In the east African country of Ethiopia, high-tech sugar production plants have been the focus of food-processing investments. These plants rely on diffusers—large, horizontal installations that extract sugar from sugar cane. Each diffuser can extract up to 12,000 tons of sugar per day. Horizontal diffusers in sugar extraction typically measure 64 meters (m) long, 14 m wide and 8 m high. Twelve juice troughs are distributed along the length of the lower part. A chain conveyor above the troughs carries sugar cane at 0.6 m per minute after it has been shredded at the plant entrance. Water washes the cane in the cross-counter current, increasing the sugar content from one trough to the next. "With an average sugar content of 12 percent, sugar cane is an ideal raw material for producing sugar," said Torsten Jüttner, technical project manager at BMA Automation GmbH in Braunschweig, Germany. His company specializes in the construction of sugar production plants, particularly in African countries. "Almost a dozen of these plants are planned to be built within a decade," Jüttner said. "We've already received the orders for the first two factories, and we're in the implementation phase."
Compact Starters
For the first two plants, Beles 1 and 2, BMA implemented a modern automation approach. The industrial controls were organized through a standard configuration—an IO-Link, which is a point-to-point serial protocol to allow communication with sensors and/or actuators. It decreased space requirements and installation costs and ensured ease of operation. "The combination of compact starters for the electric drives and communication via IO-Link has proven to be the ideal solution here," said Han Janssen, who is responsible for hardware design at the Braunschweig operation. The configuration saves up to 60 percent on installation and wiring for the plants. One plant includes 50 drives, 35 of which are actuated by compact starters. Twenty-eight electric motors turn the vertically oriented, 5-m spindles in the diffuser. These spindles break up the sugar cane to optimize the wash-out effect. The 11-kilowatt (kW) drives consume 22.5 amperes (A) of power.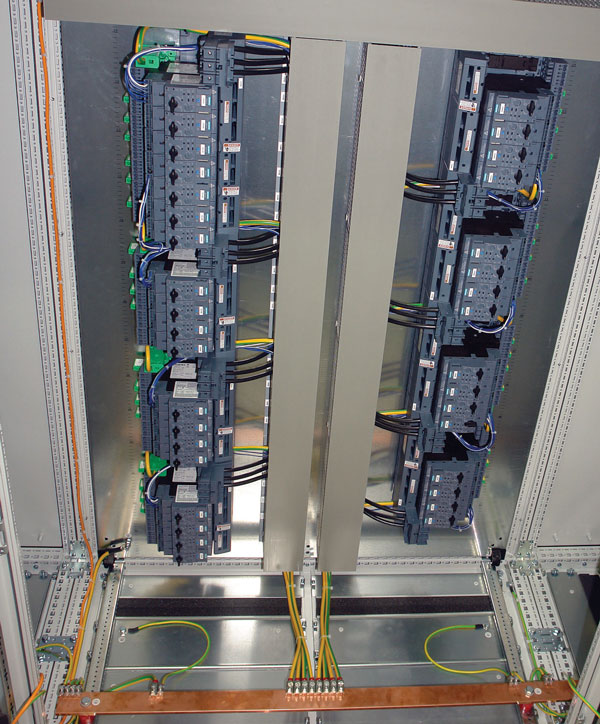
Vertical Mounting
Routing cabinets simplify cabling on the left and right of each control cabinet. This configuration works well with large and small drives alike. The compact starters are mounted vertically on the support systems in the control cabinets. The vertical placement "not only saves space but also achieves a very clear overall layout," said Janssen. Terminal blocks are not required, thanks to the central in-feed and compact starters located on the support system. "The user in Ethiopia can also connect the motors much more easily and ergonomically during installation," said Janssen. IO-Link communication can connect four compact starters into a single group. Three wires connect the first starter in the series to the IO-Link master, and pre-assembled flat cables connect the remaining three.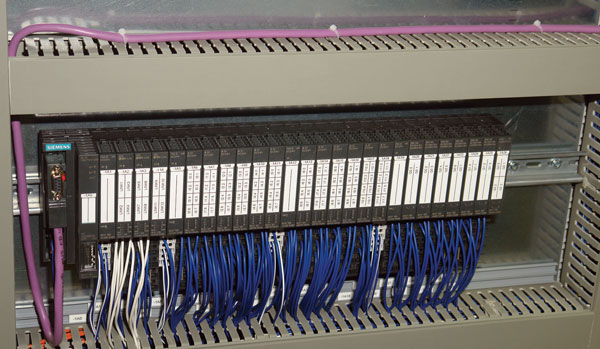