Product development is arguably one of the most important pump industry processes. For pump original equipment manufacturers (OEMs), it accelerates organic growth and complements mergers and acquisitions. For end users, product development presents new opportunities to solve problems and lower life-cycle costs. Despite these benefits, developing innovative new products can be daunting. Successful product development, especially in today's dynamic process equipment industry environment, is more demanding than ever. It requires solving end-user problems with a compelling value proposition that drives down costs in tangible ways. It requires meeting new demands for greater energy efficiency and lower environmental impact while developing highly differentiated products that enable OEMs to gain competitive advantage and achieve targeted return on investment in record time. To meet this challenge, many companies are modifying the traditional phase-gate product development structure to incorporate an iteration-based approach designed to drive innovation through rapid learning cycles. They are combining this approach with systematic ways to generate and develop ideas. For end users, these new approaches to product development are leading to more innovative product solutions.

Traditional Phase-Gate Structure
In the traditional phase-gate development structure, a project is divided into phases and separated by gates. Each gate serves as a formal decision point for management to decide if and how the project will progress to the next phase. The traditional phase gate provides structure to the product development process, helps managers select the best projects and reveals major problems so they can be addressed before further investment. But in many cases, the traditional phase-gate structure can stifle the creativity needed to develop innovative products. The time allocated for creativity comes early—and only once—in the process before it shifts to the next phase. However, opportunities to generate high-impact ideas are available throughout the entire project.Iteration-Based Approach
An iteration-based approach combines the best elements of a phase-gate structure—high-level structure and management review points—with an iteration strategy. This combination enables development projects to become a series of mini-project cycles that includes comprehensive idea-generation with a design-make-test cycle of the complete product. Each iteration builds on the in-depth learning, discoveries and results of the previous iteration. The lessons learned from one iteration are used as a starting point for the next iteration to drive improvements and spark new ideas. In the early phases, these iterations are quick and typically involve creating concept prototypes from materials such as wood, plastic, cardboard, clay or other inexpensive quick-build materials. As the product design advances to the next iteration, the developers build prototypes with more refined and functional features that converge with higher resolution to the final design. When combined with a systematic way to generate and develop ideas, the iteration-based approach becomes a powerful way to compete based on innovation.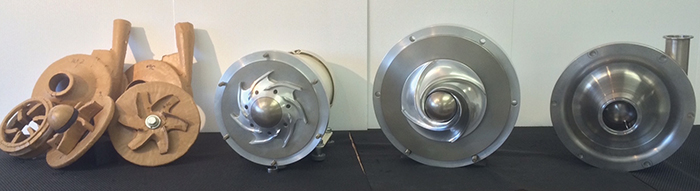
Idea Generation
Each iteration provides a structured yet flexible way to generate ideas, converge these ideas to the best alternatives and model the top ideas to bring them to life with further clarity. The idea-generation process starts with establishing the core product development challenge that will solve major end-user problems and enable OEMs to accelerate profitable growth. Only by raising the bar to seemingly impossible levels across several key success drivers can the idea-generation process have the foundation and context necessary for product line breakthroughs. Developers can design an idea-generation process, tailored to engineered machinery, to systematically find innovative solutions to the product development challenge. The process can be applied across a wide range of development activities—from high-level product design architecture to specific component design—and throughout all iterations of product development. The result is an ongoing flow of ideas that continuously improves the product's design, performance and cost in creative ways and allows the incorporation of late-breaking ideas. Brainstorming activity fuels the idea-generation process, and a visual environment—sketches, pictures and engineering drawings—displays ideas in full view so new ideas are inspired through cross-pollination..jpg)