Parallel operation is a setup in which two or more pumps take suction from the same suction header and deliver liquids into the same discharge header. In theory, if the two pumps and piping are identical in design, they should pump at approximately the same flow rate. However, differences in piping, pump performance and internal wear often lead to flow discrepancies in pumps operating in parallel. Indiscriminate parallel operation of centrifugal pumps may lead to significant flow imbalances that can result in pump vibration, pulsations, overheating and failure. Pump users should always confirm that pumps are similar in performance capabilities before operating them in parallel. Individual flow meters can help ensure that pumps are operating at a safe flow when in a parallel arrangement. A total flow meter for a group of pumps is more common. In one scenario, two centrifugal pumps—nine-stage, 125-horsepower (hp) vertical turbine pumps—are installed side by side. They transfer pipeline liquids collected upstream of a compressor station into another pipeline. These pumps were never intended to operate in parallel. Normally, one of the pumps can handle all liquids reaching the station.
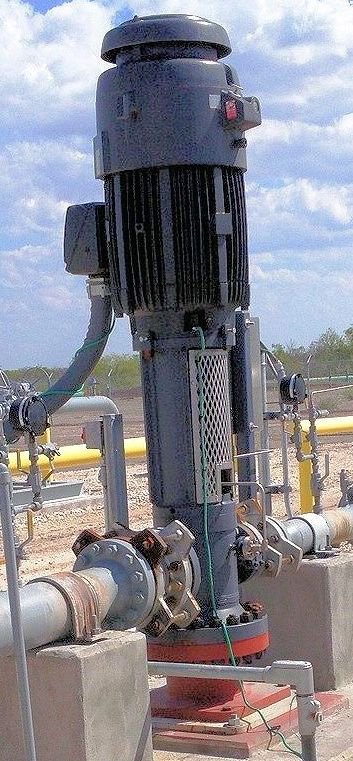
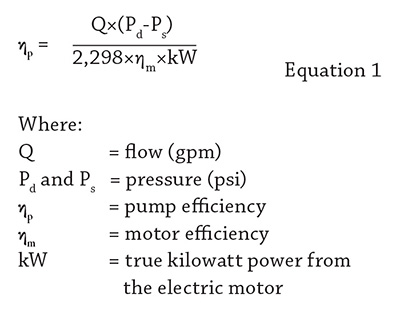
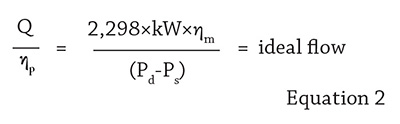
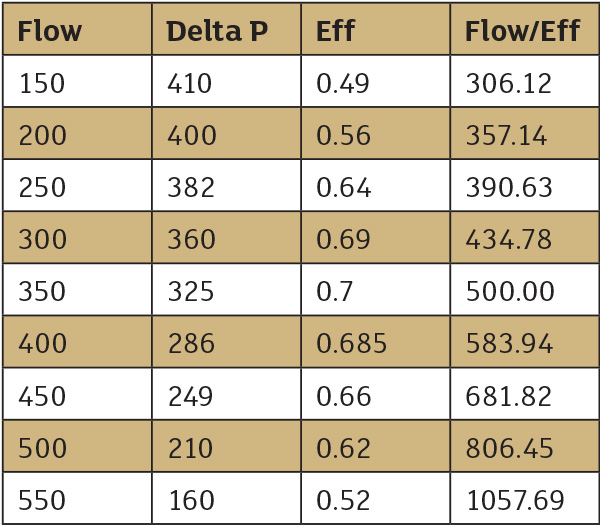
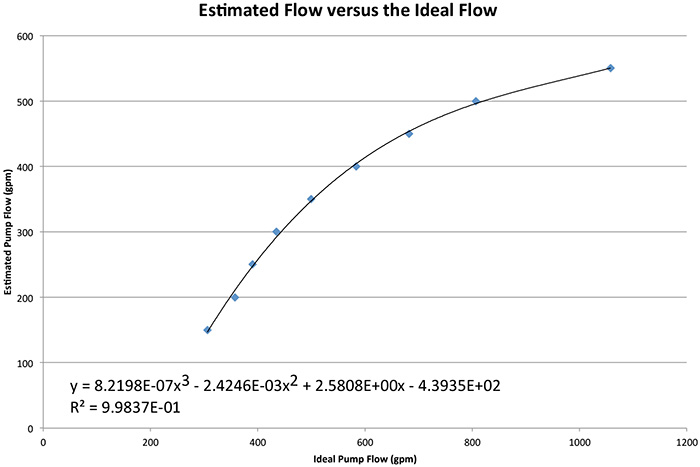
Results in the Field
Two new power meters were installed in the field, and their outputs were tied into a local PLC, along with pump suction and discharge pressures. The PLC was programmed to perform all calculations for an estimated flow rate.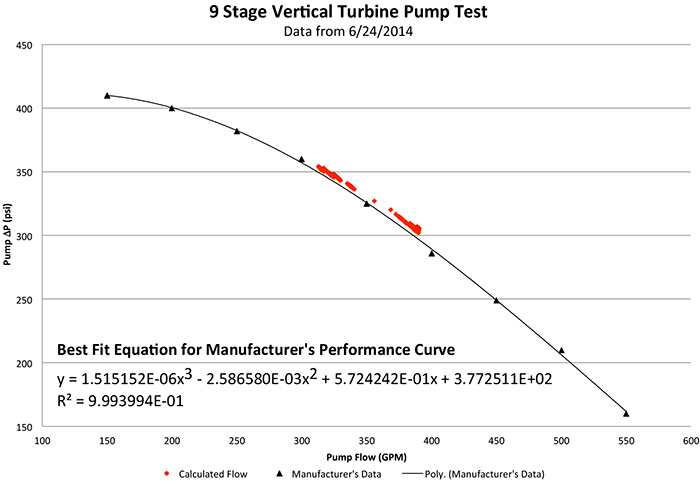