The motor industry, represented by the National Electrical Manufacturer’s Association (NEMA), continues to expand motor scope and improve electric motors. Since the early days of the Energy Policy and Conservation Act (EPCA), the electric motor has played a key role in providing a catalyst of energy savings options. In the late 1980s, NEMA worked directly with the American Council for an Energy Efficient Economy (ACEEE) to draft legislative language providing direction to the secretary of energy to create the first ever motor efficiency rule.
NEMA has diligently moved forward, expanding the scope of covered motors from what was first defined in the Energy Policy Act of 1992 (EPAct) to the Energy Independence and Security Act (EISA) to add additional motors covered from general purpose to Type 1 and 2, while also increasing the required efficiency level from levels defined in NEMA MG 1, Table 12-11 (Energy Efficient) to NEMA Table 12-12 (Premium Efficient) for 1 horsepower to 500 horsepower general purpose motors.
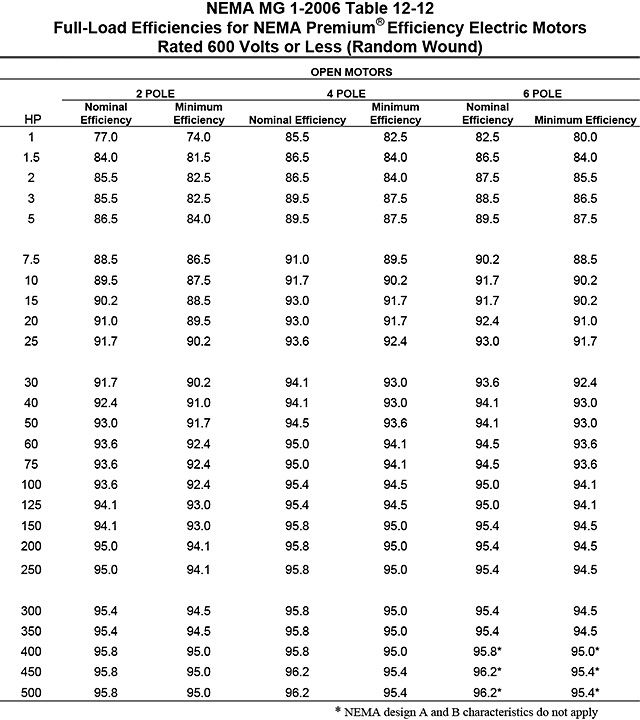
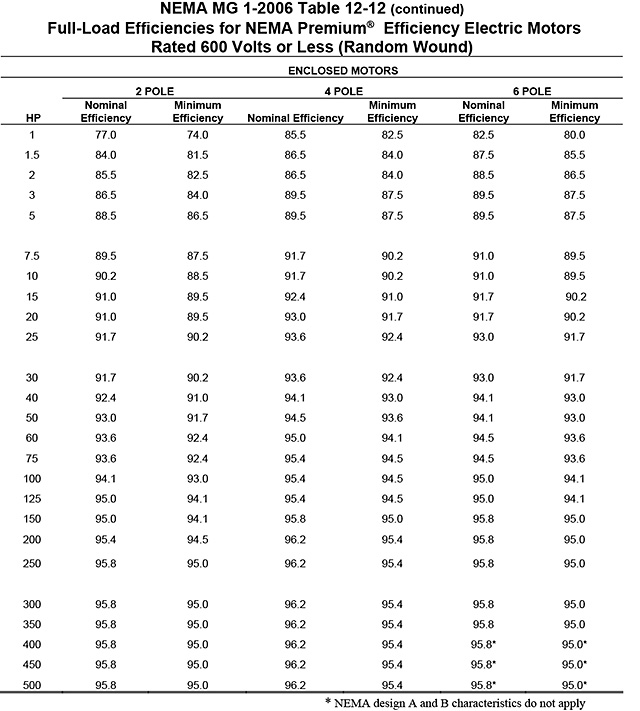
The results of NEMA’s efforts have placed the U.S. motor efficiency standards 20 to 25 years ahead of European motor standards that will be implemented in 2015 and 2017. One might think this track record of success would be sufficient—not for the NEMA motor generator section. The members have maintained an ongoing dialogue with ACEEE, which has helped add other stakeholders to the motor efficiency discussion. This relationship has resulted in the formation of the Motor Coalition, made up of the NEMA motor generator section, ACEEE and several other environmental groups focused on improving the efficiency of motors and motor-driven systems in the U.S.
MIT Study
The evolution of motor efficiency rules prompted additional support for a study recently completed by researchers within the Engineering Systems Division (ESD) at the Massachusetts Institute of Technology (MIT). Polyphase electric motors are responsible for an estimated 50 percent of global electricity usage, most significantly driving pumps, fans, compressors and other mechanical traction equipment. The International Energy Agency (IEA) estimates that 7 percent of global electricity demand could be saved through the use of higher energy efficiency motors. Limited research had previously been reported on the carbon footprint quantification and methodology development for motor products.
The NEMA members of the Motor & Generator Section (1MG) took part in this MIT ESD study to better understand and evaluate the electric motor’s carbon footprint. The study’s determination that 99.8 percent of electric motors’ greenhouse gas (GHG) impact is in the use stage confirmed the need for NEMA to continue programs supporting the application, design and selection of motors and motor-driven systems as a leading method of reducing GHG in the industrial and commercial market segments. The study determined that the GHG impact in the production of electric motors was 0.2 percent.
The NEMA Motor Generator section concluded that changes to the current federal motor efficiency regulations could be made to save additional energy through the use of NEMA Premium motors. NEMA estimates that the present federal rules cover slightly more than one third of the industrial and commercial polyphase motors currently sold in the U.S. as finished goods or imbedded in equipment.
NEMA’s Evaluation
NEMA evaluated the 1-horsepower to 500-horsepower market for motors sold in the U.S. In its evaluation, NEMA used data available from IMS consulting and the U.S. Commerce Department and valuable insights from other members of the Motor Coalition. The resulting view of the market showed that a significant number of polyphase motors were not currently covered. These products included categories, such as:
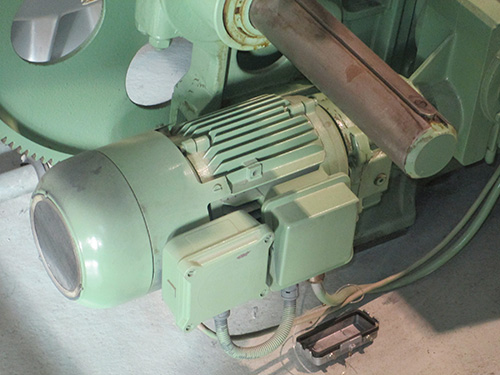
- Partial motors
- Gear motors
- Close-coupled pump motors
- Vertical, immersible, definite and special-purpose motors
The inclusion of these motor categories at the NEMA Premium efficiency levels was determined to add approximately 30 million connected horsepower to the already regulated 20 million connected horsepower. NEMA estimated that this change would save America 5.3 terrawatt-hours per year.
Motor Coalition Evaluation
The Motor Coalition next evaluated an “expanded product scope” concept to look at the potential energy savings and assess any performance or application risks that may befall motor users. Two points—performance and physical size—were reviewed.
Performance needs required that the expanded product scope be completed so that motors could maintain their electromechanical functionality. Motor users were concerned that increases in motor efficiency would change the performance and force the retrofit market to find alternatives to the higher efficiency motors. Second, the original equipment manufacturers (OEMs) and end users were concerned that increases in efficiency would force the motor suppliers to jump one frame size or add significant length to accommodate the additional copper, steel and aluminum needed to increase the motors’ efficiency, rendering the motor unusable in their applications.
The motor manufacturers explored design and technology options available to achieve the optimum energy savings while maintaining what the Department of Energy (DOE) refers to as “product utility.” The outcome of the evaluation was to increase the required nominal efficiency levels of the new motor rule to Premium Efficiency (Table 12-12) levels. The members of the section concluded that by moving virtually all polyphase motors to this level, a change could be achieved within two years of enactment of the federal energy code (CFR10, part 431).