03/09/2016
When a pump operates far from its best efficiency point (BEP) flow—either to the right or to the left—vibration, cavitation, overload and damage to the equipment can result. The letter below is an example of a dialogue between a pump user and a pump consultant. Many end users have an intuitive feeling, based on experience, that something "just isn't right" in the system. But with a little help, they can determine the problem and any actions that may solve the problem. What initially appears to be confusing becomes clearer, providing a better foundation for a more systematic analysis.
Letter from a Reader
"I work on liquefied natural gas (LNG) tankers. My query is regarding a centrifugal pump running in one of the cargo tanks and supplying LNG to the forcing vaporizer. It has a capacity to pump 50 cubic centimeters per hour (cm3/hr). The pump is in the bottom of the tank, approximately 38 meters below. This spray pump is delivering LNG to the forcing vaporizer. The system consists of the spray pump connected to the spray line—to the forcing vaporizer and spray return line back to the tank. "The pump has a discharge valve and sends liquid to the forcing vaporizer through the spray line. You can set the delivery amps of the pump and the required pressure to be maintained in the system. Once the pressure in the system is set to, let's say, 250 kilopascals (kpa) and the pump amps are set to 29 amps, the return valve is around 20 percent open and returning liquid back to the tank to maintain pressure. Any fluctuation will cause the return valve to open or shut. "Now, if we set the amps on the pump to 37 amps, the discharge valve opens more and the discharge pressure is lower than above. When the amps were initially set lower, the discharge valve is open less and the discharge pressure is high. In this case, the spray return is also open less. "But when the amps are set higher, the discharge valve is open more and the discharge pressure is lower than above, but the spray return is open more. "My question is this: Is it efficient to run the pump with a higher back pressure? Will this damage the pump? I also think that running the pump with higher load and keeping the return open is not really running the system efficiently, but am I right? I look forward to your opinion." S.A. LNG Tankers Far EastNelik's Response
When talking about efficiency, the first thing we need to know is the BEP. You can get it from the performance curve, or you can make a simplified test at different flow rates to find out where efficiency peaks and whether you are running the pump efficiently.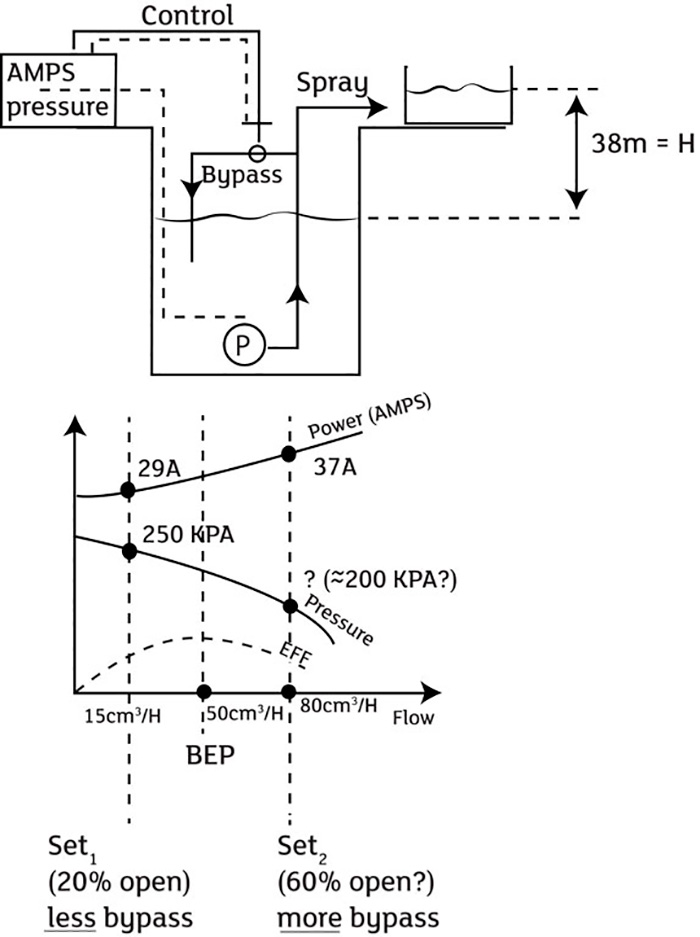
See other Pumping Prescriptions articles here.