An increasing number of industrial plants are reducing the spare parts inventories stored at their facilities. At the same time, they are replacing fewer pumps because of capital constraints and have determined that remanufacturing existing equipment is the best path forward. Many of the pumps within these facilities have exceeded 50 years of service. This drives the need for replacement parts and, in some cases, emergency replacement parts. Considering the age of these pumps, the replacement parts from the manufacturer are likely obsolete and may not be easily available. Further complicating the situation is the location of manufacture. Many cast parts are manufactured outside the U.S and have long lead times. To address these challenges, many companies are developing technologies to meet the specific and growing demands of the industry. Many of these advanced tools, including coordinate measure machine (CMM) technology, allow for quicker emergency repairs, faster deliveries and higher quality pump parts.
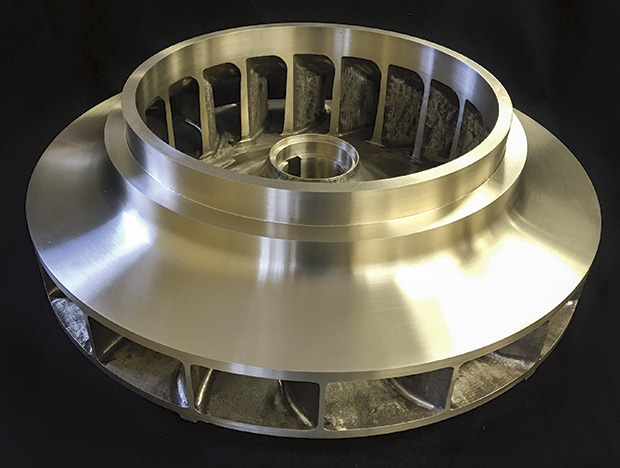
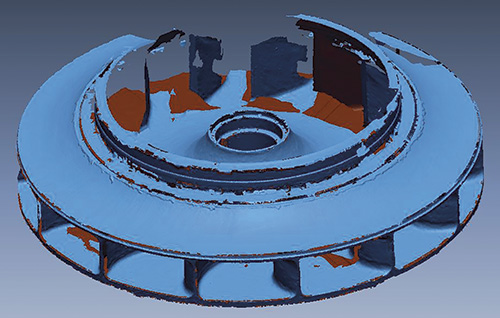
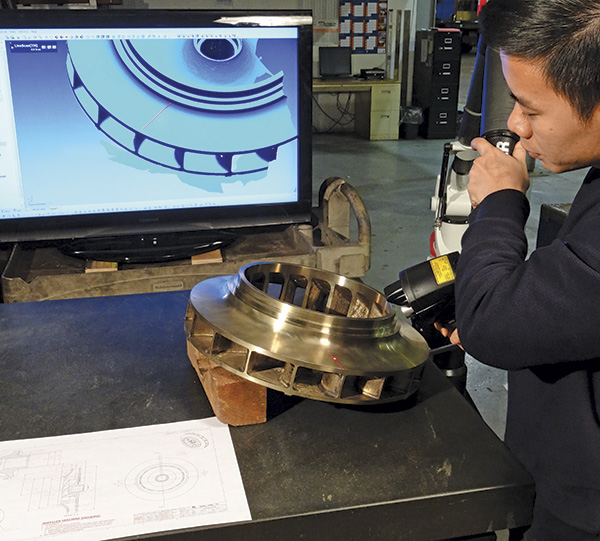
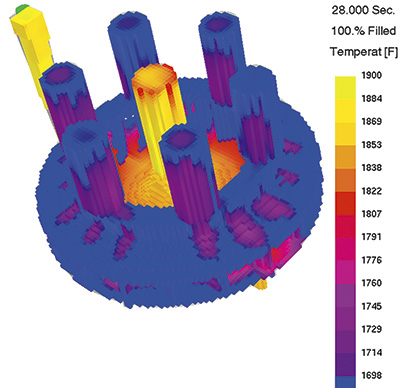
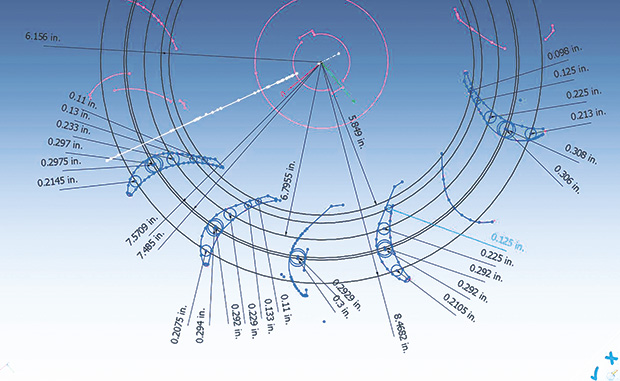
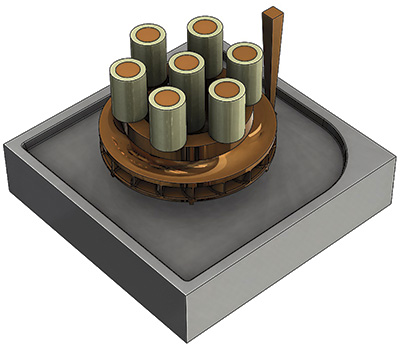
3 Benefits of New Spare Parts Manufacturing Processes
- New technologies are now available that can significantly benefit the procurement process. They can drastically cut spare parts lead times, making it possible to return critical pumps to service more rapidly.
- Studying how metal solidifies during the cooling process means that castings consistently meet the vane geometry specified by hydraulic engineers. This, in return, will save the end user money by operating the pumps within the optimum parameters.
- Scientific developments in additive manufacturing are allowing foundry engineers to make significant process changes in the way tooling is developed and castings are created. Since most major pump parts come from castings, pump users will continue to see improvements in critical areas such as price, delivery and quality of their spare parts.