Discover which systems need work and how to justify expenses.
WEG
08/30/2017
The term system optimization is widely known, but how many people truly understand what it means? Total system efficiency has been a real challenge for the industrial sector to embrace.
Lack of Standards Hinders Configuration
Except for a few standards for package boilers, there are no system standards. What does this mean, and how does this impact your plant bottom line? Anyone can design, configure and specify a pumping system, but no one can say it is incorrect without a system standard (ASME, ISO, ANSI, HI). In my 45+ years in the pump industry, I can count on one hand the number of pump systems that were properly configured. Given the focus on energy efficiency and sustainable growth in today’s industry, system optimization should be addressed in every pump system specification in some way, shape or form. The Hydraulic Institute defines system optimization as: The process of identifying, understanding and cost effectively eliminating unnecessary losses while reducing energy consumption and improving reliability in pumping systems, which while meeting process requirements, minimizes the cost of ownership over the economic life of the pumping systems.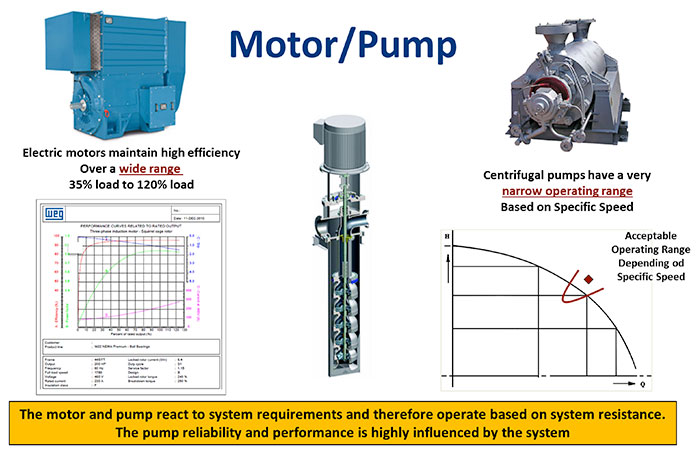
Why Focus on Pumping Systems?
A pumping system’s efficiency is highly influenced by the system it is supplying; therefore improving pump or motor efficiency will do little to reduce pump energy use. The focus must be on the entire system because the motor and pump react to the system (see Figure 1). The motor has a wide operating range maintaining high efficiency to as little as 50 percent load. The pump has a rather narrow operating range (depending on specific speed) and will lose efficiency quickly. Unfortunately, total system efficiency is rarely addressed when specifying a new system. The first focus is typically on cost, which is not the most cost-effective approach when specifying a pumping system. Consider the life cycle cost of a typical 75 horsepower pumping system (see Figure 2).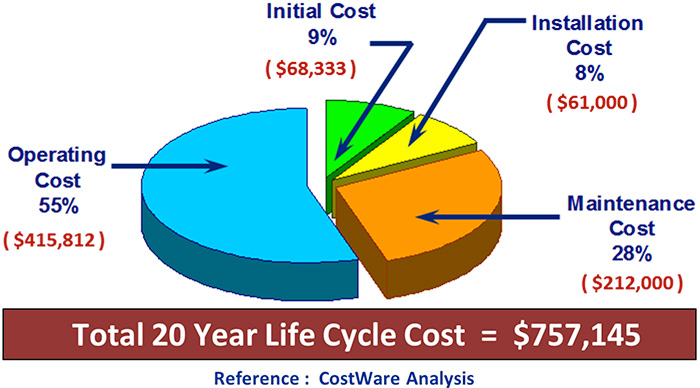
Existing Systems
Chances are high that the existing pumping systems in your plant are less than optimal. There is a very simple process for identifying “bad actors” by following The Hydraulic Institute’s six step action plan for evaluating existing pumping systems: 1. Screen and prioritize your pumping systems to identify good performance improvement candidates. Working as a team (operations, maintenance engineering, purchasing), identify pumps that have required an excessive amount of maintenance or resulted in lost production, as well as systems that require further analysis. Hydraulic Institute has a pre-screening form that you can download from their website to assist in the screening process. Priorities for detailed investigation include:- systems that are controlled by throttling valves
- systems where several pumps are normally run in parallel
- systems with frequent on/off cycling of a pump in a continuous process
- systems with no flow, pressure or power indication
- pump systems with high energy use (large motors that run continuously or frequently)