The facility partnered with an international nuclear energy services company to renovate and qualify four 12-foot, 24-ton pumps.
AREVA & Dominion Virginia Power
12/19/2016
For decades, the U.S. fleet of nuclear power facilities has efficiently and reliably generated low-carbon electricity. Inside each facility, reactor coolant pumps (RCPs) and other components play a critical role in creating this electricity. This equipment, however, operates for extended periods of time under harsh conditions. Eventually, these components need to be refurbished or replaced. The nuclear industry is constantly exploring innovative and efficient ways to complete these replacements and to ensure operational excellence. In 2015, Dominion Virginia Power completed one of the largest RCP refurbishment projects in the U.S. at the Surry Power Station in southeastern Virginia.
.jpg)
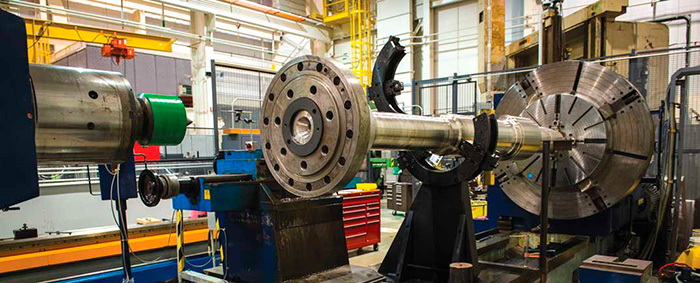
Deciding to Replace RCPs
In 2014, intergranular stress corrosion cracking (IGSCC) was found on turning vane bolts in a U.S. power plant. These bolts secure the turning vane diffuser assembly inside the RCP, located above the pump impeller. The original equipment manufacturer identified a problem with pumps manufactured with 1-inch-diameter turning vane bolts. After evaluating this issue, Dominion decided to upgrade and replace all its facilities’ RCPs that contained 1-inch-diameter turning vane bolts. At Surry, five RCPs were affected: two in Unit 1 and three in Unit 2. Dominion contracted the nuclear energy services company to refurbish the RCPs, including replacing the turning vane bolts. This work was performed in Unit 1 during the spring 2015 outage and Unit 2 during the fall 2015 outage.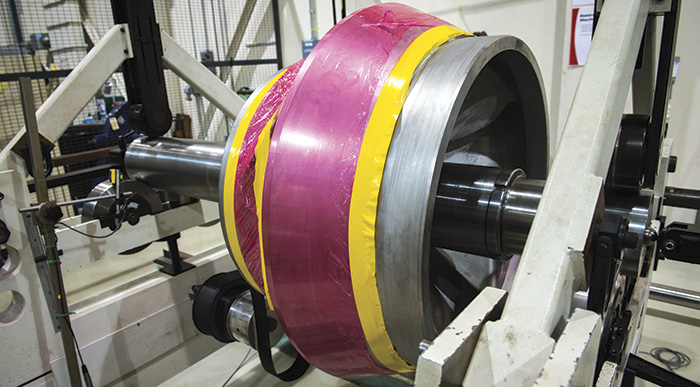
Overcoming Obstacles to RCP Refurbishment
With an aggressive outage schedule, spare pumps had to be obtained in 10 months—a monumental task when, historically, lead times to secure RCPs were two to three years. Faced with such a challenge, the nuclear energy services company looked into reclaiming two RCPs from Dominion’s retired Kewaunee plant in Wisconsin and refurbishing them to like-new conditions. This innovative idea presented significant challenges that needed to be addressed before the company could proceed with purchasing the pumps from Kewaunee:- Ownership: The ownership of the pumps had to be resolved. Kewaunee is part of the unregulated business at Dominion, but Surry is a regulated business facility. Moving assets from unregulated to regulated facilities required meeting certain regulations.
- Condition: The team had to determine whether the pumps were in a condition to support more than 20 years of service at Surry after operating for more than 30 years at Kewaunee. To be refurbished for another facility, the pumps could not be degraded.
- Codes and licensing: American Society of Mechanical Engineers (ASME) requirements vary from plant to plant based on state and date of construction. As a result, the team had to evaluate each state’s codes and standards to determine if the Kewaunee pumps were built to code requirements that satisfy those governing Surry.
- Physical interchangeability: A number of physical requirements had to be evaluated, including the size of the Kewaunee pump and the Surry pump casing, the Kewaunee pump flow rate and pressure compared with the Surry pump, the location of the interface for the motor (coupling, motor stand bolts), and the location of the piping connections (seal water, cooling water).
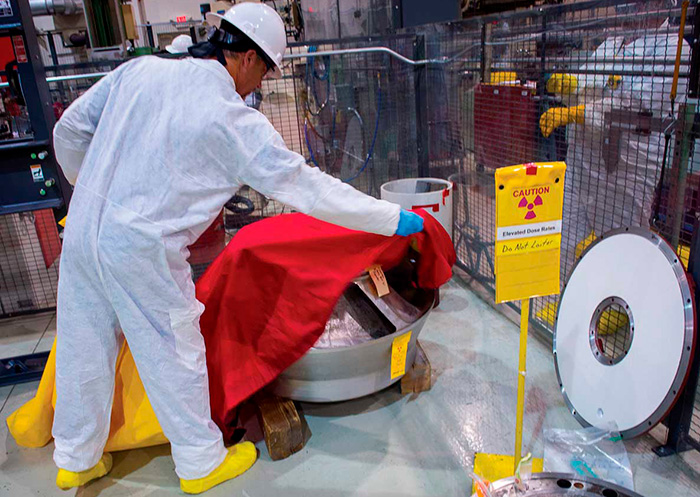
Undertaking the Refurbishment Project
The RCP refurbishment project included replacement of the shafts, impellers, couplings, bearings and all bolting on the pumps. The accelerated delivery schedule required the nuclear energy services company to manufacture these replacement parts in less than six months—a task that normally takes one to two years. Alongside the engineering and manufacturing efforts, the company’s field implementation teams planned the complex logistics of replacing multiple RCPs during a normal maintenance outage. The company’s pump and motor field service team and Surry’s maintenance technicians completed extensive mock-up training exercises, which were integral to the planning and preparation. This also led to the development of new and improved tooling and equipment..jpg)
Identifying & Integrating Lessons Learned
Project personnel learned several lessons throughout the process of refurbishing and qualifying the RCPs, including opportunities to integrate safety improvements, enhance outage excellence and innovate technologies in preparation for the next scope of work.Maintaining a Clear Focus on Safety
Five RCPs were refurbished and installed without any safety issues, personal contamination events or human performance errors. This performance is attributed to the team’s rigorous focus on safety, which was the No. 1 priority during the entire project. Using full-scale mock-ups for the RCP and machining activities, both management and crew members trained and performed all tasks based on field-like conditions. Ensuring team members experience radiation doses well within regulated limits is a key aspect of every project plan. Practicing critical tasks where expected radiation exposure is higher, such as removing and installing the RCP and the shield plug access cover on the mock-ups, allowed the team to explore best practices to reduce process time and to integrate new techniques that resulted in lowering expected REM dose exposure, also called achieving dose savings. REM is a standard unit of measurement for radiation dosage; it combines the amount of energy produced by the radioactive material with the medical effects of the given type of radiation.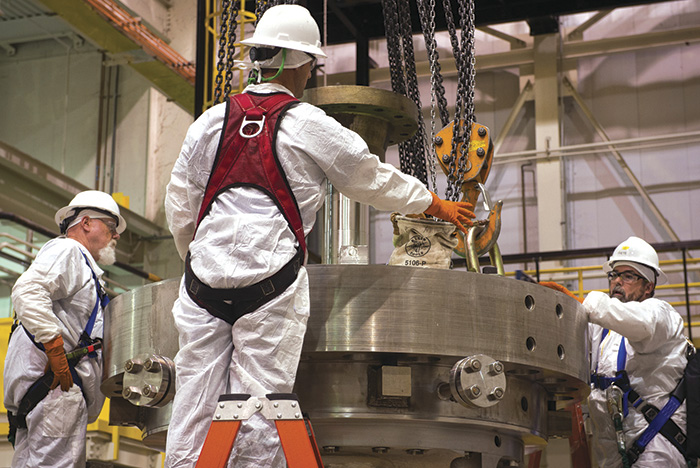
Enhancing Outage Excellence
Because timeframes for outages are decreasing at plants across the country, largely for economic reasons, the project team identified numerous ways to improve processes, incorporate best practices and develop solutions for equipment efficiency. By continually improving, the team maintained the outage schedule and stayed within budget. Improved communication between the field and project teams was critical to the success of the project. A key lesson learned and adopted early in the process was to organize the entire project team in the same working area. Having a unified base location eliminated communication delays and improved handoffs between teams..jpg)
Integrating Innovative Processes & Technologies
Improved processes and innovative technologies allowed the team to be proactive, which increased productivity and reduced critical path time and impacts to the schedule and other work groups. Innovative solutions for transporting and installing components also improved overall project performance. For instance, the nuclear energy services company designed a shielded transport RCP cask with one hook to up-end the large component. The cask’s smaller footprint and easy lift design simplified the process of repositioning the component, reducing polar crane and critical path time by eight hours per pump. Engineering innovations helped configure the unique style of Kewaunee’s pumps for Surry. Flow curves, piping configurations and thermal monitoring systems all required attention. Dominion worked with the nuclear energy services company to fabricate new shafts and impellers for the pumps to achieve flow requirements. Because of the RCP’s complex geometry, state-of-the-art digital measurement technology was used to measure the different dimensions of the pump components. Three-dimensional overlays of the new and old pumps identified possible deviations with more accuracy and speed than was previously possible through manual measurements.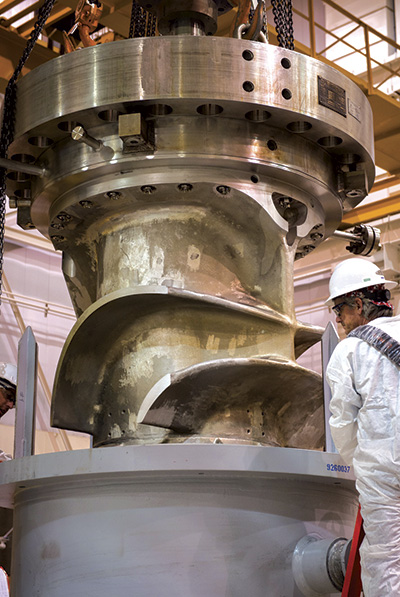