Is OEE (overall equipment effectiveness) as relevant a metric in today’s digital age as it has been in the past?” This question was posed to me recently, and I believe it is a legitimate one. I say this even though I’ve been an advocate of using OEE as a measuring stick ever since I helped implement the lean manufacturing program at Johnson & Johnson more than a decade ago. There has been heated debate for many years over the value of OEE, and I’ve found myself at times in some contentious discussions. Concerns about the lack of quality data sometimes used, the so-called “fudging” of numbers, and how OEE scores can be misused or misrepresented have resulted in disagreement among manufacturing experts on the merits of this tool. My answer remains: Yes, OEE is incredibly relevant today. In fact, I would say that its relevance now is as high or higher than it has ever been, because it remains a universal benchmark that applies across industries and countries.
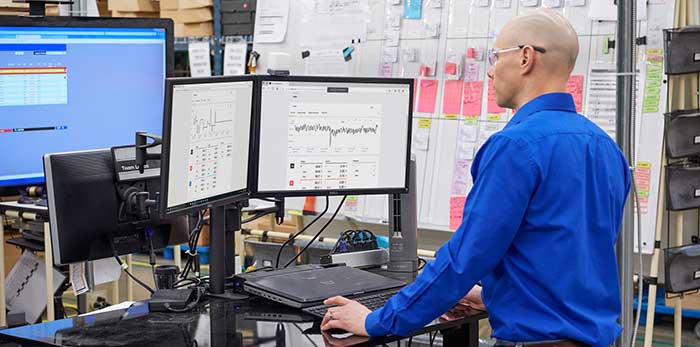
Defining OEE: Same as it Ever Was
OEE has its origins in the early 1980s as an outgrowth of the lean manufacturing movement and as part of the total productive maintenance (TPM) methodology adopted at many automobile and other manufacturing companies. It continues to be calculated by this equation: Availability x Performance x Quality = OEE score
- Availability = Run Time / Planned Production Time Availability accounts for all events that stop planned production long enough to qualify and track as downtime.
- Performance = (Ideal Cycle Time × Total Count) / Run Time Performance factors in anything that causes the manufacturing process to run at less than the maximum possible speed.
- Quality = Good Count / Total Count Quality accounts for manufactured parts that do not meet quality internal or external standards, including parts that need rework.