Hydraulic applications are challenging to seal. Not only must the hydraulic seals prevent fluid leakage from the cylinder, but they also must withstand high pressures, extreme temperatures and transverse forces within the cylinder. Additionally, hydraulic systems require a complex combination of specialized seals, rather than a single seal. Hydraulic rod seals prevent fluid leakage from within the cylinder to the outside while hydraulic piston seals prevent fluid from flowing across the cylinder head. This allows pressure buildup on one side of the piston, making the cylinder extend or retract. Wear rings guide the piston and piston rod within the hydraulic cylinder, absorbing transverse forces and preventing metal-to-metal contact. Scrapers or wipers remove dirt, chips or moisture from the piston rods as they retract into the cylinder, preventing contamination.
.jpg)
Offshore Hydraulic Sealing
The same principles apply to hydraulic sealing whatever the application, but offshore sealing systems must stand up to extreme pressures, destructive process chemicals and marine environments. In addition, sealing materials need to meet industry standards such as American Petroleum Institute (API) and NORSOK while being able to respond to an ever-changing technological horizon. As wells increase in depth and processing grows more aggressive, the working conditions for seals and bearings become more demanding. Avoidance of downtime is a key aspect as the costs associated with this in the oil industry can be huge. Close collaboration between operators and equipment and sealing suppliers is vital in ensuring long seal life and minimized downtime. One of the most important factors in successful seal specification is understanding the conditions in which the equipment will operate. This way, the sealing system can be matched to specific requirements in terms of pressure, temperature and, most significantly, media compatibility. Process chemicals can destroy seal materials if not correctly specified. In terms of materials, options include basic acrylonitrile butadiene polymer (NBR), perfluoroelastomer (FFKM) compounds or polytetrafluoroethylene-(PTFE)-based seals, which compatible with virtually all media and polyethylenes. Seal geometries are as important as material because each seal within a hydraulic sealing configuration has a specific job to do. The geometries, which have evolved and been enhanced over many years based on application experience, allow the seals to provide a specific function within the sealing system to meet the varying demands of differing applications. For instance, downhole tools need solutions that withstand extreme temperatures and aggressive media. They require a sealing system to give extended life to allow oil and gas extraction from the lowest depths; reliability and leak-free operation are critical. For tensioner cylinders, a 20-year or longer maintenance-free seal life is sought to prevent downtime and revenue loss. In hydraulic swivels, increasing speeds and pressures call for innovative and unique seal designs that give low-friction operation.Proven Solutions
There is a wide range of proven sealing options available to the oil and gas industry. Elastomer materials must meet temperatures and be compatible with system media. For the offshore industry, elastomers are often used with other materials such as PTFE-based compounds; the elastomer provides the elasticity and the PTFE has low friction properties. In high-pressure dynamic sealing applications, elastomers can be supported with polyetheretherketone (PEEK) anti-extrusion rings.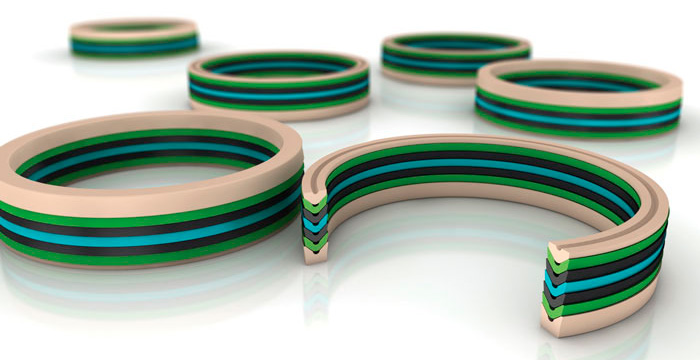