More than 30 years of machinery studies have reinforced that almost 90 percent of all machinery failure modes occur randomly—making failures of pumps, motors, compressors, gearboxes, fans and other equipment essentially unpredictable. However, warning flags of a failure in progress can often be detected by changes in the operating conditions of equipment. If the warnings are detected and addressed quickly, the problems may be fixed before the failure occurs. This is the fundamental principle behind predictive maintenance. Predictive maintenance is a proactive strategy to identify and repair machinery problems before they escalate to full-failure modes. Supported by diagnostic tools, software and remote monitoring technologies, the strategy has largely replaced time-based maintenance and run-to-failure approaches. Some bottom-line reasons for this replacement are:
- The direct cost of machinery repairs because of breakdowns can be at least three times greater than the cost of planned repairs
- The production outage time needed to complete an emergency repair can be up to five times more time than required for a planned repair.
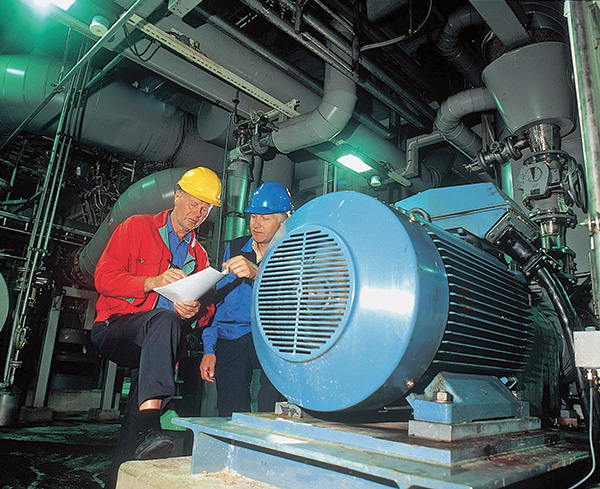
Initiating an MHRP
An MHRP as a vibration-based maintenance service program is engaged through the provider’s authorized distribution network and designed to build on the strengths of each partner—the service provider’s expertise in maintenance strategies and predictive maintenance and a distributor’s inherent knowledge about the customer’s operations and onsite logistics. The service provider contributes the technologies and expertise to collect data regarding the health of machinery at the facility and delivers reliable analysis, reporting and remedial recommendations. Equipped with ample warning, operators can be aware of problems in advance and take proactive measures to prevent catastrophic machinery failure, which is the purpose of predictive maintenance programs. This type program is especially well suited for operations with established goals of:- Reducing maintenance costs
- Production requirements that must be achieved
- Up to 500 critical and interdependent rotating production machines
- Equipment for which high repair or replacement costs can be expected