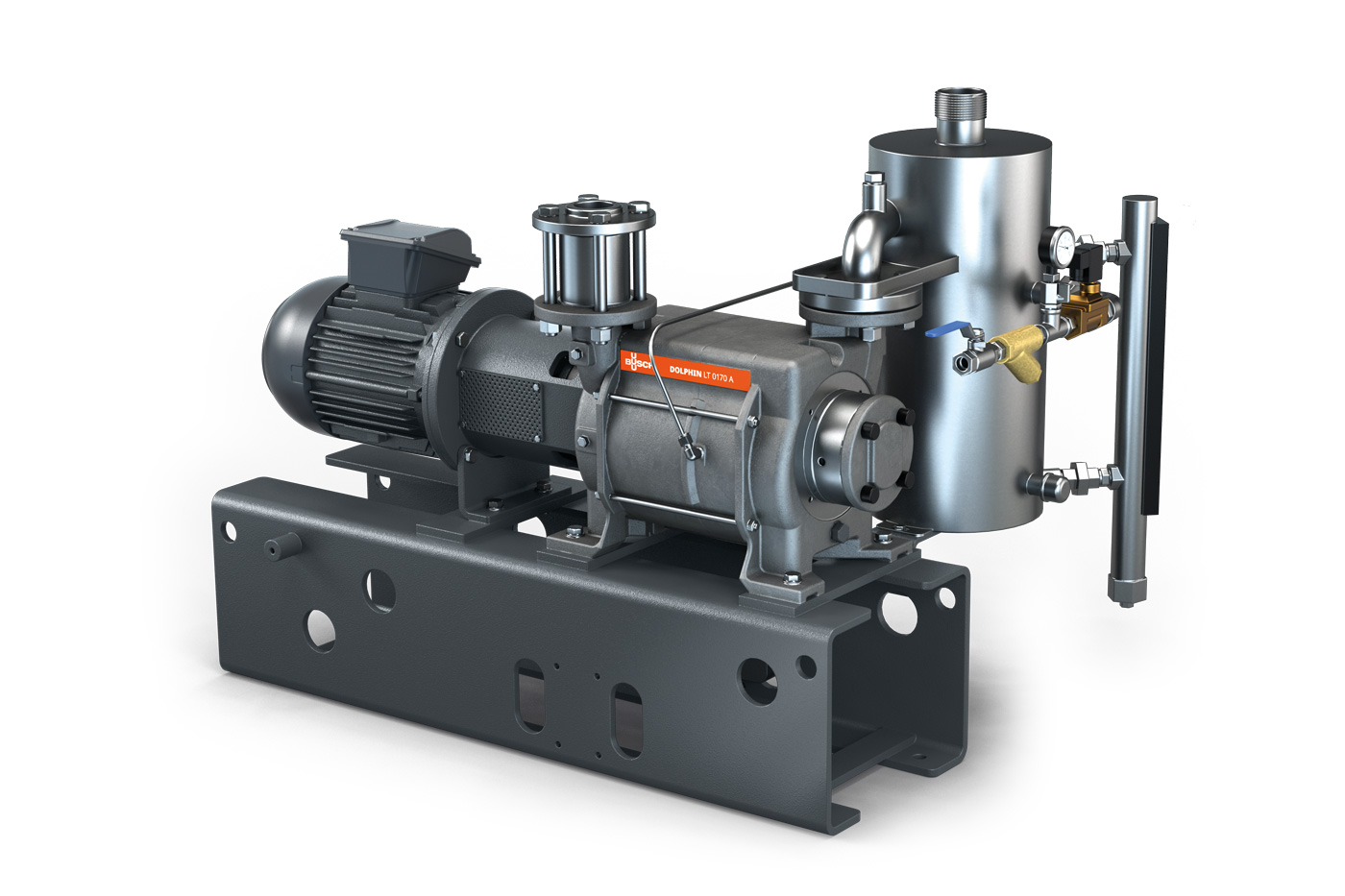
When selecting the right capital equipment for an application, the liquid ring vacuum pump may be seen as archaic and inefficient. However, labeling this technology that way can be an oversimplification. This article is intended to help adjudicate the liquid ring vacuum pump’s reputation by describing its middle ground and its positives (and potential negatives) with technical guidance.
There is a reason why liquid ring pumps are chosen for critical infrastructure applications like power generation and offshore oil and gas—when properly applied, they are reliable. That said, it is important to first summarize the drawbacks of liquid ring vacuum pumps: they consume more energy than alternative technologies and use too much water.
Energy Consumption
In applications with little or no condensable vapor loads, liquid ring pumps will consume more energy to accomplish the same compression than a comparably sized alternative technology like a dry screw, dry claw or rotary vane vacuum pump. The excess is usually published as 20% to 25% however, depending on the vacuum levels, it can be more than that.
In applications that have high amounts of condensable vapors, that efficiency gap can be closed (if not overcome) due to the “condensing effect.” In such applications, liquid ring pumps act as a direct-contact condenser, reducing the volumetric gas load inside the pump and, therefore, increasing the overall intake volumetric capacity. The greater the difference between the saturated gas temperature at the inlet of the pump and the seal fluid temperature, the greater the effect. The condensing effect occurs with little to no consequence on the absorbed power. In the right circumstances, the energy gap can be closed and a supplemental generator is not required.
Water Consumption
Liquid ring pumps require fluid to create the seal between the inlet and discharge pressures, thus fundamental to their operation. In many applications, this fluid is water, which is why liquid ring pumps are commonly referred to as water ring pumps. After performing its duty as a pressure seal, the seal fluid is expelled at the discharge in combination with the process gas. The liquid and gas phases are promptly separated, and what is done with the fluid establishes the pumps’ net thirst.
There are three potential scenarios.
1. In some applications, this seal fluid is sent to a floor drain or some other treatment system. This is referred to as a once-through configuration and often what users believe makes the liquid ring vacuum pump wasteful.
Applications applying this mode of operation are generally those that expect a high amount of particulate carryover from the application since the once-through operation continuously flushes the pump from potential product buildup. Essentially, this design helps prevent a sticky situation.
2. In other installations, the seal fluid can be recycled, passed through a heat exchanger to remove the heat of compression and condensation, then sent back into the pump to perform another round of its mission. Referred to as “total or full” recovery, applications implementing this method are usually cleaner in the sense that process gases are not expected to contain excessive particulate carryover. Furthermore, full recovery installations are often those where the continuous disposal of contaminated water or condensed solvents is undesirable.
There will be other trade-offs to consider, depending on the heat exchange type/design and the required vacuum level. Put simply, a water-cooled heat exchanger will increase facilities’ cooling water requirement, while an air-cooled heat exchanger will increase overall power consumption and require consideration paid to installation surroundings and max ambient conditions.
For operation at rough vacuum levels or for liquid ring pumps with large seal fluid flow rates, a recirculation pump may be required to overcome head losses in seal fluid pipework from the discharge separator back to the pump.
3. In a partial recovery configuration, a portion of the warmer discharge seal fluid is recycled and combined with a supply of fresh fluid before entering the pump. This effectively minimizes the amount of fresh fluid required. Pump manufacturers will often cite partial recovery modes saving up to 50% fluid usage. The actual amount of savings will depend on the vacuum level requirement, temperature of freshwater and how much heat is added to seal liquid throughput.
The seal fluid configuration can seem like a boundless game of puts and takes, or worse, a shell game of “hide the utility requirement.” The good news is that application characteristics (particulate carryover, presence of solvents, degree of condensable vapors) will often deem one method more pragmatic than others. Corporate energy and water initiatives can then be addressed by implementing the design and control scheme intelligently.
If there are liquid rings in a facility, users should check to see how they are configured. If installed in a once-through configuration, a bit of minor pipework can save money. Energy and water consumption are the two most cited deficiencies of liquid ring vacuum technology. Hopefully the above helps explain the circumstances in which one might mitigate those gaps.
Additional Advantages
Other advantages of liquid rings include:
Solvent recovery
In some chemical and pharmaceutical applications, it is desired to recover the process gases (solvents) for sale as a byproduct or re-use in the application. Using a liquid ring pump with the solvent as the seal fluid can be a solution to accomplish this (see condensing effect above) while maintaining a space-conscious footprint.
Temperature rise
When pumping gases with relatively low auto-ignition temperatures, it is desirable to keep temperatures low. After all, fires are not good for productivity. In a liquid ring pump, the heat of compression and condensation is absorbed by the seal fluid. Since liquids have higher specific heat capacities than vapors, the temperature rise across a liquid ring pump is much lower than alternative dry running technologies.
Construction flexibility
Mechanically speaking, liquid ring pumps are much less complex than other technologies (especially dry running alternatives). The shaft-mounted impeller is enclosed in the cylindrical body, which is capped by port plates and end casings, with tie rods holding it together. The tolerances between the impellers, body and end plates are wider than those found in dry running claw or screw pumps, which require tight tolerances to create the seal between the inlet and discharge pressures.
These wider tolerances, in addition to the lower temperature rise (and consequently, less thermal expansion), make liquid rings more suitable for construction in varieties of metals. Furthermore, liquid rings have seemingly endless design options for rotational speeds, bearing locations/lubrication and seal types. Whether the application involves air or potentially toxic/corrosive vapors, there is a suitable liquid ring configuration.
Pumping capacities
Because of the mechanical simplicity, liquid ring pumps are available in larger sizes for applications requiring high flow rates. For installations not requiring redundancy, this means only a single piece of equipment needs to be installed and maintained versus the multiple pumps that would otherwise be required.