Sweden's largest dairy cooperative employs digital dosing pumps for the plant's clean-in-place system.
07/22/2015
Based in northern Sweden, the Milko dairy company develops and markets natural dairy products. It is the largest dairy cooperative wholly owned by Swedish farmers and the fifth-largest food company in Sweden. Committed to ideals of natural food, openness and innovation, the Milko team decided to employ a dosing pump range for the plant's clean-in-place (CIP) system. The pumps combine precision with ease of use, ensuring the most sanitary environment possible.
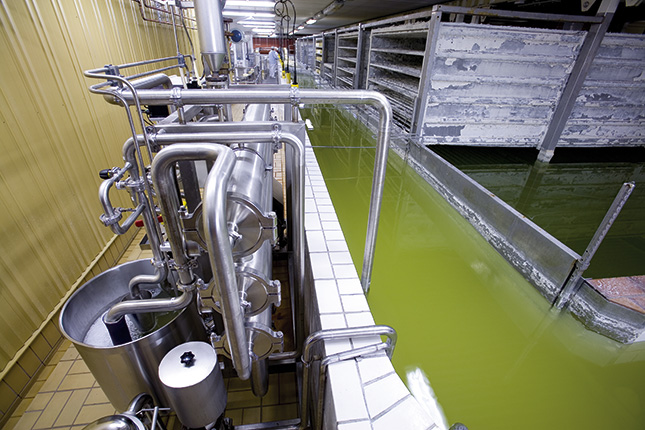