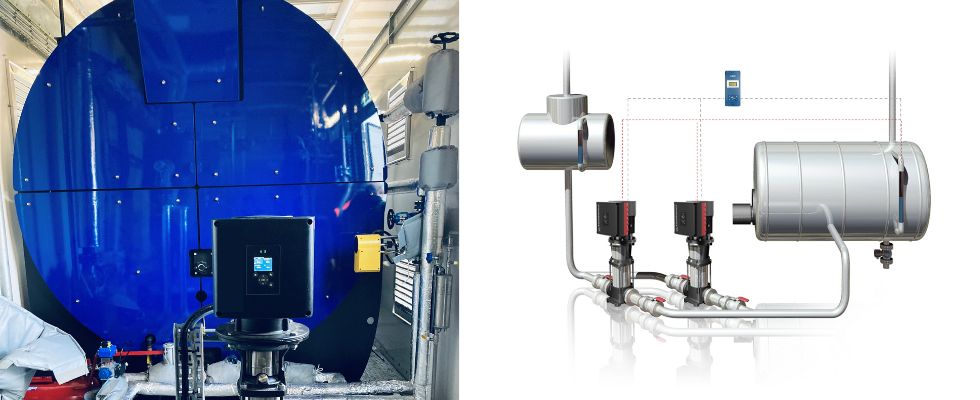
In steam boiler applications, maintaining a constant water level in the boiler drum is crucial for stable steam generation, high steam quality and reliable operations. Fluctuations in water levels can lead to thermal stress, reduced system life span and variations in steam production. An optimal boiler feed pumping solution delivers steady steam production, fast responses to changes in steam consumption, stable water levels, precise chemical dosing and energy savings.
It is also essential to have an intelligent and reliable data monitoring system to keep ahead of any warning signs. This article will cover four strategies for monitoring and controlling water levels to help users make the right decisions for their space, conditions and budget.
1. On/Off Control With Level Switch
The simplest strategy for controlling water levels in a boiler is turning the feed pumps on and off via a level switch. When the water reaches the designated level, the feed pump switches on or off based on input from a level switch. As the water level goes up and down, the pumps start and stop. This design is simpler and tends to be less expensive.
Advantages:
- It is cost-effective with a simple design.
- It is easy to implement and maintain.
Challenges:
- The sudden rush of cold water can reduce steam quantity and pressure.
- Temperature variations cause thermal stress, reducing system lifespan.
- Constant starting and stopping can strain the pumps.
2. Feed Valves With Level Sensors
The next strategy involves regulating the water level using feed valves controlled by a level sensor in the boiler. This allows a certain amount of water to enter the boiler depending on the actual steam consumption, resulting in a constant water level and steam pressure.
Advantages:
- It maintains constant water level and steam pressure.
- It offers more precise control compared to the simpler on/off approach.
Challenges:
- Continuous operation of feed pumps increases energy consumption.
- It requires a bypass loop to prevent shaft seals from overheating, which requires more space and energy.
- It adds complexity to the overall design, adding more opportunity for issues to arise.
- Feed valves can be expensive to maintain and may cause pressure loss.
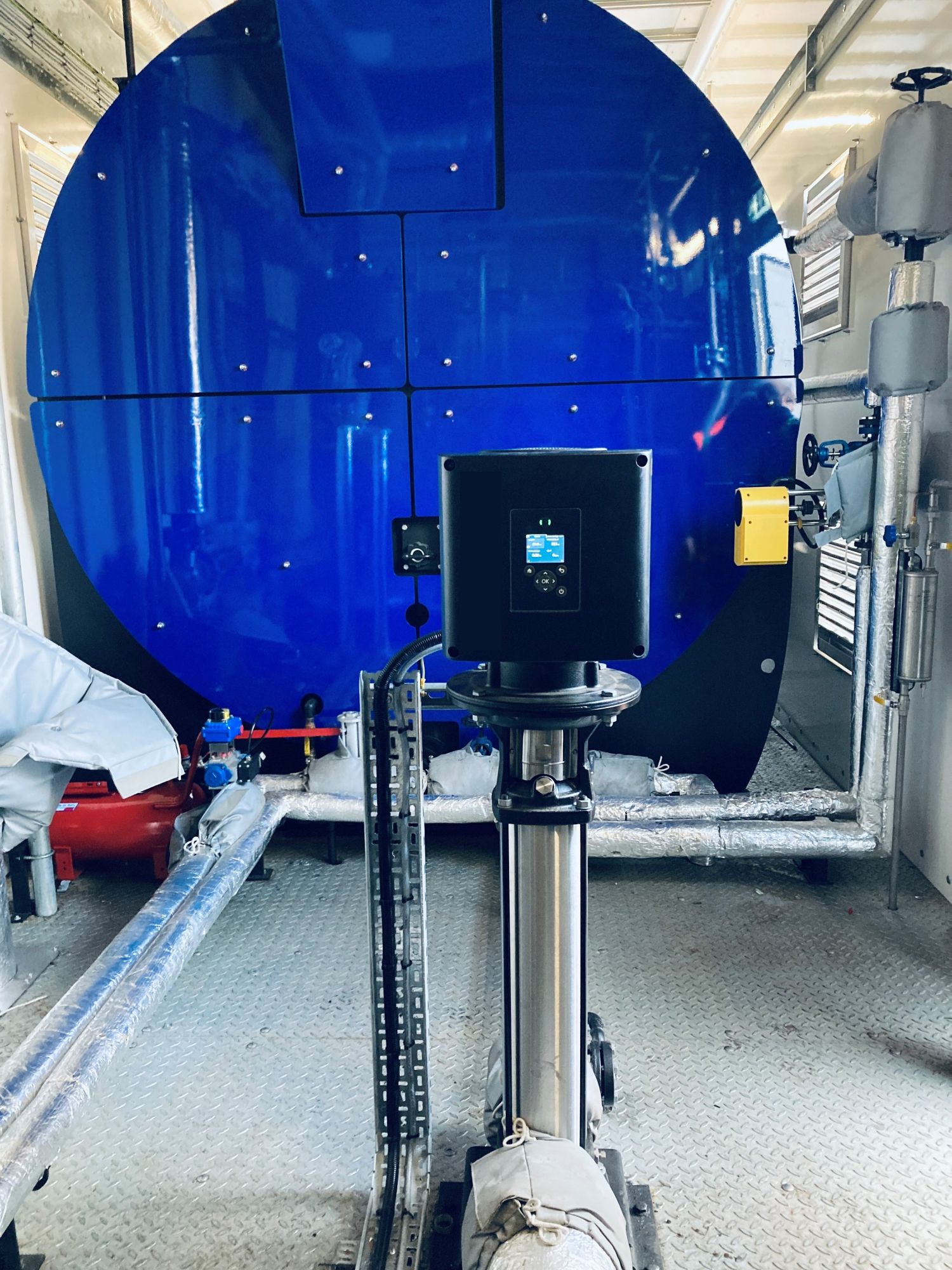
3. Variable Speed Pumps With Feed Valves
Another strategy to consider is utilizing feed valves along with variable speed pumps (VSPs). VSPs adjust their operation using signals from a pressure sensor located in front of the feed valve, minimizing the differential pressure across the valve. This results in reduced energy consumption on the pump operation.
Advantages:
- It reduces energy consumption by adjusting pump operation.
- It provides more precise control of water levels.
Challenges:
- It still relies on a bypass system and feed valve.
- It has similar drawbacks as previous strategies, including complexity and maintenance costs.
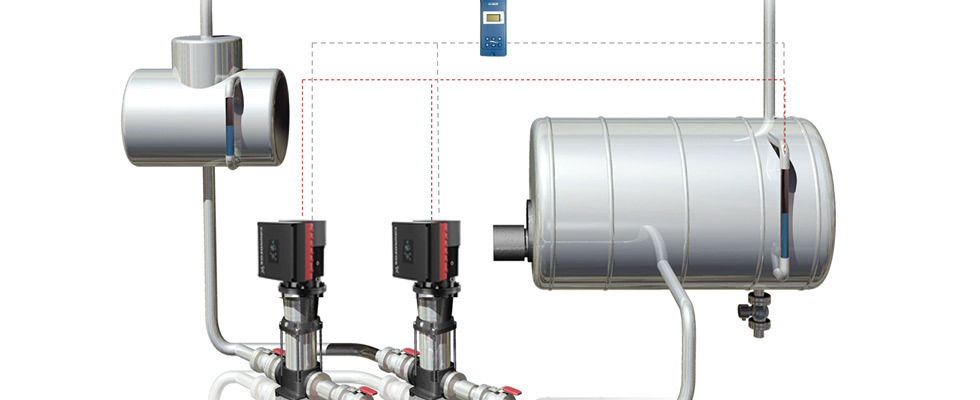
4. Direct Control With VSPs
Lastly, there is an option to monitor and control the water level in a boiler without adding valves or a bypass system. By using VSPs to control the water level, feed valves become redundant. The pumps adjust their operation according to real-time demand, resulting in smooth operation, reduced system complexity and significant energy savings.
Advantages:
- It eliminates the need for feed valves and bypass systems.
- It reduces system complexity and maintenance costs.
- It produces significant energy savings due to more efficient pump operation.
Consider a boiler system with a steam production of 20 tons per hour at 16 bar, a pressure loss across the feed valve of 5 bar at 100% boiler load and a standard load profile. The annual energy savings can exceed 20,000 kilowatts per hour (kWh). It is also possible to size for a pump with fewer stages and a smaller motor because the pump no longer has to compensate for the loss of pressure across the valve. This means the energy savings of direct boiler feed are equal to the cost of a new expensive feed valve, including maintenance, every year.
For boiler systems with high feedwater temperatures, an air-cooled pump is ideal, as it can handle temperatures of up to 180 C. Standard pumps cannot cope with such high temperatures. This is particularly useful in systems with economizers, which transfer energy from exhausts to the water, significantly increasing water temperature.
Additionally, electronic pumps (e-pumps) are equipped with high-efficiency motors and integrated frequency drives designed to operate efficiently at full load operation at ambient temperatures up to 60 C. They require less cooling, ensuring the system stays fully operational even in the hottest conditions. Unlike standard frequency drives that need to be derated when they go above 40 C, motors with permanent magnet technology generate less heat, allowing them to maintain full shaft power at higher temperatures.
Maintaining a constant water level is essential for efficient and reliable boiler operation. While traditional strategies have their place, using variable speed pumps without feed valves offers a simpler, more energy-efficient solution. This approach not only reduces system complexity but also provides energy savings and improved performance under challenging conditions.
By exploring these strategies and understanding their advantages and challenges, users can optimize their boiler feed systems for better performance and efficiency.
References
- grundfos.com/us/learn/ecademy/all-courses/boiler-systems/efficient-level-control-in-steam-boilers