05/12/2015
First of Four Parts
A reliability professional recently asked me for spare parts recommendations. His global fertilizer plant had used a piecemeal approach during the last 20 years that frequently failed to meet expectations. After unplanned shutdowns, the plant remained down for two days when it should only have been down for 18 to 24 hours.
His latest challenge was setting up spares for a greenfield methanol plant. He said he had three different manufacturers that supplied him with turbine parts alone. "Surely, the spares that we stock for a particular rotating machine should be somewhat generic," he said.
His approach was familiar and standard practice for many in his industry. I recommended that this fertilizer plant should abandon the way it—and others—had made spare parts decisions in decades past. The focus of this series is on how modern spare parts programs should be handled in 2015.
Find the Root Cause
In the U.S., thousands of process pumps achieve mean times between failures (MTBF) of only a year or less. However, in several identical services, MTBF values of more than five years are common. A spare parts management program will differ depending on each plant's MTBF value. Any two refineries or hydrocarbon-based fertilizer plants may have identical designs. However, their respective staffs may not have the same training or motivation concerning spare parts management. One plant may often take greater risks. For example, some plants allow adequate time for turbine warm-up while others use the dangerous "full speed ahead on lukewarm" approach. In another instance, a plant will replace failed parts before understanding why the part failed in the first place. Figure 1 and Image 1 refer to examples of replacements made without fully understanding the underlying cause of the failure.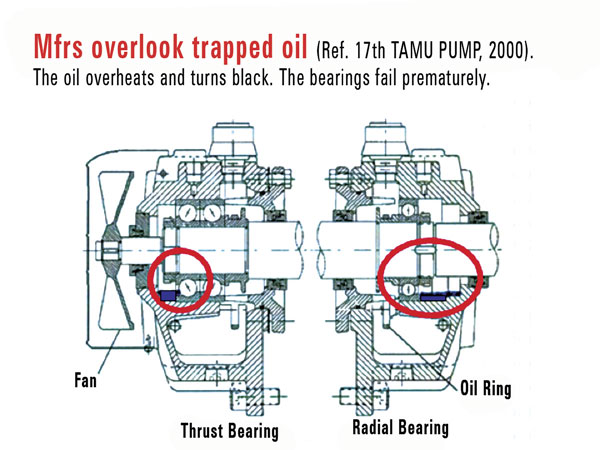
Bearing Failures
The pump with the bearing housings in Figure 1 required bearing replacement. But why did the bearings fail? Lubricant oil was trapped between the bearings and could not escape through their respective end caps. Trapped oil will overheat, and the carbon residue will degrade both lubricant and bearing (see Reference 1). Unless someone recognizes the problem, the degradation will repeat itself. Bearing life will remain short and cost the facility dearly over the equipment's life cycle. In Image 1, an oil ring shows substantial abrasion damage. Cheap oil rings are not usually stress-relief annealed. They will become out-of-round and will slip and skip. Also, unless the driving and driven shafts are installed parallel to the true horizon, oil rings will run downhill and often make contact with bearing-internal components. Abrasive wear will slow down the oil rings, and contaminated oil feeds into the bearings.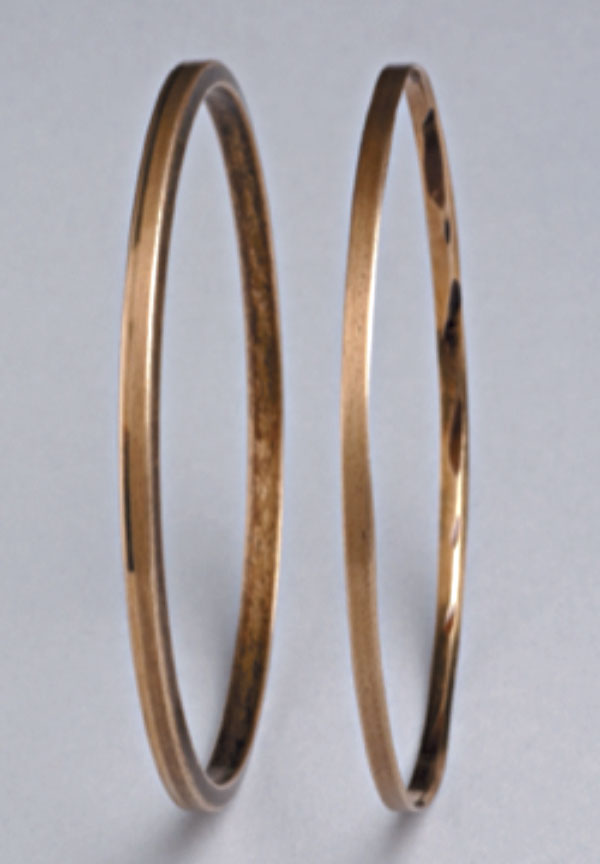
The First Step is Training
When Figure 1 and Image 1 were shown to groups of maintenance and reliability technicians in four different countries, it was clear that fault-inducing details were consistently being overlooked. Organizational initiatives such as asset management and operational excellence had gained prominence while attention to detail and systematic acquisition of highly relevant in-depth knowledge remained vastly underappreciated. Understanding these details is the true key to asset performance. Reliability professionals must learn to implement design, maintenance and operating knowledge responsibly. There must be accountability, even-handedness and equitability. An ethical reward system needs to be in place for knowledge to be practiced with unerring continuity and wisdom. When facilities provide the necessary knowledge in well-structured programs, they will need fewer spare parts and increase equipment reliability.A Chance to Upgrade
Plants and facilities staffed by highly competent maintenance and reliability professionals hate repeat failures. These professionals loathe unplanned downtime events. They view every single maintenance intervention as a challenge to their desire to upgrade, or to design-out the need for excessively frequent preventive maintenance actions. All repeat failures either result from the root cause of the failure being undetermined or remedial action has not been pursued. Highly competent maintenance and reliability improvement professionals will never be at ease with either of these two possibilities. Competent practitioners view these challenges as personal affronts—like a medical doctor losing a patient to the common cold. Part two of this series will examine how these professionals can better organize, pool and judge spare parts quantities to respond to root cause failures without incurring excessive costs. Read it here.
References:
- Bradshaw, Simon; Bradshaw et al., Proceedings of the 17th TAMU International Pump User's Symposium, (2000)
- Bloch, H.P., "Pump Wisdom: Problem Solving for Operators and Specialists," (2011) John Wiley & Sons, Hoboken, NJ
- Bloch, Heinz P., (1998) "Machinery Reliability Improvement," 3rd Edition, Gulf Publishing Company, Houston, TX
- Bloch, Heinz P., and Allan Budris; (2013) "Pump User's Handbook: Life Extension," 4th Edition, Fairmont Publishing Company, Lilburn, G
- Bloch, Heinz P.; Updating your Sealing Knowledge," Hydrocarbon Processing, March 2008