07/14/2015
Reciprocating compressors are a vital part of the oil and gas refining process. Without safe, reliable and efficient machines, facilities will face unexpected downtime, costly repairs and lost production. Fortunately, the development of modern monitoring software options has allowed refineries to detect dangerous faults early. They have the opportunity to correct them before they become catastrophic failures.
Liquid Entrainment
One monitoring software solution recently identified a liquid entrainment problem on a reciprocating compressor at an oil and gas refinery. The program detected that discharge pressure values were spiking as high as 40 bar gauge (BARG), when they were expected to stay steady at around 30 BARG. During the next two weeks, the software detected fluctuations in discharge pressure as high as 40 BARG and as low as 15 BARG. The software provider diagnosed the apparent cause as liquid entrainment within the system. This compressor system is equipped with a gas discharge cooler and a discharge cooler bypass temperature control valve (TCV) that is used to control temperature downstream of the cooler at a predetermined set point. When the TCV is partially bypassing the discharge cooler—usually on colder days—liquid forms in the cooler as a result of the predominant flow path bypassing the cooler. Over time, this accumulating liquid decreases available flow area through the coolers.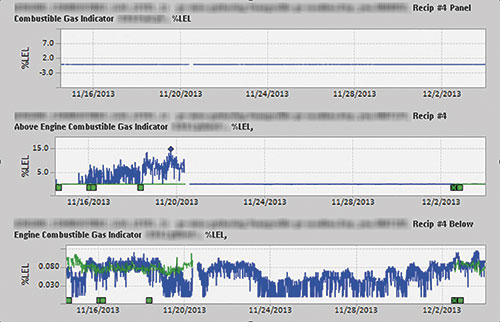
Above Engine Combustibles Issue
At another oil and gas facility, the software detected a gradual increase in the above engine combustibles reading on a reciprocating compressor. Given the engine speed on the machine, the above engine combustibles reading was expected to be 0.14 percent lower explosive limit (LEL). However, the actual reading was 13.0 percent LEL. The software provider notified the user of this fault through a high-priority email and began tracking the issue. The user investigated the problem and found a loose fuel header. The refinery team immediately tightened the fuel header to reduce the amount of combustible gases that were leaking.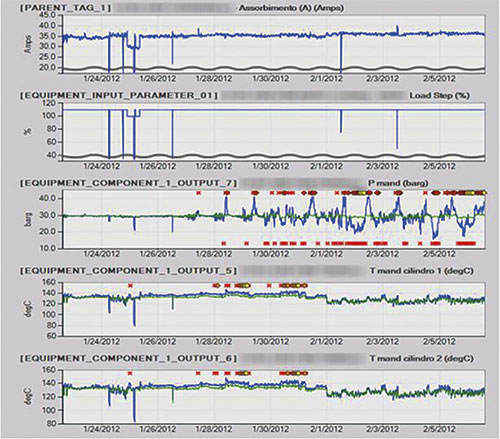